Best Practice Montage und Logistik
Moderne Montagesysteme sind in der Lage, komplexe und variantenreiche Produkte zu wettbewerbsfähigen Kosten herzustellen. Sie beherrschen Einzelfertigung und Kleinserien und sind flexibel bezüglich Stückzahlschwankungen. Dies gilt in differenzierter Form auch für die Serienfertigung.
Die Unternehmensberatung EFESO verfügt über das dafür notwendige Instrumentarium:
Mit ROM®, der ROI-Operationsfolgemethode, wird auf Basis der Stückliste ein verschwendungsfreies Montagesystem in kurzer Zeit simuliert. Optimale Montagezeit und Potenzial liegen damit fest.
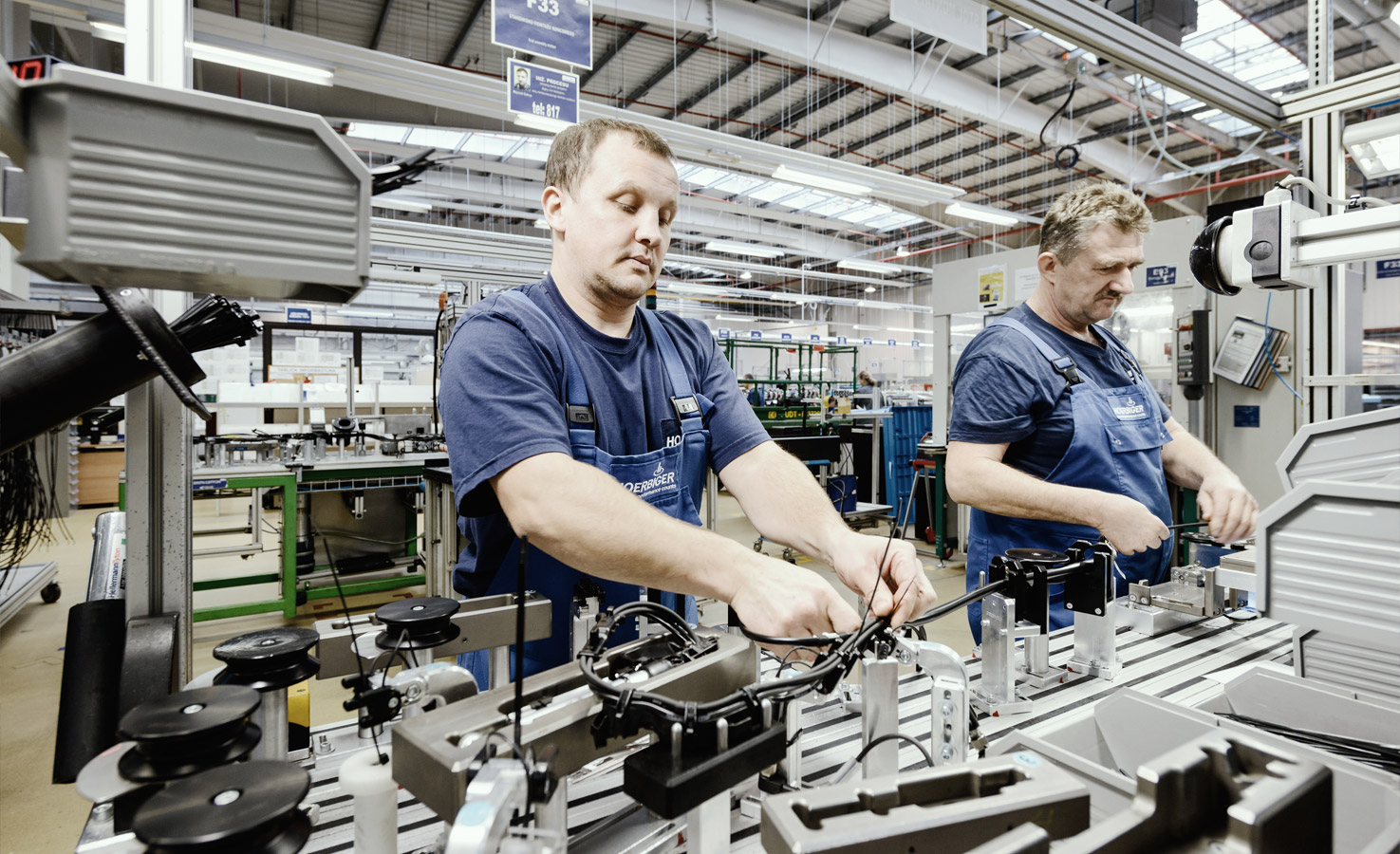
Das Montagesystem selbst wird aus einem Best-Practice-Baukasten entwickelt, der sich an den folgenden Grundprinzipien orientiert:
- klare Trennung von Montage und Logistik
- Einführung One-Piece-Flow
- flexible Abtaktung
- optimale Abgrenzung und Integration von Vor- und Endmontage
- sinnvolle Automation, Low Cost Intelligent Automation
- Nutzung von Industrie 4.0-Technologien
- Pull-Prinzip und flexibles Umrüsten in der Teilebereitstellung
- standardisierte Nachschubprozesse
- modulare und nutzungsneutrale Montagesystem- und Arbeitsplatzgestaltung
- teamorientierte und kapazitätsflexible Organisationskonzepte
- Ergonomisch gestaltete Arbeitsplätze
- Elektrostapler vs. Dieselstapler (CO2-Thematik)
- Digitalisierung als Basis von effiziente und somit Ressourcen schonenden Prozesses
- Arbeitssicherheit (Unfälle, Gefahrstoffe, …)
Zusätzlich kann ROM® wertvollen Input zu Fertigungs- und montagerelevanten Aspekten liefern, die bereits in der Phase der Produktgestaltung berücksichtigt werden sollten.
KONTAKT