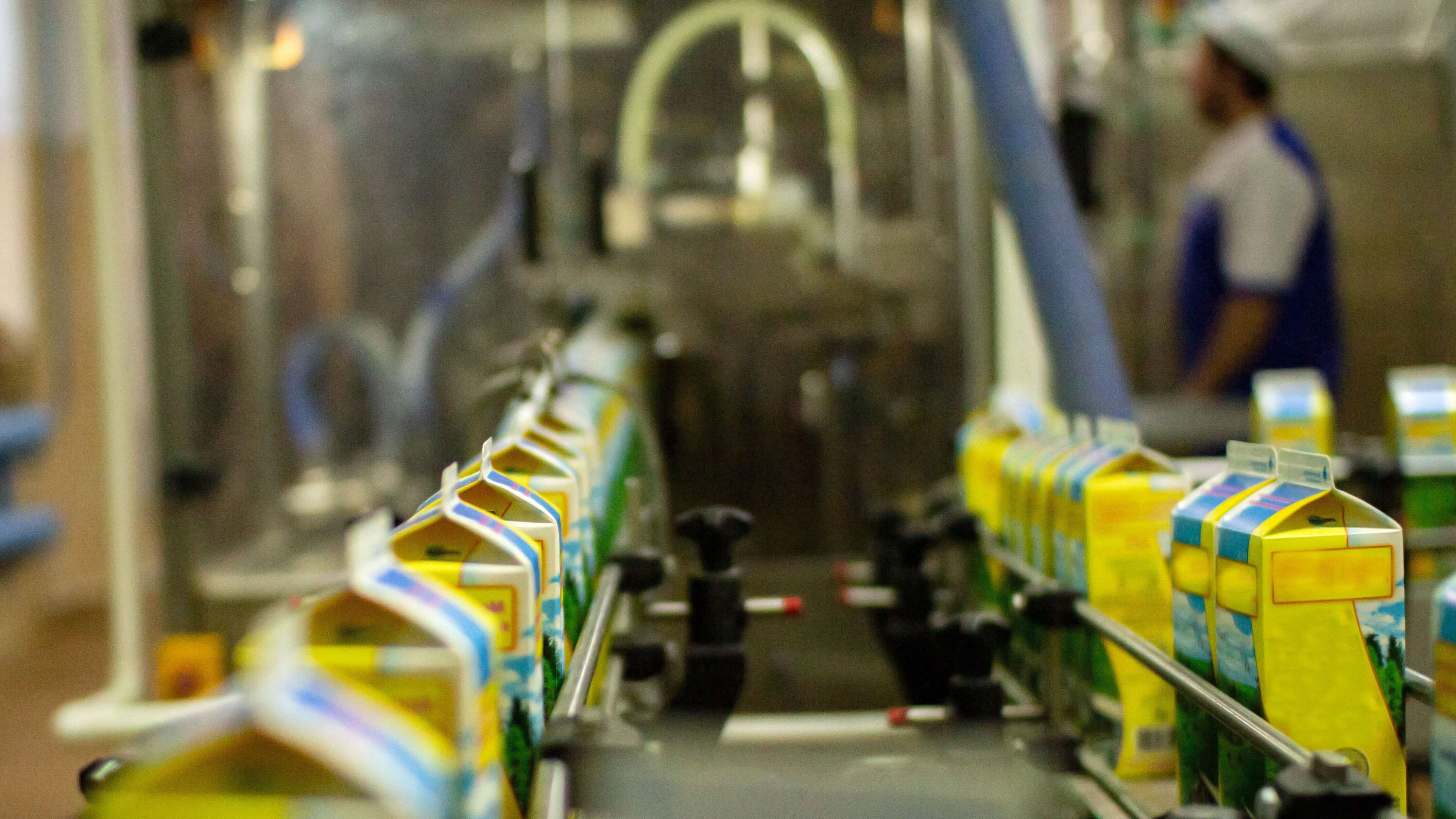
Bei Umsatz und Nachhaltigkeit auf Kurs
Konsequente Umsetzung der Zero-Loss-Philosophie mit WCOM™ bei einem Marktführer in der Verpackungsindustrie
Einer der weltweit größten Verpackungskonzerne will Reklamationen, Abfall, Produktivitätsverluste und Verarbeitungskosten an seinen Produktionsstandorten weiter reduzieren. Um die Ziele zu erreichen, führte das Unternehmem mit EFESO ein umfassendes WCOM™-Programm in 24 Werken rund um die Welt ein und schulte seine Mitarbeiter entsprechend.
