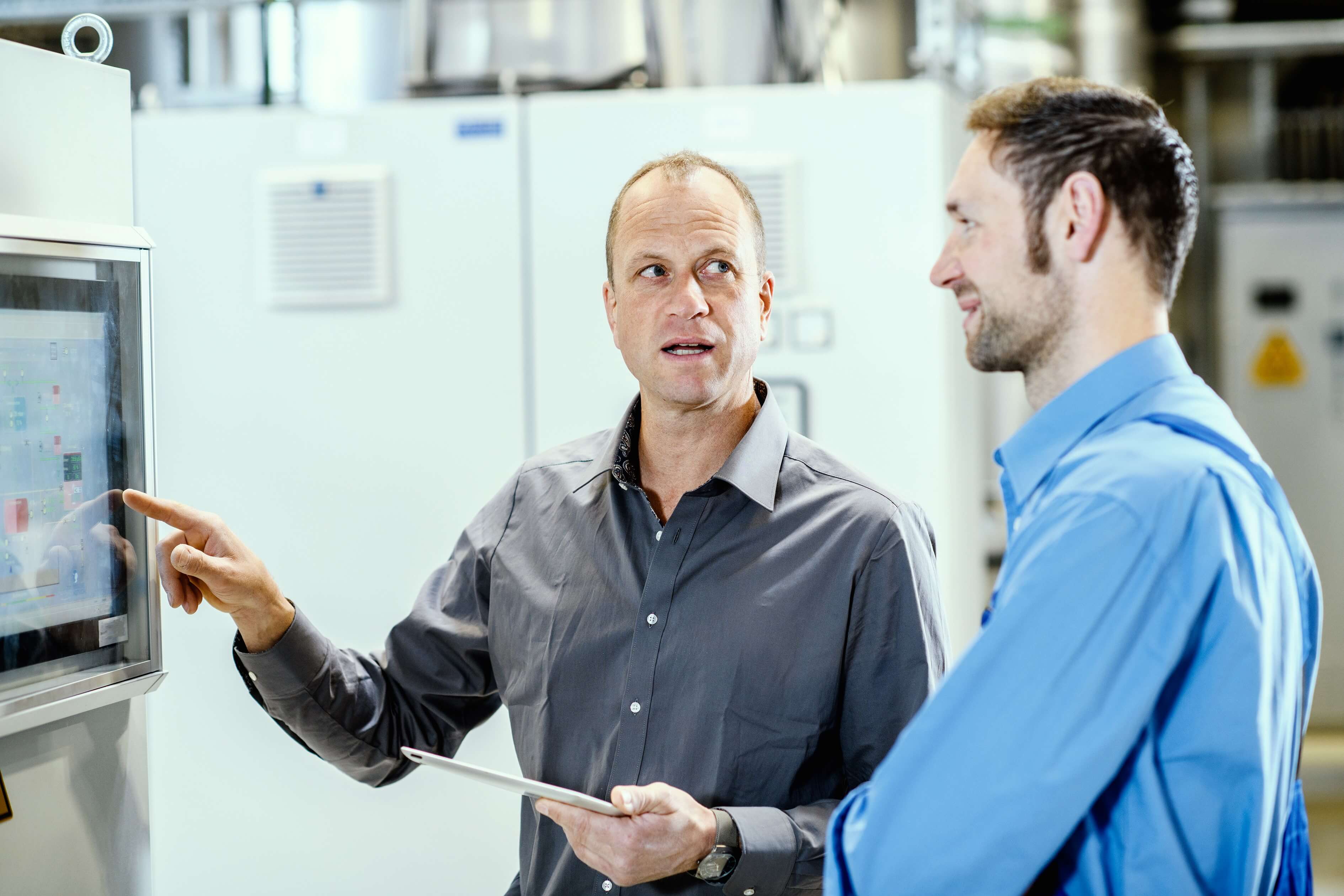
Lean Transformation
Premium-Prozesse statt Fire Fighting
Im Lean Production System eines Automobilherstellers lief ein Premium-Modell mit hoher Variantenspreizung und Fertigungstiefe vom Band. Doch dann gab der neue Produktionsvorstand das Ziel vor, innerhalb von nur fünf Monaten gleich zwei zusätzliche Baureihen auf der selben Linie einzuführen.
Diese schon für sich besonders anspruchsvolle Herausforderung nutzte das Unternehmen für eine Neuausrichtung seiner Produktion, bei der das Volumen der gefertigten Autos um 85% gesteigert und die Produktqualität sowie die schlanke Produktion ein höheres Leistungsniveau erreichen sollten.
