Im Projekt-Setup sammelt EFESO alle nötigen Informationen und schafft damit die Basis für alle folgenden Schritte der Produktindustrialisierung. Dazu zählen insbesondere das Know-how über den vorhandenen Produktentstehungsprozess und über bekannte Lücken. Wichtig sind zudem Informationen zur Organisation, zum Projektmanagement sowie zu den Merkmalen der IT-Infrastruktur.
Produktindustrialisierung und Ramp-up Management
Mit „Industrialisierung“ wird im Kontext eines Produktentstehungsprozesses (PEP) die Phase der Überführung eines Produktes von der Entwicklung in die Serienproduktion bezeichnet. In dieser Phase integrieren Unternehmen ein Produkt oder eine Produktidee in ihre Fertigungslinie(n).
Dies umfasst unterschiedliche Aufgabenstellungen. Neben der Optimierung des Produktdesigns für die Massenproduktion sind z.B. geeignete Maschinen und Anlagen auszuwählen. Zudem gilt es, die Herstellungsrichtlinien und Qualitätsstandards zu entwickeln sowie die Mitarbeiter zu qualifizieren. Die klassischen Zielsetzungen der Produktindustrialisierung sind, Produktionskosten zu senken, Durchlaufzeiten zu verkürzen und eine konsistente Qualität der Produkte zu gewährleisten.
In der PEP-Praxis wird dieses wichtige Thema jedoch häufig nicht angemessen berücksichtigt. Das zeigt sich z.B. in mangelhaft gestalteten Schnittstellen zwischen der Projekt- und Serienorganisation sowie zwischen Werksstandorten. Im „Worst Case-Szenario“ führt dies zu verspäteten Serienanläufen, unnötigem Ausschuss und zusätzlichen Kosten, etwa durch ungeplante Extraaufwände (Taskforces) oder Sonderfahrten. Die Wirtschaftlichkeit des Produktes kann also schon zu Beginn des Produktlebenszyklus gefährdet sein.
Lücken im PEP schließen
Um die Herausforderungen der Produktindustrialisierung – einschließlich des Produktanlaufs/Ramp-up – zu lösen, kombiniert EFESO die folgenden Maßnahmen in einem speziell auf dieses Thema zugeschnittenem Ansatz:
- Mit einem detaillierten Fragenkatalog ermitteln und quantifizieren wir anhand von 250 Fragestellungen die Lücken im PEP in zwei Dimensionen: Erstens, welchen Reifegrad weist die aktuelle Produktindustrialisierung auf? Zweitens, wie steht es um die tatsächliche, im Arbeitsalltag gelebte Realität?
- Dies zeigt den konkreten Handlungsbedarf im PEP auf, da somit Abweichungen von Best Practice-Standards messbar sind. Die spätere Anwendung des Fragenkataloges verdeutlicht die Fortschritte. Zudem vermeiden wir somit ineffiziente „Brainstorming Workshops“: Anstelle subjektiver Meinungen soll bei diesem Vorgehen vor allem Faktenwissen ausgetauscht werden, um den bestmöglichen PEP herzuleiten.
- Darauf aufbauend schließen wir die identifizierten Lücken und nutzen dazu Best Practice-Erfahrungen für einen zielgerichteten und zeitsparenden Ablauf (z.B. 3P-Workshops, APQP). Mit der Durchführung von „Change Readiness Assessments“ berücksichtigen wir von Anfang an die Veränderungsbereitschaft der Mitarbeiter und entwickeln maßgeschneiderten Roll-out-Leitlinien für das Change Management und die Mitarbeiterqualifizierung.
Lösungswege nach Kundenbedarf
Unser Ansatz basiert auf den Erfahrungswerten und Ergebnissen aus Kundenprojekten, wird kontinuierlich von uns weiterentwickelt und in den Projekten zur Produktindustrialisierung an die Situation und die Ziele des Unternehmens angepasst. Dabei profitieren unsere Kunden von einem strukturierten und effizienten Vorgehen in den folgenden Projektphasen.
Produktindustrialisierung: Ansatz von EFESO
Baseline identifizieren
Status quo ermitteln
Mit unserem 250 Fragen umfassenden Fragenkatalog ermitteln wir crossfunktional die Lücken und Schwachstellen im PEP. Dabei berücksichtigen wir zwei Dimensionen: den aktuellen Implementierungsgrad sowie die „gelebte“ Reife. Dass ein Prozess beschrieben und geschult ist, bedeutet schließlich nicht automatisch, dass er auch angewandt, weitervermittelt und verbessert wird.
Prozesse und Trainings definieren
Im Zuge eines „Change Readiness Assessment“ erfasst das Projektteam die Veränderungsbereitschaft der Organisation. In crossfunktionalen Workshops schließen wir nun die ermittelten Lücken, vor allem über diese Maßnahmen:
- Definition und Darstellung neuer und vorhandener Prozessschritte im PEP
- Prozessbeschreibung (Input, Aufgabenbeschreibung, Output, Teilnehmer, Tools, Templates etc.)
- Definition der RACI-Matrix der Prozesse
- Abgleich des Umsetzungsgrads geschlossener Lücken im PEP über unseren Fragebogen
- Bestimmung des prozessseitig notwendigen Trainingsbedarfs sowie des Transformationskonzepts und -bedarfs; Erstellung entsprechender Dokumente und IT-Voraussetzungen, z.B. Workflows
Prozess einführen und Mitarbeiter coachen
In der Umsetzungsphase konzentrieren wir uns auf das PEP-Training und das Change Management. Dies beinhaltet u.a. eine klare Definition eines Masterplans für die Veränderungsschritte sowie zur Ergebniskontrolle. Alle Aktivitäten berücksichtigen hier die Ebenen faktischer Veränderung (z.B. Definition und Verankerung neuer Prozesse und Verantwortlichkeiten) sowie mentaler Veränderung (z.B. kontinuierliche Überwachung und Unterstützung des gesamten Change-Prozesses).
