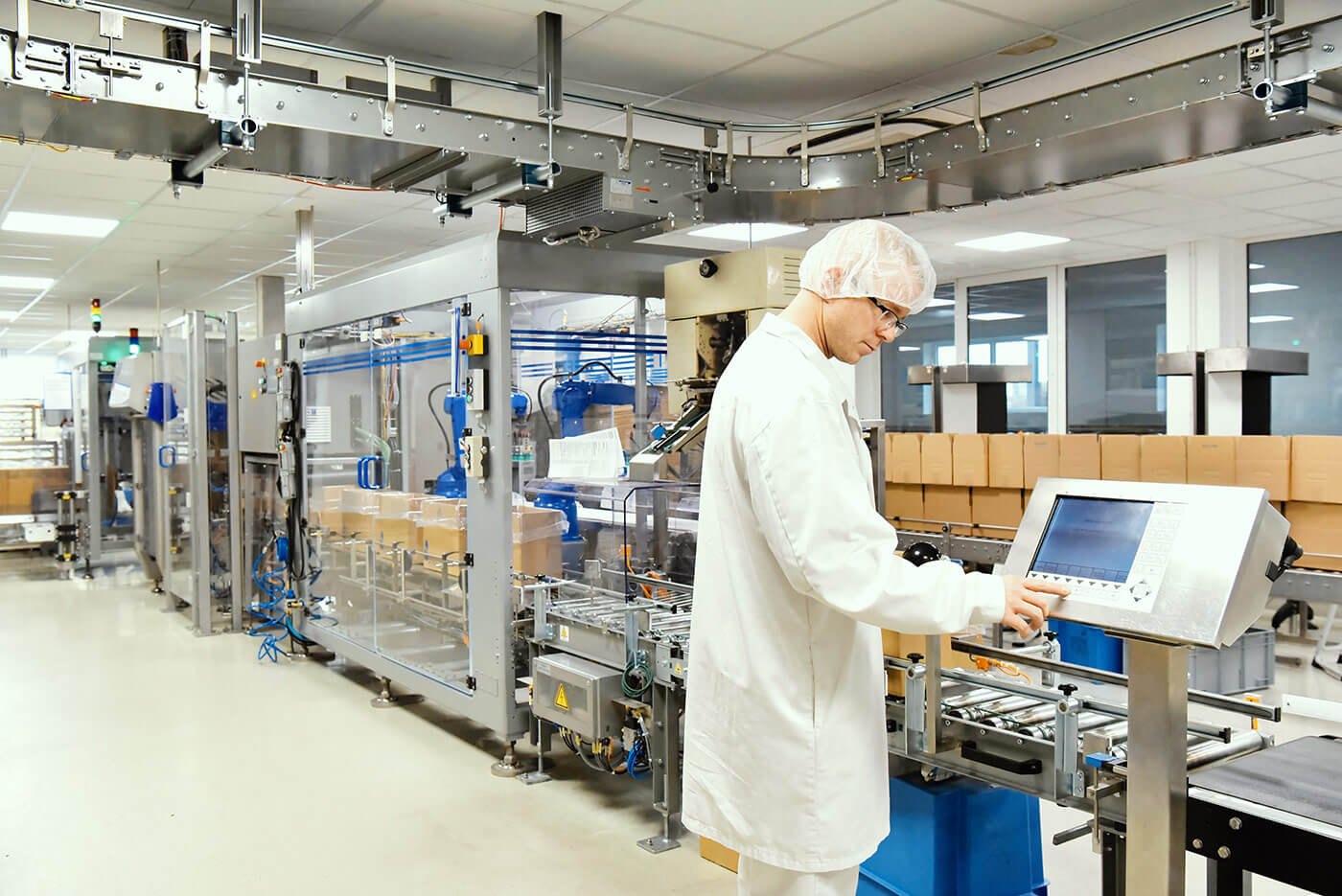
Smart Factory Planning
Smarte Planung für smarte Fabriken
Wie sieht die ideale Fabrik der Zukunft aus? Steuern dort Produkte ihre Fertigung komplett selbstständig? Oder geht es eher um die perfekte Choreographie von Menschen und Maschinen? Häufig verlieren sich Unternehmen bei der Planung einer „Smart Factory“ in unterschiedlichen Vorstellungen, welche Technologien oder Organisationsformen den bestmöglichen Weg in die Zukunft darstellen. Ein „Big Picture“ davon, wohin die Reise gehen soll und wie die Umsetzung konkret funktionieren kann, ist selten vorhanden.