Über einen Zeitraum von acht Jahren hat das Unternehmen seine Betriebsabläufe mit EFESO weiterentwickelt. Es erzielte außergewöhnliche Ergebnisse bei der Beseitigung und Verhinderung von Verlusten - und qualifizierte Tausende Mitarbeiter für die Realisierung kontinuierlicher Verbesserung.
Herausforderung
Ein globaler Marktführer der Verpackungsmittelindustrie stärkt seine Wettbewerbsfähigkeit gegenüber neuen Marktakteuren. Dabei richtet sich der Konzern im Sinne der „Zero-loss“-Philosophie auf ein ökonomisch und ökolgisch profitables Wirtschaften hin aus.
MEHREFESO Lösungsansatz
Das Unternehmen verfolgte den WCOM™-Ansatz von EFESO, um in 24 Werken die Erkennung, Beiseitigung und Vermeidung von Verlusten zu verbessern. Zugleich befähigte es tausende Mitarbeiter, Operational Excellence (OPEX) zu verfolgen und zu verwirklichen.
MEHRLessons Learned
Die Operationalisierung der strategischen Ziele benötigt klare Prozesse und ein genaues Verständnis davon, wo die größten Potenziale für Zero-loss liegen. Dabei stellt die Mitarbeiterqualifzierung eine unverzichtbare, tragende „Säule“ für WCOM™ / OPEX-Projekte dar.
MEHREFESO Erfolgsmodell
Teamleiter und weitere Mitarbeiter aus den Werken arbeiten mit Methodikexperten von EFESO in Verbesserungsteams zusammen, um Methodik- und Praxisexpertise von Anfang an optimal zu kombinieren. Dabei werden die Werksteams zur eigenständigen Weiterentwicklung befähigt.
MEHRNeuausrichtung der Fertigung und weiterer Operations-Bereiche
Das in den 1950er Jahren gegründete und seit vielen Jahren als Familienunternehmen geführte Unternehmen hat sich zum Marktführer bei Getränkekartonverpackungen entwickelt. Mit seinen Verpackungsdesigns setzt es Branchenstandards - und erzielt heut mit fast 200 Milliarden verkauften Verpackungseinheiten einen zweistelligen Milliardenumsatz pro Jahr.
Die Zusammenarbeit mit EFESO startete vor einigen Jahren und trug maßgeblich zu dieser Erfolgsgeschichte bei. Bereits mit innovativen Produkten sehr gut im Markt aufgestellt, richtete die damalige Geschäftsführung das Unternehmen darauf aus, die Produktion und das Betriebsmanagement in allen Standorten auf ein erstklassiges Leistungsniveau zu bringen – und dies im Sinne einer kontinuierlichen Verbesserung dann weiter fortzusetzen. Dies sollte die Wettbewerbsfähigkeit gegenüber neuen Akteuren im Markt stärken; zugleich legte die Eigentümerfamilie viel Wert darauf, verantwortungsbewusst zu wirtschaften und eine „Win-Win-Win-Situation“ zu schaffen, in der das Unternehmen, seine Kunden und der Planet profitieren.
Weltklasseniveau bei „Zero-loss“ im Fokus
Mit einer klaren Zielsetzung richtete das Unternehmen dieses Vorhaben von Anfang an eindeutig aus: im Unternehmen sollte die Philosophie des Null-Verlustes (Zero-loss) verwirklicht werden. Eine Auszeichnung mit dem Industriepreis „TPM Award“ des Japan Institute of Plant Maintenance (JIPM) sollte dann im Laufe der Zeit von externer Seite prüfen und bestätigen, dass man sich mit klaren Verbesserungen auf dem richtigen Weg befindet. Dazu ermutigte das Management alle Operations-Bereiche, sich zu beteiligen und gemeinsam ein Weltklasseniveau bei „Zero-loss“ zu erreichen.
Diesen Weg wollte der Verpackungshersteller gemeinsam mit EFESO beschreiten. Schließlich hatte die Unternehmensberatung bereits in vergleichbaren Projekten bewiesen, dass ihr WCOM™-Ansatz die angestrebten Ergebnisse erbringt. Im Laufe der Zeit qualifizierte das Unternehmen tausende Mitarbeiter über WCOM™-Teams dazu, Ansatzpunkte für kontinuierliche Verbesserungen in den täglichen Arbeitsabläufen zu entdecken und zu verwirklichen. WCOM™ etablierte sich somit als elementarer Bestandteil der Organisationskultur und wird bis heute vom Unternehme weltweit erfolgreich weiterentwickelt.
