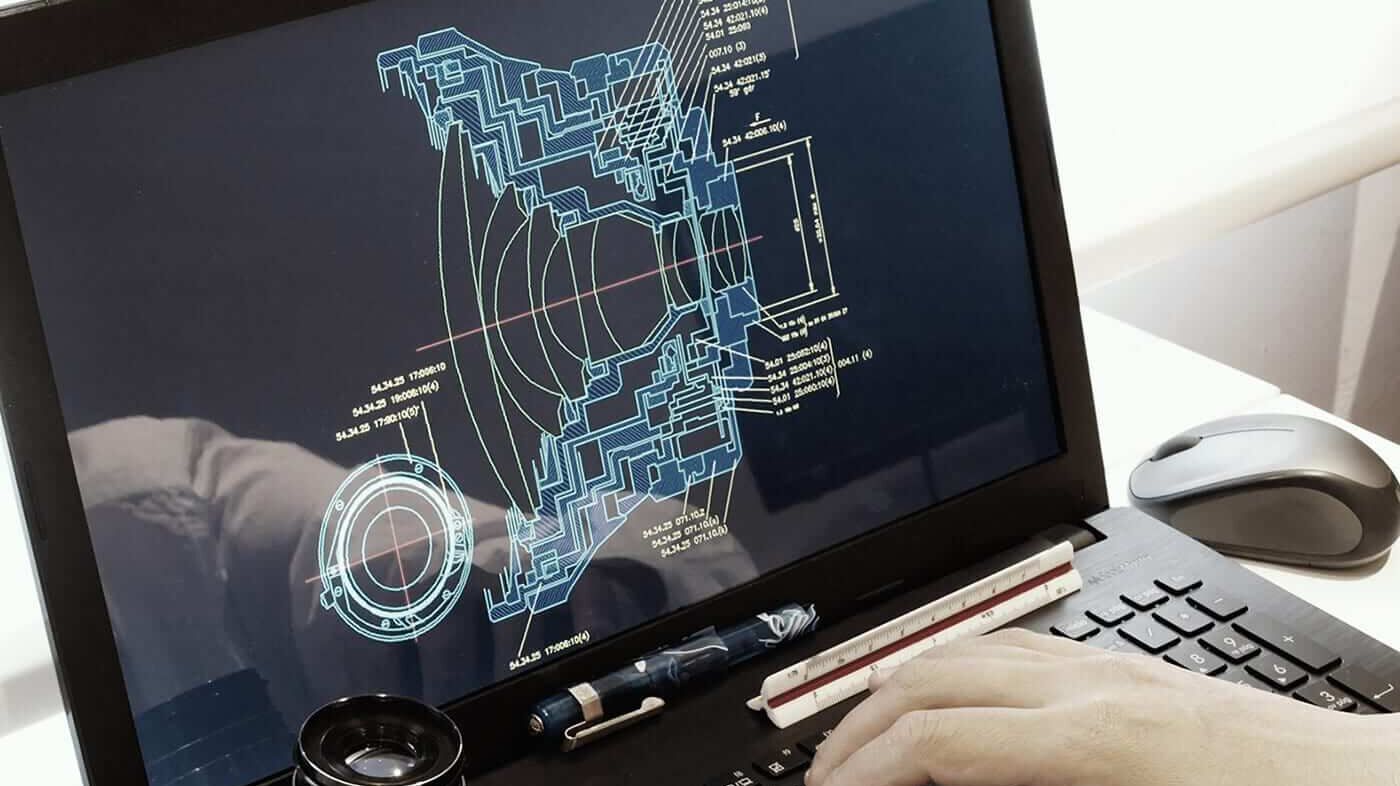
Digital Process Twin: Prozessoptimierung durch Predictive Quality und Predictive Production
Virtuelles Cockpit zum Wertstrommanagement
Bei der Verbesserung einer Fertigungsanlage für Armaturentafeln stand ein Automobilzulieferer vor zwei Herausforderungen: Die gesamte Prozesskette mit allen Risikofaktoren in Produktion und Supplier-Management sollte transparenter werden. Zugleich führten bereits kleine Fehler im Fertigungsprozess zum Ausschuss kompletter Komponenten, da ein sensibles Material verarbeitet wird – es galt nun, diese Ausschussrate zu senken. Gemeinsam mit EFESO bildete das Unternehmen dazu den gesamten Produktionsprozess mit einem „Digitalen Zwilling“ Schritt für Schritt nach. So entstand ein IoT-Pilot, der sowohl in der Fertigung als auch im Wertstrommanagement bei Lieferanten Potenziale identifiziert und Verbesserungen anstößt.
Herausforderung
Ein Automobilzulieferer verbesserte die Transparenz von Arbeits- und Organisationsprozessen in seiner Fertigungsanlage für Armaturentafeln. Es galt, bei einer hohen Variantenzahl und Taktung Fehler und Effizienzeinbußen zu identifizieren und zu eliminieren.