Im Teamwork mit EFESO meisterte der Automobilhersteller diese „Lean Transformation“. Er sicherte nicht nur den Anlauf bei der Einführung der neuen Baureihen, sondern erzielte die 85%-Marke mit beeindruckenden Leistungen: neben einem Produktivitätsplus von mehr als 20% und Qualitätsverbesserungen realisierte das Team eine Taktreduzierung von 30% in der Montagelinie.
Herausforderung
Ein Automobilhersteller erweitert die Montagelinie eines Premium-Modells innerhalb von fünf Monaten um zwei Baureihen. Das Volumen der gefertigten Autos soll um 85% steigen, die Produktqualität sowie das Lean Management zugleich ein höheres Leistungsniveau erreichen.
MEHREFESO Lösungsansatz
Das Projektteam entwickelt einen skalierbaren Ansatz zur Lean Transformation des Werkes. Nach Start in einzelnen Pilotbereichen der Montage überträgt es die Verbesserungen in die laufende Linie und schließlich mit weiteren „Lessons Learned“ ins Ramp-up der beiden neuen Modelle.
MEHRLessons Learned
Lean Theorie visualisieren und greifbar machen; Mitarbeiter:innen aus allen relevanten Bereichen frühzeitig einbinden und das Gelernte schnell in der Linie ausprobieren lassen; für ein ein solides methodisches Fundament sorgen, in diesem Fall 3P.
MEHREFESO Erfolgsmodell
Umfassende Lean Transformation in drei Dimensionen: im Technischen (Fertigungs-) System, den Führungsstrukturen sowie in Hinblick auf die Lean Fähigkeiten bzw. „Mindsets“ der Mitarbeiter:innen.
MEHRSkalierbare Lean Transformation als Schlüssel
Nicht für eine, sondern gleich für drei Modelllinien den besten Lean Ansatz zu finden – das ist machbar. Aber was, wenn zwei der Fahrzeugmodelle noch gar nicht gestartet sind und es keinerlei Spielräume gibt, in der laufenden Fertigung die Arbeitsprozesse zu durchleuchten? In genau dieser Ausgangssituation befand sich der OEM einer Premium-Marke. Eine Limousine lief bereits in eingespielten Schritten vom Band, der Ramp-up eines Coupes stand in zwei Wochen bevor – und im nächsten Quartal sollte eine weitere Limousine in der selben Montagelinie starten.
Diese ambitionierte Planung bot allerdings auch die Chance, mit einem neuen Ansatz die Lean Kultur im Werk rasch auf ein neues Leistungsniveau zu bringen. Denn bis dato fanden Produktivitätsverbesserungen nur punktuell statt, häufig im „Fire Fighting“-Modus und ohne eine Strategie, die Lean Kompetenzen langfristig im Team zu verankern und auszubauen. Somit war zu Projektbeginn auch nicht eindeutig klar, wer welche „Verbesserungshebel“ entlang der Prozesskette kennt oder die Verantwortung dafür trägt, diese regelmäßig zu identifizieren.
Gemeinsam mit dem Team der Lean Expert:innen von EFESO entschied sich der Automobilhersteller, einen skalierbaren Ansatz für seine „Lean Transformation“ zu entwickeln. Er startete das Projekt in einzelnen Pilotbereichen der Montage, übertrug die Verbesserungen in die laufende Limousinen-Fertigung und schließlich mit weiteren „Lessons Learned“ ins Ramp-up der beiden neuen Modellreihen. Um die Vorgehensweise auch langfristig in der Organisation zu verankern, definierte das Projektteam Lean Prinzipen für drei Dimensionen: das Technische (Fertigungs-) System, die Führungsstrukturen sowie in Hinblick auf die Lean Fähigkeiten bzw. „Mindsets“ der Mitarbeiter:innen. In diesem Fall bedeutete das zum Beispiel, für bessere Abläufe in der Montagelinie sowie in den Vormontagebereichen die Arbeitsinhalte neu zu verteilen und die Anzahl der Prozesse und Arbeitsstationen zu reduzieren. Auch eine Umstellung der Weitergabe von Informationen am Shopfloor von „manuell“ auf „digital“ sorgte für Zeitersparnisse und eine bessere Kommunikation im Team.
Um 15-25% stieg die Produktivität nach bereits acht Wochen.