Der TPM Award soll als „Proof of concept“ für die erzielten Ergebnisse dienen.
Kombination von Zero-loss und OPEX (Operational Excellence)
Das Projektteam setzte sich aus WCOM™-Verantwortlichen und EFESO Consultants zusammen. Um die Projektziele in den damals 24 weltweiten Standorten zu erreichen, verfolgte es den von EFESO entwickelten WCOM™-Ansatz (World Class Operations Management) für Fabriken. Dieser konzentriert sich auf:
- Zero-loss-Prinzip: Der Ansatz basiert auf dem Null-Verlust-Prinzip (zero-loss) und umfasst die Dimensionen Verlusterkennung, Verlustbeseitigung und Verlustvermeidung. Das Projekt startete an allen Standorten mit einer Verlustanalyse, die schnell die problematischsten Punkten in den Fertigungslinien ans Licht brachte. In einem Masterplan wurden diese Punkte zusammengefasst, priorisiert und mit Maßnahmen zur Reduzierung oder kompletten Vermeidung der Verluste versehen.
- Befähigung zu OPEX: Gleichzeitig baute das Projektteam Schritt für Schritt und in Zusammenarbeit mit allen wichtigen operativen Ebenen ein entsprechendes OPEX-System auf. Dies beschränkte sich nicht auf eine technologiegestützte Weiterentwicklung der Prozesse und IT / OT-Systeme. Ebenso wichtig war die Befähigung der Mitarbeiter, diese Prozesse und Systeme im Alltag zu nutzen. Diese konnten somit ihre eigenen Abläufe stabilisieren, Verluste reduzieren und langfristig eine ständige Verbesserung eigenständig voranttreiben.
Der Konzern steigerte mit WCOM™ die Produktivität in 24 Werken um 30% - und halbierte deren Abfallmenge.
Cross-funktionale Verbesserungsteams
Eine Besonderheit des Ansatzes: Lösungen, um zu „Zero-loss“ zu gelangen, entstehen in zwei Ebenen. Zum einen direkt vor Ort in den Teams an der Maschine / Anlage. Diese Teams werden meist von den Bedienern geleitet – schließlich geht es um ihre Arbeitsumgebung und darum, wie sie ihre Arbeit einfacher, stabiler und effizienter gestalten können. Diese Perspektive wird – zum anderen – von „Verbesserungsteams“ erweitert, die sich aus Vertretern mehrerer Bereiche wie Betrieb, Wartung, Beschaffung oder HR zusammensetzen.
Ein großer Vorteil dieser Vorgehensweise besteht darin, mit gemeinsam erzielten Ergebnissen den Teamgeist innerhalb der gesamten Unternehmenskultur zu stärken. Zudem wird das abstrakte Thema „ständige Verbesserung“ nicht nur an den Maschinen, sondern an vielen weiteren Punkten der Organsiation mit Erfolgsgeschichten „lebendig“. Im diesem Fallbeispiel konnten die Verbesserungsteams innerhalb von drei Monaten deutliche Resultate auf dem Weg zu „zero-loss“ verbuchen. Über die gesamte Projektdauer hinweg und über die Werke insgesamt betrachtet erzielte das Unternehmen u.a. diese Ergebnisse:
- 50 % weniger Reklamationen
- Abfall um 50 % reduziert
- Produktivität um 30 % gesteigert
- Umrüstungskosten um 37 % gesenkt
Zudem übertraf es sein ursprüngliche Mindestziel bei weitem: nicht nur eine, sondern mehrere TPM-Awards für den gesamten Werkverbund (geprüft und vergeben von JIPM) bestätigten die Ergebnisse und wegweisenden Arbeitsprozesse auf allen Ebenen der Fertigung, Wartung, Qualität und Kompetenzentwicklung der Belegschaft. Das Unternehmen profitiert davon bis heute, u.a. in diesen Bereichen:
- Die Auswirkungen des Programms verbesserten die Produktivität so sehr, dass sich die Marktpositionierung vom „Verteidiger von Marktanteilen“ zum aktiven Marktführer wandelte.
- Die bessere Auslastung der Kapazitäten führte zu Einsparungen im Mio.-Bereich bei Investitionsgütern und zur Erhöhung von Marktanteilen.
- Das Programm wurde vollständig digitalisiert und zudem auf Lieferanten und Kunden ausgeweitet, um die Leistung der gesamten Wertschöpfungskette zu verbessern.