In diesem Fall entwickelt ein Unternehmen aus dem Pharma- & Lifesciences-Sektor gleich vier seiner Werke in Europa zu „Smart Factories“ weiter. Gemeinsam mit EFESO schuf es zuerst dazu ein solches Gesamtbild als Planungsgrundlage für die anstehenden Transformationsprozesse in den Standorten – und testete daraufhin passende Technologien in Pilotprojekten.
Herausforderung
In nur vier Wochen möchte ein Pharma- & Lifesciences-Unternehmen die zentralen Stoßrichtungen für die Smart Factory Transformation von vier Werken planen.
MEHREFESO Lösungsansatz
Das Projektteam entwickelt ein „Big Picture“ als Planungsgrundlage für die anstehenden Transformationsprozesse und testet drei priorisierte Technologien in Pilotprojekten.
MEHRLessons Learned
Commitment aller Entscheidungsebenen frühzeitig einholen; Ideen aus der Linie berücksichtigen, aber die Umsetzung nach Notwendigkeit priorisieren.
MEHREFESO Erfolgsmodell
Bereits in der Planungsphase wenige Kernthemen heraussfiltern, die schnell realisierbar sind, in der Umsetzung wenig kosten und zugleich einen großen Benefit bringen.
MEHREFESO Scan ermittelt Smart Factory Potenziale
Die besondere Herausforderung lag bei diesem Projekt darin, dass sehr unterschiedliche Produktruppen und Linien in einem Zeitraum von je maximal vier Wochen eingebunden werden sollten. Die Arbeitsabläufe und Performance-Indikatoren variierten je Linie und Werk, mit entsprechend unterschiedlichen Bedarfen und Prioritäten bei der Digitalisierung. Ergo ging es beim Projektstart darum, erst einmal ein klares Bild zum Status Quo des Reifegrades und den Anforderungen je Standort zu erhalten. Genau dies ermittelte EFESO mit seinem Smart Factory Scan in nur vier Wochen.
Bei dem Scan handelt es sich um ein Assessment-Tool, das alle zeitlich und inhaltlich relevanten Faktoren für die Digitalisierung von Fertigungsstandorten sammelt und strukturiert. Ein Projektteam aus Mitarbeiter:innen der Standorte und EFESO Berater:innen staffelte dies in den folgenden Abschnitten:
4 Werke in 4 Wochen überprüfte der EFESO Smart Factory Scan auf optimale Ansatzpunkte zur Digitalisierung.
Erste Woche: Status Quo erfassen
Zuerst ging es ausschließlich um eine Bestandsaufnahme: Was ist bereits in den Werken digitalisiert? Welche laufenden Projekte existieren? Gibt es Besonderheiten und spezielle Anforderungen, die zu berücksichtigen sind? Gute Ansätze wurden festgehalten, um sie später im Kontext aller Maßnahmen und Projekte in den Werken zu bewerten. Ein zentraler Bestandteil dieses ersten Schrittes war zudem, die wichtigsten Grunddaten im Sinne eines Baselinings zu erheben.
Zweite Woche: Big Picture mit Stoßrichtungen skizzieren
Auf Grundlage dieser Erkenntnisse legte das Projektteam in einem gemeinsamen Workshop mit der Werksleitung die Hauptstoßrichtungen pro Standort fest. Im Fokus standen nicht nur Themen, die der Führungskreis als besonders spannend und interessant erachtete, sondern auch Entwicklungsszenarien sowie die Standortstrategien. Daraus ergab sich ein Big Picture, das ein gemeinsames Verständnis der Workshopteilnehmer:innen dazu absicherte, wohin die Reise gehen soll. Entsprechend hoch war das Commitment für die gemeinsamen nächsten Schritte.
Im Workshop legten die Teilnehmer:innen außerdem die unterschiedlichen Digitialisierungs-Stoßrichtungen der jeweiligen Standorte fest. Dazu zählten Themen wie Datentransprenz, Smart Analytics oder Digitaler Zwilling für den Herstellungsprozess, smarter Materialfluss sowie fahrerlose Transportsysteme (FTS). Da das Unternehmen von einigen Pharmaprodukten pro Jahr Stückzahlen im dreistelligen Millionenbereich produziert, bewegt es große Materialmengen über unterschiedliche Prozessschritte – entsprechend aufwendig und kostspielig sind die dazu notwendigen Abläufe. So sollen zum Beispiel die FTS dazu beitragen, den zukünftigen Materialfluss kostengünstiger und transparenter zu gestalten.