Strukturiertes Leuchturmprojekt
Zu Beginn galt es, die richtige Methodik zu finden, um das „Operieren am schlagenden Herzen“ der laufenden Fertigung in der gesetzten Zeit zu meistern. Dies löste das Lean Transformation Team mit einem „Ligthouse Project“ in Pilotbereichen der Montage, welches
- ein strukturiertes, wiederholbares Vorgehen ermöglichte mit einer festen zeitlichen Taktung von zwei Wochen Analyse, zwei Wochen Konzeption, acht Wochen Umsetzung sowie acht Wochen Begleitung (siehe Grafik);
- unter Leitung der Doppelspitze eines EFESO Lean Trainers und eines „Lean Transformers“ aus dem Unternehmen für jeweils 15 bis 35 Mitarbeiter:innen wiederholt werden konnte;
- sich je Bereich auf die KPIs Hours Per Unit (HPU), Defects Per Vehicle (DPV) und Right First Time (RFT) konzentrierte.
Das diese Vorgehensweise funktionierte, zeigte sich bei der laufenden Umsetzung der identifizierten Verbesserungsmaßnahmen. Bereits nach acht Wochen erzielte das Werk eine Produktivitätssteigerung zwischen 15 und 25%. Die Lessons Learned und Erfahrungen aus dieser Phase nutze das Team direkt bei der Einführung der neuen Modelle, ergänzte neue Ideen und Erkenntnisse – und wird dieses Prinzip auch zukünftig auf neue Bereiche „ausrollen“.
Mitarbeiter:innen als Lean Experten aufbauen
Einen wesentlichen Anteil an diesen schnellen Erfolgen hatten die Mitarbeiter:innen, die vom ersten Projekttag an sehr motiviert Verbesserungsvorschläge beisteuerten. Um dieses Wissen aus dem Team zu für die Lean Transformation zu aktivieren, erwiesen sich drei Elemente als besonders wertvoll: erstens, in Videoanalysen Lean Potenziale zu visualisieren und damit greifbar zu machen; zweitens, die Experimentierfreude der Mitarbeiter:innen zu fördern und sie das Gelernte schnell in der Praxis ausprobieren zu lassen. Drittens, mit dem 3P-Ansatz (Production, Preperation, Process) ein solides methodisches Fundament für das Ramp-Up der neuen Modelle in der Linie zu schaffen.
Lean Prinzipin erfahrbar machen
Welche unnötigen Wegstrecken legen Mitarbeiter:innen an ihren Montagestationen zurück? Wo sind Werkzeuge und Fahrzeugteile ungünstig abgelegt? Per Videoanalyse veranschaulichte das Projektteam schnell und nachvollziehbar, wo es Chancen für Zeitersparnisse gibt oder Hilfsmittel zum Einsatz kommen sollten, um Qualitätseinbußen zu minimieren. Zum gelungengen Launch der neuen Modelle trug die Videoanalyse ebenfalls bei, da die Mitarbeiter:innen so neue Arbeitsabläufe proben und verfeinern konnten. Als sehr hilfreich erwies sich auch die Visualisierung der gesamten Lean Transformation im Werk mit einer Projektlandkarte, dem „Control-Room“. Diese zeigte zum einen die wesentlichen Milestones und (Zwischen-) Ergebnisse für das C-Level-Management, zum anderen ließen sich darüber abteilungsübergreifende Fragestellungen thematisieren, eskalieren und vorantreiben.
Experimentierfreude fördern
Viele Mitarbeiter:innen probierten die Theorie der Lean Prinzipien und Methoden direkt in ihrem Arbeitsbereich aus. Das machte das Erlernte nicht nur greifbar, sondern motivierte auch zur Suche nach weiteren Zeitersparnissen. Ein Beispiel: Bei der Sitzmontage in der Limousine verteilten die Mitarbeiter:innen ihre Werkzeuge und kleinere Komponenten im Fußraum und auf den Sitzen. Beim Ramp-up des Coupes hatte das Team bereits ein Montagewagen für Werkzeuge und Teile entwickelt und getestet, das dem Fahrzeug auf dem Förderband folgt und sich schnell in den Innenraum schieben lässt. Damit ist nicht nur das Material in Reichweite und Zeit beim Ein- und Ausräumen eingespart – auch das Risiko einer Beschädigung des Fahrzeugs in diesem Arbeitsschritt sinkt deutlich.