Die Verbesserungsteams sind bis heute der entscheidende „Treiber“ zur Realisierung kontinuierlicher Verbesserung im Konzern. Ihr Erfolg beruhte in hier u.a. auf der Umsetzung dieser Leitlinien:
Den Teamgeist fördern – und fordern.
Ein Standort entwickelte ein Vorgehen zur „horizontalen Expansion“ von Verlustbeseitigung von einer auf weitere Linien. Dieses Vorgehen ließ sich leider nicht in alle anderen Werke übertragen. Dennoch motivierte dieser Erfolg das zuständige Team sehr, den eingeschlagenen Weg täglich weiter zu verfolgen – und mit jedem behobenen Verlust den Arbeits-(Prozess) stabiler zu machen. Wer dies wenige Male erlebt, ist motiviert, sich erneut in Verbesserungsteams aktiv einzubringen.
Mit einfachen, effizienten Lösungen experimentieren.
In einem anderen Werk identifizierte das Team Verluste an den Druckmaschinen, die den Verpackungen ihr Erscheinungsbild geben. Um die Zeit für die Maschinenreinigung zu reduzieren, entwickelten die Mitarbeiter clevere Lösungen, etwa zur Neubefüllung der Maschine mit Farben oder zur Vermeidung von Papierverschwendung bei Druckdüsentests. Dieses „Tüfteln“ an eigenen Lösungen erweist sich auch in anderen WCOM-Projekten als ergiebig, da die direkt in den Arbeitsschritt involvierten Mitarbeiter einen pragmatischen Blick auf derartige Schwachstellen haben – und meist sehr gute Idee, um sie zu beheben. Die Kosten dafür sind i.d.R. sehr gering, die Änderungen machen aber einen großen Unterschied in der täglichen Arbeit und summieren sich natürlich auf dem Weg zum Zero-loss-Ziel.
Prozesse visualisieren.
Ein weiteres Beispiel, dass sich leicht auf alle Werke übertragen ließ, sind die visualisierten Prüfpunkte in der Fertigung. Schematische Fußabdrücke auf dem Hallenboden zeigen in unterschiedlichen Farben die Wege und Stationen für Inspektionen an, z.B. Blau für „Qualität“ und Rot für „Sicherheit“. Dies verkürzt Inspektionszeiten und gestaltet diese effizienter, ohne dass die Qualität der Inspektion nachlässt. Ein Werk in Italien entwickelte diesen Ansatz zu einem digitalen Poka-System weiter. Kleinerere Abweichungen, die bei der Inspektion oder während der Arbeit entdeckt wurden, ließen sich somit direkt Poka-System eingegeben und dort mit Maßnahmen zur Beseitigung der Verluste weiterverfolgen.
Natürlich ist das nur ein sehr kleiner Ausschnitt der zahlreichen Ideen und Maßnahmen, die im Laufe der Zeit umgesetzt wurden. Den immensen Wert, der damit generiert wurde und wird, verdeutlicht die Anzahl der Mitarbeiter in den Verbesserungsteams: während der Zusammenarbeit mit EFESO qualifizierte der Verpackungshersteller tausende Angestellte zu den Themen WCOM™ / OPEX.
Von der Strategie in die Praxis
In diesem Projekt erwiesen sich u.a. die folgenden Aspekte als besonders wichtig, um die vom Unternehmen gesetzten Ziele zu erreichen:
Verankere strategische Ziele im Tagesgeschäft!
Eine der größten Herausforderungen im Projekt bestand darin, die übergeordneten Ziele aus dem „Big Picture“ der Strategie auf die Ebene der konkreten Aktivitäten im Shopfloor / der Linie hinunterzubrechen. Ein wichtiger Erfahrungswert war hier, dass nicht nur das tägliche Management hier ein Ansatzpunkt sein muss, z.B. in Schicht-Reviews oder Regel-Meetings. Ebenso wichtig ist es, die „Lücken“ konsequent in einem Ergebnisplan festzuhalten: Welche Bereiche bergen Potenzial, um Verluste zu vermeiden – sind aber noch nicht in Angriff genommen?
Der Verpackungshersteller erreichte eine Prozesskontrolle in seinen Werken. Er konnte somit klar die „Pain Points“ der Verluste benennen und die Ressourcen realistisch benennen, die zur Schließung dieser Lücken erforderlich sind. Dies erwies sich als konkrete Verbindung, als der „rote Faden“ für das Management, um zu verstehen, was man braucht, um das strategische Ziel zu erreichen – und was zugleich den Teams vermittelt werden muss, um diese zu führen und zu motivieren.
Mache Bildung zum Erfolgsgaranten!
