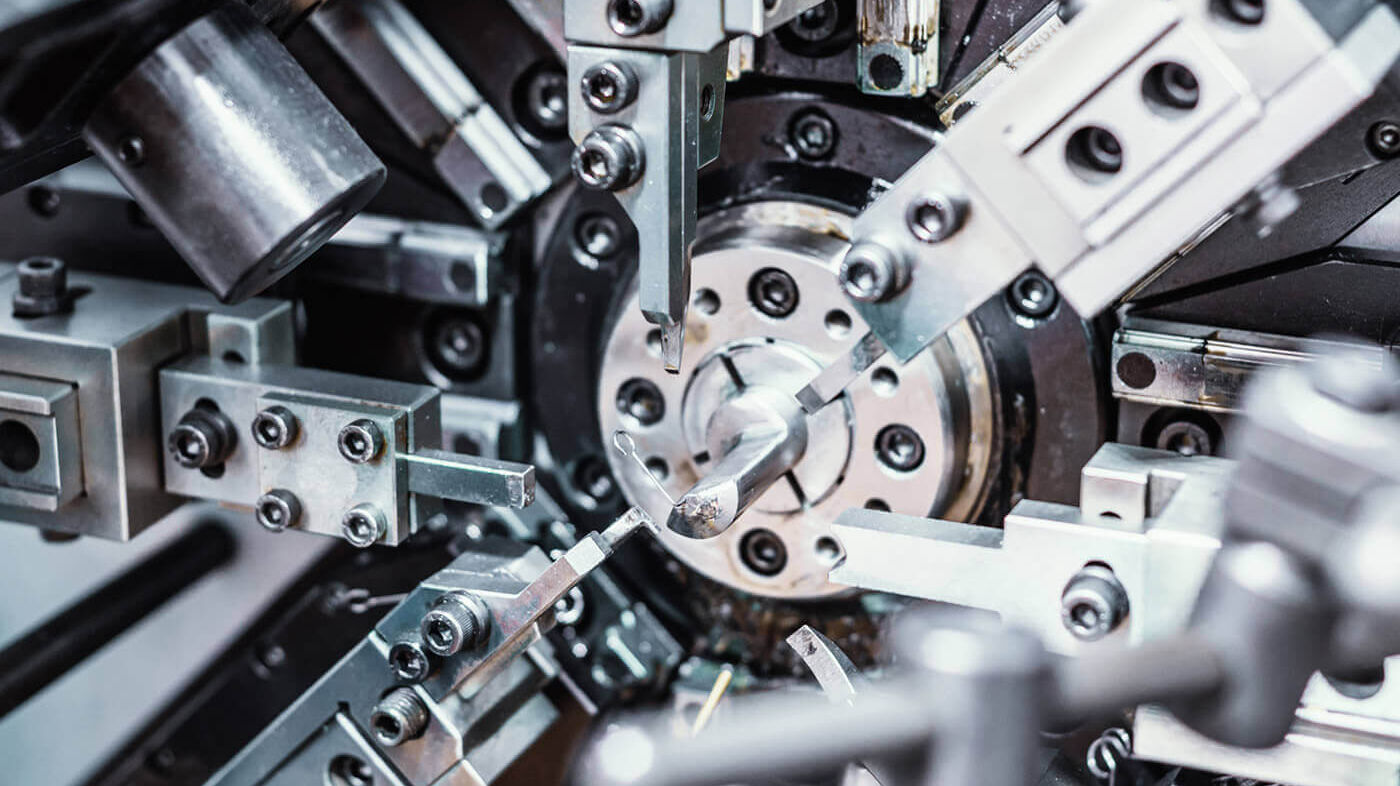
Restrukturierung und Kostensenkung im Maschinenbau
Den Turnaround meistern
Gute Bilanzen können Komfortzonen schaffen. Auf Attacken von Konkurrenten reagieren? Die Flexibilität bei Nachfrageschwankungen erhöhen? Vielleicht in fünf Jahren. Ist die Bedrohung dann plötzlich besonders groß und akut, reagieren viele Unternehmen gerne mit drastischen Maßnahmen an einer oder wenigen Stellen. Nachhaltig ist das meist nicht. Es geht aber auch anders, wie ein EFESO-Projekt zur Restrukturierung eines Unternehmens aus dem Anlagen- und Maschinenbau zeigt. Dieses packte alle dringend notwendigen Veränderungen an und kam so wieder auf Erfolgskurs.
Herausforderung
Vertriebserfolge sicherten einem Unternehmen im Anlagen- und Maschinenbau eine Pole-Position im Wettbewerb. Doch die war extrem gefährdet: eine signifikante Margenerosion bei unverändertem Umsatz und fest eingefahrene Strukturen erforderten gravierende Veränderungen in kurzer Zeit.
MEHREFESO Lösungsansatz
Anstatt nur die offensichtlichsten Brandherde zu löschen, identifizierte EFESO an einem Fertigungsstandort in Deutschland alle Stellschrauben für die notwendigen Veränderungen und brachte mit einem vielschichtigen Restrukturierungsansatz den Turnaround ins Laufen.
MEHRLessons Learned
Für einen nachhaltigen Turnaround sind nicht nur Teilbereiche, sondern der Aufbau der gesamten Werksorganisation auf Herz und Nieren zu prüfen. Zudem ist Transparenz schmerzhaft, aber wichtig. Nur klare Verantwortungsbereiche, Zahlen und Fakten helfen effektiv weiter.
