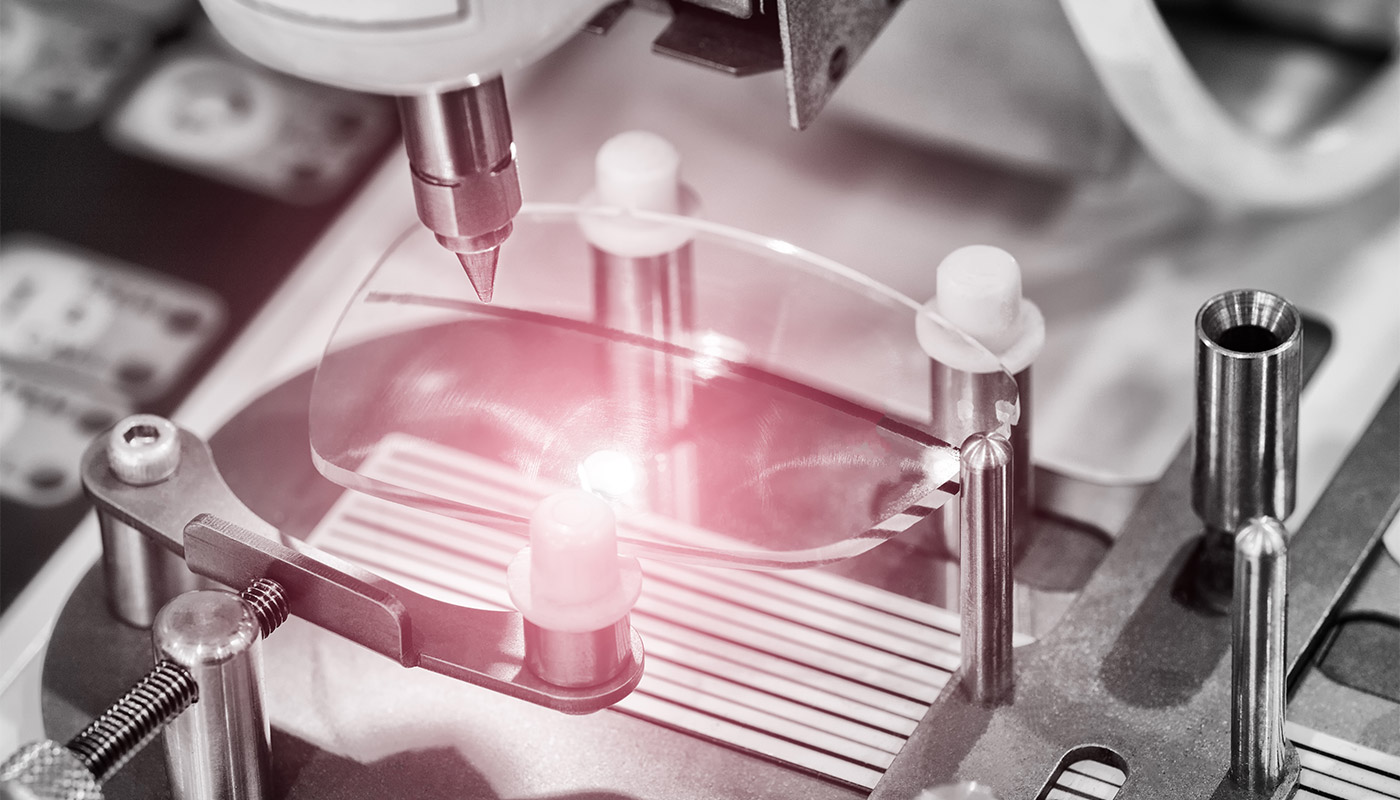
Komplexität reduziert, Wachstum gesteigert
Der Brillenhersteller Thélios synchronisiert seine Wertschöpfungskette und reduziert seinen WIP um 35 Prozent.
Die italienische Unternehmensgruppe Marcolin S.p.A. designt, fertigt und vertreibt seit 60 Jahren Sonnenbrillen und optische Gläser für renommierte Marken wie Tom Ford, Bally, Moncler, Sportmax oder Ermenegildo Zegna. Im Jahr 2018 verkaufte sie mehr als 14 Millionen Brillen über 150 Vertriebspartner in 125 Ländern. Die Kunden stellen hohe Erwartungen an das Design, die Qualität und Verfügbarkeit der Produkte – entsprechend wichtig ist ein optimales Management der internationalen Lieferketten und Produktionsprozesse des Fashion-Unternehmens.
Herausforderung
Ein Hersteller von Luxus-Brillen gründet einen neuen Produktionsstandort. EFESO soll den erfolgreichen Start des neuen Werkes und die optimale Gestaltung der Wertschöpfungsketten sicherstellen.
MEHREFESO Lösungsansatz
Einführung eines schlanken Entwicklungssystems, eines Lean-Design-Ansatzes zur Rationalisierung der Produktpalette sowie eines Kapazitätsmodells zum Ausgleich der Arbeitsbelastung.