Dritte und vierte Woche: Deep Dives klären Details
In dieser Phase beschäftigte sich das Projektteam mit sogenannten „Deep Dives“, d.h. den technologischen und ökonomischen Details der festgelegten Stoßrichtungen. So identifizierte es etwa die potentialträchtigsten Bereiche für fahrerlose Transportsysteme, in welcher Größenordnung das Unternehmen investieren müsste und wo der wirtschaftliche Nutzen liegt. Hieraus ließen sich sehr präzise Aussagen in puncto Wirtschaftlichkeit / Pay Back von einzelnen Business Cases ableiten.
Vierte Woche: Ergebnisse in Portfolio einordnen
Zum Abschluss ordnete das Projektteam je Standort ca. 40 Schwerpunkthemen und Initiativen aus den vorangegangenen Wochen in ein Portfolio mit drei Gliederungskriterien ein:
- Wie groß ist der vorhandene Effizienz-Hebel und wie hoch sind die möglichen Kosteneinsparungen?
- Was kostet das Ganze im Endeffekt?
- Wie schnell lässt sich das Thema umsetzen?
>100 Millionen Produkteinheiten pro Jahr lassen sich mit fahrerlosen Transportsysteme besser choreographieren.
Pilotprojekte für die Industrie 4.0
Das Team filterte u.a. drei Themen heraus, die schnell realisierbar sind, in der Umsetzung wenig kosten und zugleich einen großen Benefit bringen. Die anderen Schwerpunkte aus dem Portfolio kamen auf die Liste „offene Punkte“, um sie zu einem späteren Zeitpunkt umzusetzen. Nach einer Portfolioauswertung aller Entscheidungsinstanzen im Unternehmen startete man u.a. die Umsetzung von:
- Fahrerlosen Transportsystemen für einen smarten Materialfluss
- Cobots (kollaborative Robotik) zur Unterstützung der Mitarbeiter:innen
- Real-Time-Tracking-Systemen für mehr Datentransparenz und eine präzisere Kenntnis der Umlaufbestände
Machbarkeitsstudien sichern Anwendungserfolge
Für den Cobot-Einsatz führte das Projektteam eine Machbarkeitsstudie durch. Mehrere hundert Meter lange Anlagen bzw. Linien in den Werken sorgen für lange Laufwege, um die Anlagen zu Beschicken oder leere Blister zu entfernen. Cobots können die Mitarbeiter:innen hierbei erheblich entlasten. Ein entsprechender Testlauf mit einem Cobot in einer Pilotumgebung zeigte, das alle Prozesse für einen reibungsfreien und vor allem sicheren Ablauf funktionieren. Auch wenn dieser Part eher der klassischen Automatisierung als der Digitalisierung zuzuordnen ist, trägt er erheblich zur Smart Factory Transformation des Werkes bei.
Real-Time-Tracking Systeme verbessern Informationsfluss
Wo im Werk welche Bestände liegen, konnte auch das Unternehmen in diesem Fall vor der Planung seiner Smart Factories nicht 100%ig genau sagen. Ärgerlich ist diese Intransparenz vor allem dann, wenn Maschinen umgerüstet werden und die benötigten Teile fehlen. Das hat zwar keinerlei Auswirkungen auf die Qualität des Endproduktes, aber es geht oftmals ein erheblicher Prozentsatz an Anlagenverfügbarkeit verloren. Im schlimmsten Fall sind Teile, die man zum Produktionsstart benötigt, nicht vorhanden oder nicht auffindbar, so dass die Fertigungslinie still steht.
Real-Time-Tracking-Lösungen mit Geofencing und RFID-Technologie, die eine direkte Ortung der Anlagenteile erlauben, kamen daher auf die Shortlist der Top-Digitalisierungsprojekte. Das Unternehmen kann somit lückenlos verfolgen, wo welcher Artikel wie gelagert und genutzt wurde und jederzeit nachvollziehen, was in der Anlage passiert. Die Informationen, die über die smarten Geofencing-Systeme generiert werden, lassen sich auch für die klassischen ERP-Abläufe nutzen.
