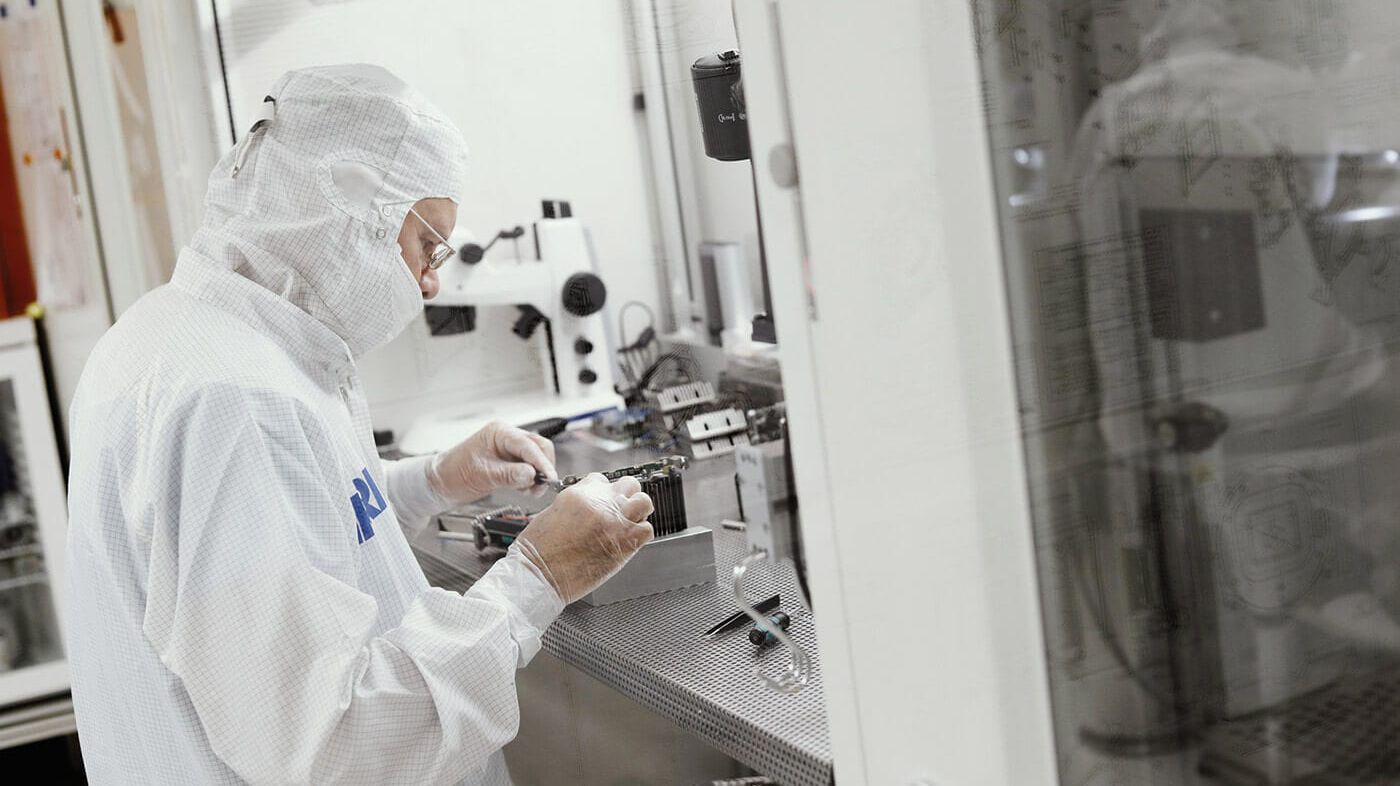
Qualität in der Produktion
Neue Horizonte für das Qualitätsbewusstsein
Höchste Qualitätsansprüche gehören in der Pharma- & Lifesciences-Industrie zum Tagesgeschäft. Ein Hersteller von Medizintechnik wollte die Fehlerquote in einer Fertigungslinie elektrischer Spezialpumpen mit einem verbesserten Qualitätsmanagement um den Faktor 10 reduzieren. Gemeinsam mit EFESO identifizierte das Unternehmen die passenden Ansatzpunkte und sorgte für Qualitätssteigerungen, die auch auf andere Produktlinien skalierbar sind.
Herausforderung
Ein Medizintechnik-Unternehmen musste die Fehleranzahl in der Fertigungslinie eines seiner Top-Produkte um den Faktor 10 musste reduzieren. Strenge Marktregularien schränken die Wahl der Mittel ein.
MEHREFESO Lösungsansatz
Eine genaue Analyse brachte die zentralen Fehlerquellen ans Tageslicht. In Workshops schuf EFESO zudem die Rahmenbedingungen für eine neue Arbeitskultur, die das Verantwortungsbewusstsein des Teams für Qualitätsverbesserungen stärkt.