Als tragende „Säule“ des WCOM™ / OPEX-Projektes erwies sich hier die Qualifizierung bzw. Befähigung der Belegschaft, das Erlernte auch eigenständig weiterzuverfolgen. Dies gelang über eine Trainings- / Qualifizierungsansatz nach dem Train-the-Trainer-Konzept. Anhand des gewonnenen Wissens wurden zudem eine interne Akademie sowie eine interne Beratung eingerichtet. Somit kennt das Unternehmen ganz genau die Prozesse, Standards und Niveaus der Qualifizierung in der Organisation, kann also auch in diesem Bereich seine Ressourcen gezielten und ergiebig einsetzen.
Betone die hohe Bedeutung des Themas!
Bereits in den ersten Tagen und Wochen des Projektes signalisierte die Führungsspitze des Konzerns den Mitarbeitern klar, welchen hohen Stellenwert WCOM™ / OPEX von nun an haben. Die C-Level-Entscheider engagierten sich z.B. in Audits, die Verbesserungsteams durchführten. Sie besuchten regelmäßig Werke, um sich über Best Practices und Ideen zu informieren und auszutauschen – nicht nur mit dem Management, sondern auch mit Mitarbeitern in den Linien. Dieses Engagement trug entscheidend dazu bei, dass Projekt mit viel „Passion“ zu starten und auf Erfolgskurs zu bringen.
Methodik- und Praxisexpertise werden vom Projektbeginn an kombiniert.
Befähigung im „Tandem“ mit WCOM™-Experten
Beratungsprojekte zu Effizienz und Verlustreduzierung sind häufig einseitig geprägt: die externen Berater werden engagiert, um eine Verlustanalyse vorzunehmen und schließlich die Umsetzung der Verbesserungen zu steuern. Als Outcome entstehen vor allem Ergebnisdokumentationen. WCOM™ / OPEX Projekte mit EFESO sind u.a. deswegen erfolgreich, weil sie diese Systematik aufbrechen und erweitern. So sollen z.B. die Mitarbeiter des Unternehmens die Verlustanalyse bestätigen. Das erfordert einen direkten, intensiven Austausch mit allen Akteuren wie Anlagenführern, Monteuren, Wartungsmitarbeiter. Von Anfang sensibilisiert dies die Mitarbeiter für das Thema – nicht in der Theorie, sondern an ihrem Arbeitsplatz.
Diese Vorgehensweise bringt zudem „Pain Points“, also heikle Themen ans Licht. Diese sind häufig bekannt, werden aber nicht kommuniziert oder konsequent nachverfolgt – und tauchen in Verlustanalysen nicht auf. Auch in diesem Projekt identifizierte das Unternehmen bereits in der Anfangsphase solche „Pain Points“ und entwickelte Lösungen dazu. Die Struktur zur Umsetzung schufen die bereits genannten Verbesserungsteams mit einer in zahlreichen WCOM™ / OPEX Projekten bewährten Teamkonstellation: Mit den Methodikexperten von EFESO bilden Teamleiter und Mitarbeiter aus den Werken Verbesserungsteams, z.B. für Produktion, Wartung, Logistik. Somit werden Methodik- und Praxisexpertise von Anfang an kombiniert.
Consultants mit regionaler Erfahrung
In dieser Art der Zusammenarbeit erweist es sich immer wieder als Erfolgsmodell, die Verbesserungsteams zu einer eigenständigen, vom Berater unabhängigen Weiterentwicklung zu befähigen. Dessen Rolle verändert sich nach dem Bedarf und dem Reifegrad des Programms in der Organisation. Wie bei einer Fahrt im Tandem ist der Berater anfangs z.B. eher als steuernder Prozessexperte gefordert, kann aber vielleicht schon nach kurzer Zeit dem Teamleiter diese Rolle übergeben. In diesem Fall wechselt der Berater in die Rolle des Coachs oder Auditors, der bedarfsweise wieder zum Verbesserungsteam hinzustößt.
In diesem Fallbeispiel erwies sich auch die globale Präsenz von EFESO als Schlüssel zum Erfolg: es gelang dem Verpackungshersteller, WCOM™ / OPEX trotz der unterschiedlichen Sprachen und (Führungs-)Kulturen parallel in den Werken zu etablieren. Dies funktioniert in dieser Form nur mit einem Team aus Beratern, die einen engen regionalen Bezug haben und die standorteigenen Herausforderungen genau kennen. Die Erfolgsgeschichte wird auch heute weiter fortgesetzt: nach vielen Jahren dient das System inzwischen sogar Operations Management System für das Unternehmen.