Mit diesen Digitalisierungsinitiativen ist das Unternehmen optimal für eine weitere Smart Factory Transformation an allen vier Standorten gerüstet. Bereits in der Planungsphase konnte es mit Hilfe der Pilotprojekte die Qualität im Prozess und somit die Operation Excellence in den Standorten verbessern. Und sowohl diese Erfolge als auch die „Lessons Learned“ aus den geschilderten Projektphasen unterstützen natürlich in Zukunft einen erfolgreichen Roll-out der Smart Factory Initiative auf weitere Standorte.
40 relevante Ansatzpunkte für die Digitalisierung identifizierte das Team in einem Monat.
Lean Prinzipin erfahrbar machen
Welche unnötigen Wegstrecken legen Mitarbeiter:innen an ihren Montagestationen zurück? Wo sind Werkzeuge und Fahrzeugteile ungünstig abgelegt? Per Videoanalyse veranschaulichte das Projektteam schnell und nachvollziehbar, wo es Chancen für Zeitersparnisse gibt oder Hilfsmittel zum Einsatz kommen sollten, um Qualitätseinbußen zu minimieren. Zum gelungengen Launch der neuen Modelle trug die Videoanalyse ebenfalls bei, da die Mitarbeiter:innen so neue Arbeitsabläufe proben und verfeinern konnten. Als sehr hilfreich erwies sich auch die Visualisierung der gesamten Lean Transformation im Werk mit einer Projektlandkarte, dem „Control-Room“. Diese zeigte zum einen die wesentlichen Milestones und (Zwischen-) Ergebnisse für das C-Level-Management, zum anderen ließen sich darüber abteilungsübergreifende Fragestellungen thematisieren, eskalieren und vorantreiben.
Experimentierfreude fördern
Viele Mitarbeiter:innen probierten die Theorie der Lean Prinzipien und Methoden direkt in ihrem Arbeitsbereich aus. Das machte das Erlernte nicht nur greifbar, sondern motivierte auch zur Suche nach weiteren Zeitersparnissen. Ein Beispiel: Bei der Sitzmontage in der Limousine verteilten die Mitarbeiter:innen ihre Werkzeuge und kleinere Komponenten im Fußraum und auf den Sitzen. Beim Ramp-up des Coupes hatte das Team bereits ein Montagewagen für Werkzeuge und Teile entwickelt und getestet, das dem Fahrzeug auf dem Förderband folgt und sich schnell in den Innenraum schieben lässt. Damit ist nicht nur das Material in Reichweite und Zeit beim Ein- und Ausräumen eingespart – auch das Risiko einer Beschädigung des Fahrzeugs in diesem Arbeitsschritt sinkt deutlich.
Hot Spots im 3P-Workshop simulieren
In diesem Fall kam hinzu, dass unterschiedliche Fahrzeugmodelle mit einer sehr straffen Zeitplanung in die Montagelinie eingeführt wurden. Viele Abläufe variieren dann, etwa bei der Verkabelung, die in der neuen Limousine umfangreicher und komplexer ist als in den beiden anderen Modellen. Da es sich zudem um die erste Baureihe handelte, war kein Wissen zu Problempunkten vorhanden. Das Projektteam ging daher zweigleisig vor: für die laufende Fertigung der Limousine mit dem klassischen Lean Ansatz. Für das neue Modell identifizierte es mit den Launch-Verantwortlichen im Voraus die „Hot-Spots“: Worin unterscheiden sich die Modelle grundlegend? In welchen Prozessen gibt es mehr Inhalte?
Ihr Experte für Smart Factories
Prof. Dr. Werner Bick ist seit 1999 Generalbevollmächtigter der ROI Management Consulting AG. Seine fachlichen Schwerpunkte liegen in der Verbesserung von unternehmensinterner und -übergreifender Logistik, der Produktionsoptimierung sowie der Effizienz- und Effektivitätssteigerung im Produktentstehungsprozess. Zudem unterstützt Werner Bick Unternehmen im digitalen Transformationsprozess von der Strategie bis zur Implementierung von Industrie 4.0 / IoT-Lösungen.
Kontakt:
Tel: +49 89 1215 90-0
E-Mail kontakt.dach@efeso.com