MEHRLessons Learned
Das Commitment der Mitarbeiter:innen ist ein zentraler Erfolgsfaktor – ebenso wie ein flexibles Produktionstool, das eine ganzheitliche Produktüberwachung gewährleistet.
MEHREFESO Erfolgsmodell
Mit Lean Management Methoden setzt das Projektteam ein Konzept dynamischer Montagelinien in der Praxis um. Es entsteht eine „schlank“ organisierte Fabrik, die eine exzellente Lieferzeit und ein minimales Betriebskapital aufweist.
MEHRNeuer Fertigungsstandort für Luxus-Brillen
2017 vereinte das Unternehmen Thélios als Joint Venture das Know-how von Marcolin und des französischen Konzerns LVMH in der Brillenfertigung. In diesem Kontext wurde die Manifattura Thélios in Longarone, Italien, gegründet, einer Stadt, die für ihre Expertise in der Brillenherstellung bekannt ist. Dieser neue Standort fertigt Brillen für die Filialen der LVMH-Gruppe. Für einen erfolgreichen Start des neuen Werkes und die optimale Gestaltung der Wertschöpfungsketten engagierte Thélios das Team von EFESO.
Mit drei Expert:innen für Produktion und Logistik analysierte EFESO die Ausgangsituation in zwei Monaten. Dank früherer gemeinsamer Projekte mit Marcolin, Luxottica und ihrer guten Reputation in Frankreich konnten die Berater:innen schnell ermitteln, welche Verbesserungen sich erzielen ließen.
In zwei Monaten sorgte das Projektteam für ideale Startbedingen eines neuen Werkes.
Lösungsansatz von EFESO: Synchronisierung der Wertschöpfungskette
Der Projektfokus lag in diesem Fall auf der Entwicklung von Prozessen, Fertigungsbereichen und Schlüssellieferanten. Zusammen mit dem gesamten technischen Team implementierte EFESO …
- ein schlankes Entwicklungssystem, um die Entwicklungszeit zu verkürzen, Probleme bei der zeitgleichen Entwicklung von Kollektionen zu antizipieren und Wissen zu kapitalisieren;
- einen Lean-Design-Ansatz zur Rationalisierung der Produktpalette, indem unnötige Komplexität reduziert wird und somit das Risiko, mit veralteten Informationen zu arbeiten;
- ein Kapazitätsmodell zum Ausgleich der Arbeitsbelastung für Prototyping, Entwicklung und Industrialisierung.
Ein Lean-Design-Ansatz strafft die Produktpalette.
Erfolgsmodell EFESO
Aus der Verbindung von Spitzentechnologien mit einzigartigem Know-how schuf Thélios ein komplettes und flexibles Produktionstool, das eine ganzheitliche Produktüberwachung gewährleistet – von der ersten kreativen Kollektionsplanung über die Herstellung bis schließlich zum Endkunden am Point of Sale.
Um 35 Prozent sank die Vorlaufzeit der Fertigung.
Gemeinsam mit dem zukünftigen Operations-Team setzte EFESO die Projektziele erfolgreich um. Ein zunächst mit Pappe simuliertes Konzept dynamischer Montagelinien erwies sich dabei als ideal geeignet für die Umsetzung in der Praxis. So entstand eine „schlank“ organisierte Fabrik, die eine exzellente Lieferzeit und ein minimales Betriebskapital aufweist.
Die Interaktion und erfolgreiche Einbindung der Mitarbeiter:innen am Standort spielte dabei stets eine wesentliche Rolle. Denn die Übernahme von Lean-Konzepten durchbricht die traditionellen Produktionsparadigmen – was ein Commitment des Teams erfordert, die damit verbundenen Anstrengungen bei der Umsetzung zu meistern.
WIP und Vorlaufzeit der Fertigung erheblich reduziert
Die Vorgehensweise erbrachte eindeutige Resultate für ein erfolgreich abgeschlossenes Projekt:
- Bessere Regalverfügbarkeit und schnellerer Nachschub aufgrund einer reduzierten Reaktionszeit.
- Reduktion des WIP in der Produktion: -35 bis -50 Prozent.
- Reduktion der Vorlaufzeit der Produktion: -35 Prozent.
- Reduktion der Überschneidungen in der Lieferkette: -30%.
- Erhöhung der Wertschöpfung in der Entwicklung durch schnelleres Prototyping und Know-how-Austausch.
- Weitere Verlustreduzierung in der technischen Abteilung (Prozess-BPR und Digitalisierung).
- Nivellierung der Arbeitsbelastung durch Festlegung der Kadenz von Markteinführungen.
- Synergie mit der Konstruktion, frühzeitiges Management von kritischen Problemen und gemeinsame Nutzung von Mitarbeitern für das Prototyping.
Um 30 Prozent wurden die Überschneidungen in der Lieferkette reduziert.