Erfolgsfaktoren: Produktanlauf (Ramp-up) beherrschen
- Prozesse und Standards detailliert und zugleich verständlich beschreiben
- crossfunktionale Teams und lokale Ramp-up Manager aufbauen bzw. weiterentwickeln
- effektive Controlling-, Reporting- und Steering-Instrumente identifizieren und etablieren
- Risikomanagement intensivieren, z.B. proaktives Erkennen von „Late Changes“ fördern
- Management Attention sicherstellen, etwa hinsichtlich der Einhaltung von Prozessen, Priorisierungen, Eskalation
- transparenten End-to-End-Wertstrom realisieren, dabei Lieferanten und (End-)Kunden einbeziehen
Erfolgsfaktoren: Neuen PEP implementieren
- den PEP einfach, klar, eindeutig und vollständig gemeinsam im crossfunktionalen Team gestalten
- Nachvollziehbarkeit und Zugänglichkeit des PEP sicherstellen, wofür die verantwortlichen Mitarbeiter die entsprechenden IT-Tools (Software) beherrschen müssen
- Identifikation der Mitarbeiter in ihrer Rolle und Verantwortung mit dem Prozess ermöglichen bzw. fördern
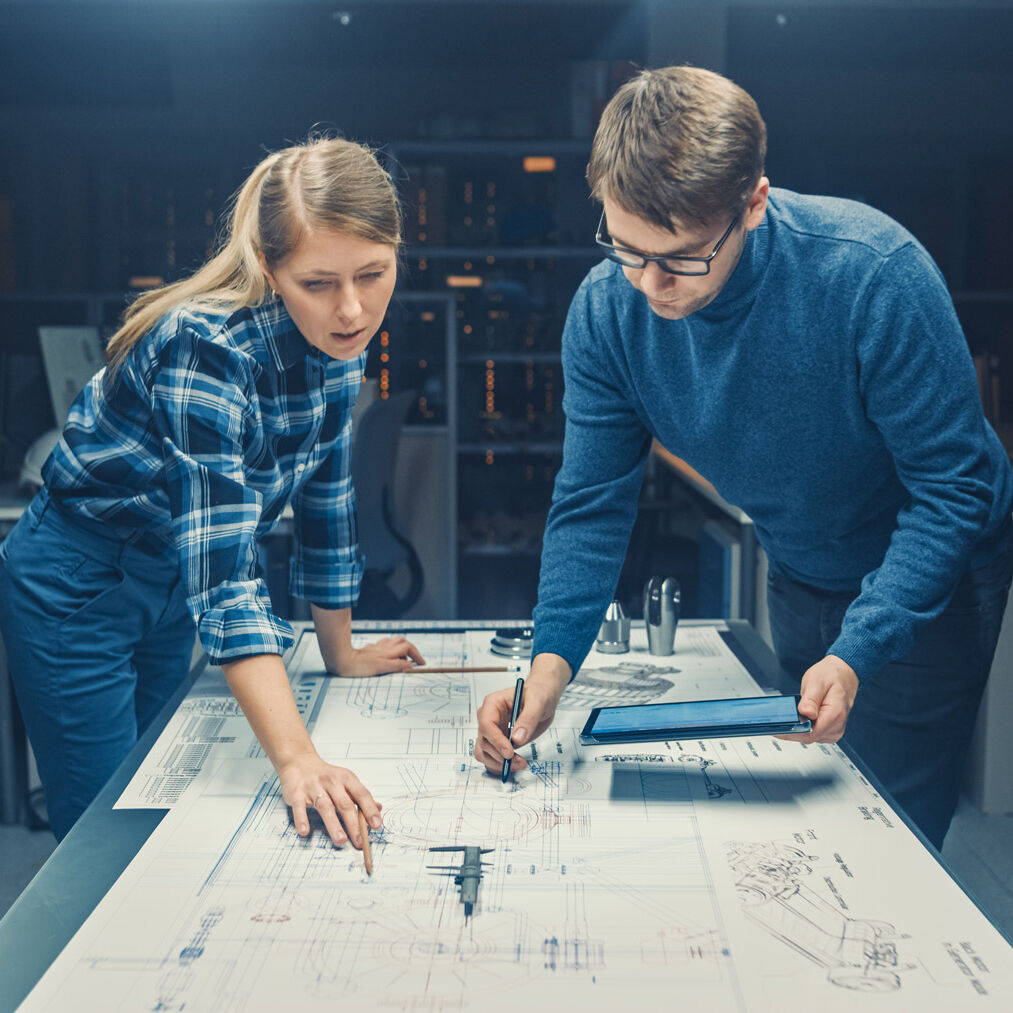
Projekt: Konzeption und Realisierung eines robusten, effizienten und standardisierten PEP inkl. Produktindustrialisierung und Ramp-up Management bei einem Tier 1-Zulieferer (ca. 10.000 Mitarbeiter weltweit).
Ergebnisse:
- Vollständige Behebung der Lücken im bestehenden PEP nach einem Jahr, v. a. in Bezug auf die Produktindustrialisierung.
- Weltweiter Rollout des neuen PEP inkl. Implementierung / Mitarbeiterschulungen.
- Werke sind im PEP mit eingebunden und übernehmen frühzeitig durch lokale Ramp-up Manager und Teilprojektverantwortliche mit Industrialisierungsverantwortung.
WEITERE LEISTUNGEN