MEHRLessons Learned
Kultur-Diskussionen zu konkreten Maßnahmen in allen Hierarchieebenen führen. Mitarbeiter:innen dazu motivieren, Verbesserungschancen zu finden und anzuwenden. Verantwortung für Qualität nicht auf einen Punkt fixieren, sondern auf viele Schultern verteilen.
MEHREFESO Erfolgsmodell
Transparenz diente in diesem Projekt als Schlüssel zur Veränderung. Im Mittelpunkt standen der Material- und Informationsfluss in der Linie sowie ein neuer Blick der Mitarbeiter:innen auf ihre Qualitäts- und Fehlerkultur.
MEHRIn der Medizintechnik sorgen strenge Zertifizierungsvorgaben für die Sicherheit der Patienten. Vom Zahnbohrer bis zum Kernspintomographen durchläuft jedes Produkt einen langen Zyklus aus internen und unabhängigen Tests, bevor es in Europa nach einer Konformitätserklärung mit einer CE-Kennzeichnung versehen oder in den USA nach Vorgaben der Food and Drug Administration (FDA) zum Verkauf freigegeben wird. Danach müssen u. a. genaueste Qualitätskontrollen in der Fertigung sicherstellen, dass keine fehlerhaften Geräte beim Patienten zum Einsatz kommen. Sobald ein Produkt allerdings eine CE-Kennzeichnung besitzt und FDA-zertifiziert ist, lässt sich die Auswahl und Gestaltung von Bauteilen, Kabeln oder kleinsten Schrauben im Fertigungsprozess nicht so einfach umstellen wie in anderen Branchen – jede kleine Veränderung kann erst nach einer erneuten, entsprechend zeitintensiven Überprüfung und Freigabe des kompletten Produktes durch die Behörden erfolgen.
Qualitätskontrolle mit hohen Ansprüchen
Unter diesen Rahmenbedingungen muss das Qualitätsmanagement in der Produktion von Medizintechnik besonders viel leisten, denn viele Fehler lassen sich nicht einfach durch konstruktive Änderungen aus der Welt schaffen. In diesem Fall hatte ein europäischer Hersteller von elektrischen Spezialpumpen in den Fertigungslinien seines Top-Produktes bereits eine umfangreiche Qualitätsprüfung etabliert. Doch dass nur makellose Geräte an die Kunden ausgeliefert wurden, genügte dem Unternehmen noch nicht. Das Management wusste: Montagelinien nach bester Lean-Manier auf Effizienz und Effektivität zu trimmen, ist nur eine Seite der Medaille. Die andere besteht darin, auch in den Prozessen zur Qualitätskontrolle ständig kleine Verbesserungen zu realisieren, die in Summe die Qualität steigern und ebenfalls viel Zeit und Geld einsparen. Die Kunst liegt allerdings darin, diese Punkte zu identifizieren und schnell im Fertigungsalltag umzusetzen.
Fehlerquellen ans Tageslicht bringen
Genau dieser Aufgabe widmete sich das Projektteam, das sich aus EFESO Berater:innen und den Projektverantwortlichen aus F&E, Fertigung und Qualitätsprüfung zusammensetzte. Vom COO des Unternehmens erhielt das Team eine klare Zielvorgabe: die Fehlerzahl im Montageprozess der Pumpen um den Faktor 10 reduzieren. Dies sollte zuerst in einer Fertigungslinie mit neun Montageinseln erfolgen und dann später von zwei weiteren Linien adaptiert werden.
Montagefehler sind vorprogrammiert
Im ersten Schritt identifizierte das Projektteam die Fehlerquellen bzw. Hauptfehlergruppen in der Vormontage und Montage der Spezialpumpen. Dabei zeigte sich etwa, dass falsch gesteckte Kabel und Schläuche für eine sehr hohe Fehlerquote sorgten. Die Mitarbeiter:innen in der Linie müssen pro Pumpe etwa 70 Kabel stecken – 70 sehr dünne, minimal gekennzeichnete und gleichfarbige Kabel. Montagefehler sind somit vorprogrammiert.
Poka Yoke ist keine Option
Zur Behebung dieser Fehlerquellen waren nun allerdings Lösungswege bzw. Prinzipien wie Poka Yoke, die das Design oder die Konstruktion des Produktes ändern, aus den genannten Gründen ausgeschlossen. Der Aufwand, neue, verbesserte Modellgenerationen erneut durch die strengen Zulassungsprozesse zu schleusen und zur Verkaufsreife zu bringen, ist schlichtweg höher, als Produktfehler intern im Fertigungsprozess zu beheben.