Hot Spots im 3P-Workshop simulieren
In diesem Fall kam hinzu, dass unterschiedliche Fahrzeugmodelle mit einer sehr straffen Zeitplanung in die Montagelinie eingeführt wurden. Viele Abläufe variieren dann, etwa bei der Verkabelung, die in der neuen Limousine umfangreicher und komplexer ist als in den beiden anderen Modellen. Da es sich zudem um die erste Baureihe handelte, war kein Wissen zu Problempunkten vorhanden. Das Projektteam ging daher zweigleisig vor: für die laufende Fertigung der Limousine mit dem klassischen Lean Ansatz. Für das neue Modell identifizierte es mit den Launch-Verantwortlichen im Voraus die „Hot-Spots“: Worin unterscheiden sich die Modelle grundlegend? In welchen Prozessen gibt es mehr Inhalte?
9 statt 14 Minuten benötigt das Team nach einer 3P-Simulation für einen aufwändigen Arbeitsprozess.
Auf einen Blick: Erfolgsfaktoren für Lean Transformation
- Das richtige Team: Führungskräfte, Verantwortliche aus der Linie und Lean Evangelist:innen, die das Thema mit Begeisterung im Team lebendig halten.
- Das richtige Erlebnis: Vorhandene oder geplante Prozesse in einer Testumgebung nach-/aufbauen und wiederholt durchspielen. Informationen und Learnings visualisieren.
- Der richtige Prozess: ist nicht nur auf dem Papier designed, sondern auch im Versuch bestätigt.
Diese Prozesse verbesserte das Projektteam in einem 3P-Workshop zuerst für die Limousine. Dazu baute es neben der Linie ein „Testfeld“ mit einem kompletten Fahrzeug auf und ging für den Abschnitt der Kabelbauminstallationen jeden Prozess fünf- oder sechsmal aufs Neue mit Verbesserungsideen durch. Diese intensive Auseinandersetzung führte dazu, dass die Prozesszeit für diesen Part von 14 auf 9 Minuten sank.
Um +30% verbesserte das Team die Qualitäts-KPI „Right First Time“.
Kompromisslos bei der Qualität
Gerade bei Fahrzeugen der Premium- und Luxusklasse betrachten die Kunden eine hohe Qualität bis in die kleinsten Ausstattungsdetails als Hygienefaktor. Zu Projektbeginn war offen, welche Ansatzpunkte sich in der laufenden Montage der Limousine für Qualitätsverbesserungen am besten eignen könnten. Umso stolzer war das Team auf den Erfolg, ein Plus von 30% bei der fehlerfreien Produktion auf Anhieb (RFT, Right First Time) zu erzielen. Beim Ramp-up des zweiten Modells galt es, dieses Niveau weiter zu halten und zu verbessern.
Der Ansatz von EFESO: zum einen „die Luft aus den Prozessen rauslassen“, d.h. die Taktzeit zu reduzieren und zugleich weitere Tätigkeiten zum Arbeitsprozess hinzuzufügen. Zum anderen die Qualitätskennzahlen zu „Right First Time“ und „Defects Per Vehicle“ frühzeitig erheben und für jede:n Mitarbeiter:in klar am Shopfloor kommunizieren. Unterstützt wurde das erneut durch die hohe Motivation im Team, aktiv Ideen beizutragen. Beispielsweise holten Mitarbieter:innen Komponenten des Kofferaums erst im Fahrzeug aus ihrer Verpackung und montierten sie dann von der Innenseite des Kofferraums aus, was regelmäßig zu kleinen Beschädigungen führte. Mit einem Werkzeugwagen, der dem Fahrzeug nun auf dem Band mit bereits ausgepackten Teilen folgt, ist dieses Qualitätsrisiko ausgeschaltet.
Produktivitätsziele übererfüllt
Mit diesen und vielen weiteren Verbesserungsmaßnahmen erzielte das Lean Transformation Projekt außerordentliche Ergebnisse. Das Werk konnte nach erfolgreichem Ramp-up der neuen Modelle sein Produktionsvolumen um 85% steigern und erzielte dabei ein Produktivitätsplus von insgesamt 20%. Und damit sind noch nicht alle Lean Potenziale erschlossen. Denn neben den getakteten Linien gibt es weitere Bereiche, die nach Prinzip der Werkstatt- bzw. Inselfertigung Komponenten wie Leder bearbeiten und zuliefern. Für die engagierten Mitarbeiter:innen im Unternehmen ein ideales Terrain, um neue, schlanke „Premium“-Prozesse zu entwickeln.
Um 20% stieg die Produktivität im Werk innerhalb von fünf Monaten.