MEHREFESO Erfolgsmodell
Mit einem neuen Fertigungskonzept, Kostensenkungen durch standardisierte Prozesse und Design-to-Cost-Maßnahmen senkte das Projektteam die Material- und Fertigungskosten in anderthalb Jahren so erheblich, dass die langfristige Wettbewerbsfähigkeit des Werkes gesichert ist.
MEHRDass Behaglichkeit zum erheblichen Risikofaktor für das eigene Überleben werden kann, registrierte unser Kunde gerade noch rechtzeitig. Über Jahrzehnte fertigte er an einem Standort in Deutschland Anlagen für die Prozessindustrie. Die Vertriebserfolge sicherten dem Unternehmen eine globale Marktführerschaft – solange das Geschäft nicht gezielt von Konkurrenten angegriffen oder durch stärkere Schwankungen in der Kundennachfrage destabilisiert wurde.
Geringe Flexibilität, falsche Prioritäten
Aber natürlich passierte genau das. Und natürlich passierte es gleichzeitig: Mehrere Produkte erwiesen sich nicht mehr als ausreichend wettbewerbsfähig, da Konkurrenten qualitativ vergleichbare, aber günstigere Anlagen offerierten. Dass sich die Komfortzone der Marktführerschaft in Gefahr befand, zeigte sich jedoch vor allem in einer signifikanten Margenerosion bei unverändertem Umsatz. Zudem rutschte das Werk schon bei geringer Unterauslastung in die Kostenunterdeckung. Vor allem hohe Fixkosten senkten die Flexibilität bei Nachfrageschwankungen. Ohnehin bremsten viele fest eingefahrene Strukturen in der Arbeitsorganisation das Potenzial zum effizienten und effektiven Wirtschaften: Supportfunktionen wie Logistik, Instandhaltung oder Qualität waren mehrfach vorhanden, Synergien zwischen zentralen Funktionen wie Arbeitsvorbereitung und Disposition blieben ungenutzt, und die Fertigungsorganisation sorgte für einen mangelhaften Ausgleich der internen Kapazitäten. Die Führungsmannschaft hatte das durchaus registriert, aber anderen Themen eine höhere Priorität eingeräumt. Schließlich stimmten die Zahlen ja am Ende immer – irgendwie. Und irgendwer würde sich dem Thema schon irgendwann annehmen, oder?
Sechsfacher Weckruf zum Turnaround
Bereits beim Projektstart war also klar, dass der Weckruf laut und das Erwachen aus der Komfortzone entsprechend hart ausfallen müssten, um den Turnaround zu schaffen. Genau genommen waren dazu sogar mehrere Weckrufe notwendig: Das Unternehmen hinterfragte den Aufbau seiner gesamten Werksorganisation und definierte klare Verantwortungsbereiche, etwa bei der Absatzplanung. Durchleuchtete Materialfluss, Anlagenstruktur und Investitionen. Prüfte Beschaffung und Outsourcing auf Herz und Nieren. Führte Shopfloor-Management ein und sorgte dafür, dass Effizienz in den Mittelpunkt des Tagwerkes rückte. Stellte die Prozesse und IT-Systeme von Auftragsverwaltung, Entwicklungs- und Support-Funktionen auf den Prüfstein und entwickelte die passenden IT-Konzepte für Standard- und F&E-Produkte. Und koordinierte all dies in einem übergeordneten Projekt- und Änderungsmanagement, das die Wirksamkeit der Maßnahmen in den genannten Teilprojekten im Blick behielt.
Kostensenkungen dank Transparenz
Eben diese Vielschichtigkeit der Restrukturierung brachte das Projekt schnell auf Erfolgskurs. Anstatt nur Teilbereiche aus der Lethargie ihrer Routinen zu reißen, drehte ein Projektteam mit zwölf Mitgliedern gleich an allen Stellschrauben für die dringend notwendigen Veränderungen: Für die genannten Bereiche gab es je eine verantwortliche Führungskraft aus dem Werksteam, die mit einem entsprechend spezialisierten EFESO-Berater zusammenarbeitete. Klare Funktionen, Zahlen und Fakten erwiesen sich dabei an einigen Punkten zwar als schmerzhaft, aber notwendig für einen nachhaltigen Turnaround.
Flucht in Richtung Effizienz
Ein solcher Punkt waren zum Beispiel die Vorgabezeiten in der Fertigung. Hier mussten zahlreiche Anpassungen vorgenommen werden: Das Projektteam bewertete u. a. Änderungen im Fertigungsprozess und am Produkt sowie den technischen Fortschritt verschiedener Anlagen zeitlich neu. Dies bewirkte in Summe eine Zeitreduktion um 10%. Parallel dazu baute das Team das Shopfloor-Management auf, um zu einer strukturierten Problemlösung zu gelangen.
Wettbewerbsfähigkeit gesichert
Nicht nur in dieser Hinsicht kam ein Weckruf an. In gut anderthalb Jahren erreichte das Projektteam weitere beachtliche Erfolge: Es implementierte ein KPI-System mit Review-Meetings sowie eine neue Kapazitätsplanung so erfolgreich, dass sich das Verhältnis der produktiven Stunden pro Mann/Monat im Vergleich zu 2015 signifikant verbesserte. Das neue Fertigungskonzept, Kostensenkungen durch standardisierte Prozesse und Design-to-Cost-Maßnahmen reduzierten die Material- und Fertigungskosten so erheblich, dass die langfristige Wettbewerbsfähigkeit gesichert ist. Damit ist der Anlagenbauer auf zukünftige Marktveränderungen bestens vorbereitet.