First-Pass-Yield Rate enthüllt Schwächen
Im Falle der Spezialpumpenmontage tolerierte das Unternehmen daher eine First-Pass-Yield Rate von 80 Prozent in der Qualitätsprüfung. Das bedeutet: Von 100 Geräten passierten 80 die finale Qualitätskontrolle ohne Beanstandungen, 20 mussten repariert werden. Bei Volumina von mehreren tausend Geräten pro Jahr ein ernstzunehmendes Problem. Zumal nicht nur die Qualitätskontrolle und Instandsetzung der „Rückläufer“ Zeit und Geld kosteten, sondern auch das Fehler-Reporting sowie nicht bezifferbare Verluste durch versteckte Nacharbeiten.
Wege zur Qualitätssteigerung
Nachdem das Unternehmen mit EFESO in der Analysephase die wichtigsten Fehlerquellen klar benannt hatte, konzentrierte sich das Projektteam auf drei Stoßrichtungen für die Verbesserungsmaßnahmen: Arbeitsmittel, Quality Gates und eine neue Arbeitskultur.
Maßnahmen zur Fehlervermeidung umsetzen
Eine detaillierte Analyse der Top-Fehler gab Hinweise darauf, wo entlang der Montage und Vormontage sich einfache Fehler schnell vermeiden ließen: Wie wird das Material beigestellt? Wie gestaltet sich der Montageablauf? Anhand dieser Erkenntnisse konnte das Projektteam u. a. Montagevorrichtungen und -anweisungen umgestalten und Fehlerquellen mit anderen Werkzeugen, Schablonen oder Hilfsmitteln für die Arbeitsschritte schnell beseitigen.
Einführung von Q-Gates
Trotz einer umfangreichen Überprüfung der fertiggestellten Geräte im Rahmen der finalen Qualitätskontrolle am Ende der Montagelinie wurden beim nachgeschalteten Dauerlauf bei ca. 20 Prozent der Pumpen Fehler entdeckt. Das Projektteam installierte deshalb an allen Montageinseln so genannte Q-Gates, in denen der Montageumfang der jeweils vorgelagerten Insel überprüft wird. Fehler werden somit entdeckt, bevor weitere Montageschritte am Gerät erfolgen. Die unmittelbare Fehlerbehebung durch den Verursacher schärft dabei ebenso das Qualitätsbewusstsein wie die Visualisierung aller aufgetretenen Fehler an jeder Montageinsel: Welche klassischen Fehler sind aufgetreten? Nahm deren Anzahl zu oder ab? Wird das Fehlerziel eingehalten? Was waren die häufigsten Fehler?
Arbeitskultur spürbar verändern
Auf dieser Basis legte das Werksteam bereits in den ersten Tagen dieser Projektphase die passenden Verbesserungsmaßnahmen gezielt und schnell fest. Der größere Vorteil dieser Vorgehensweise liegt jedoch an einer anderen Stelle. Zuvor sah das Team nur alltägliche „Einzel“-Fehler, die tatsächlichen Problemzonen der systemischen Fehler jedoch nicht. Die Arbeitskultur musste sich also dahingehend ändern, systemische Fehler klar zu benennen, statt mit Ausflüchten schönzureden. Denn wer direkt die wirklich wichtigen Probleme angreift, erzielt schneller größere Effekte in der Qualitätsverbesserung.
Qualitätsbewusstsein geweckt
In Change-Management-Workshops zeigte EFESO daher dem Team, wie es die eigenen Sinne für eine solche Arbeitsweise schärfen kann. Auf der Führungsebene, etwa im Kontext einer übergeordneten Change Initiative: Wie soll unsere Zielkultur aussehen? Was – ganz konkret – hindert uns daran, dies zu erreichen? Mit welchen konkreten Maßnahmen erreicht man den kulturellen Wandel? Was trägt jeder im Managementteam konkret dazu bei?
Diesen Workshop wiederholte EFESO mit allen weiteren Mitarbeiter:innen. Dabei teilten einige Mitarbeiter:innen ein ähnliches „Aha-Erlebnis“: Trotz ganz offensichtlicher Fehler hatten sie an einigen Stellen einfach aufgehört, sich selbst zu verbessern und die Verantwortung für Qualität an die Qualitätsprüfung am Ende der Linie delegiert. Im Projekt erlebten sie, dass ein Aufspüren und Benennen von Fehlern nicht nur die Prozesse der Qualitätssicherung verbessert, sondern auch die eigene Arbeit erleichtert. Diese Erkenntnis war der entscheidende Wendepunkt – nun kommt es nur noch darauf an, auch in Zukunft das Gespür und die Motivation der Mitarbeiter:innen für Qualität lebendig zu halten.