MEHREFESO Lösungsansatz
Mit seinem „Digital Process Twin“ senkte EFESO nicht nur die Ausschussrate, sondern machte auch über die Fertigung hinaus Parameter in den Wertschöpfungsnetzen des Unternehmens transparenter, die das Ergebnis beeinflussen.
MEHRLessons Learned
Virtuelle Prozesszwillinge tragen nicht nur zur Effizienz- und Qualitätssteigerung bei, sondern sind zudem ein wichtiger strategischer Faktor beim Aufbau eines smarten Supply Chain Managements.
MEHREFESO Erfolgsmodell
Eine Datenbasis von Prozessparametern zur Anlagen-Performance und zu Qualitätsergebnissen bildet die Grundlage für eine virtuelle Abbildung von Arbeitsschritten. Je nach Kontext entwickelt EFESO dazu ein unternehmensspezifisches Modell eines „Digital Process Twin“.
MEHRMit einer Variantenvielfalt von bis zu 600 Serien- und Individualcockpits fertigt das Unternehmen täglich mehrere tausend Cockpits. Unterschiedliche Oberflächenkonzepte erhöhen die Anzahl und Komplexität der Prozessschritte zusätzlich, etwa beim Spritzguss, Schäumen, Stanzen, Schweißen und der Montage. Allein im Schäumungsprozess werden dabei pro Schicht mehr als 1.000 Teile bei einer Taktzeit von weniger als einer Minute gefertigt. Da bleibt wenig Spielraum, um den Benchmark in Bezug auf Kosten, Qualität und Lieferfähigkeit zu definieren, die Übertragung auf externe Zulieferer sicherzustellen und Prozessverbesserungen anzustoßen.
Hohe Ausschussrate und Effizienzeinbußen
Die besondere Herausforderung lag in diesem Fall darin, dass häufig Polyurethan-Schaum verarbeitet, also geformt und gehärtet wird. Das geschieht meist mit einer signifikanten Ausschussrate, gerade vor dem Hintergrund der sehr hohen Branchenstandards. Aber nicht auf das Material, sondern auf die Arbeitsprozesse sind dabei die meisten Fehler und Effizienzeinbußen zurückzuführen: Bis zu 60 Roboterarme arbeiten an den einzelnen Produktionsschritten eines Cockpits. Nach dem Abkühlen wird der Cockpitleichtbauträger mit der später sichtbaren Cockpithaut verbunden. Das geschieht an einem karussellartigen Apparat, dem Schäumrundtisch. Auf diesem Rundtischelement stehen 14 Werkzeuge parat, die auf zwei Ebenen bestückt werden. Gleichzeitig sind jeweils zehn Werkzeuge in Betrieb. Dieses Fertigungssegment nahm der Automobilzulieferer nun gemeinsam mit EFESO genau unter die Lupe.
Performance und Qualität im Fokus
Als Startpunkt definierte das Projektteam Prozessparameter, die sowohl die Performance der Anlage als auch das Qualitätsergebnis beeinflussen können. Die Ableitung dieser Werte erfolgte erfahrungsbasiert und erfasste zunächst weit über hundert unterschiedliche Parameter, die man im weiteren Analyseverlauf reduzierte oder ergänzte. Im nächsten Schritt sorgte das Projektteam dafür, dass die vorhandenen Prozessdaten richtig aggregiert und aufbereitet wurden, und sammelte Daten, die bislang nicht aufgenommen wurden. Mit zusätzlichen Sensoren erfasste das Team außerdem neue, im Hinblick auf die definierten Parameter notwendige Daten.
Digital Process Twin von EFESO
Die auf diese Weise generierte Datenbasis wurde anschließend in einer Cloud-Anwendung zusammengeführt und analysiert. Auf dieser Grundlage entwickelte das Projektteam ein Modell, das den zu verbessernden Prozess der Fertigungsanlage für Armaturentafeln möglichst genau abbildete – also alle relevanten Parameter, deren Wechselwirkungen und kritische Werte. Dieses Modell kann, wie der Prozess selbst, zudem weit über das eigene Unternehmen hinausreichen. Im beschriebenen Fall etwa zum Logistiker, der den Schaum transportiert oder sogar zum Hersteller des Schaums. Denn die Problemursachen im Schäumungsprozess – etwa für das empfindliche Polyurethan gefährliche Temperaturschwankungen – können an jeder Schnittstelle der Wertschöpfungskette entstehen. Im Ergebnis erhielt das Unternehmen ein digitales Prozessabbild, das den gesamten physischen Prozess in Echtzeit überwacht und ein frühzeitiges Eingreifen auf Basis kritischer Prozessparameter erlaubt – einen „Digital Process Twin“.
Präziser Check von Wertschöpfungsnetzen
Mit Hilfe dieses digitalen Zwillings konnte das Projektteam nicht nur die Ausschussrate der Anlage deutlich reduzieren, sondern auch die Zusammenhänge relevanter Einflussgrößen auf das Qualitätsergebnis transparenter machen. Das Unternehmen baute zudem ein Prädikationsmodell des Ergebnisses am folgenden Q-Gate auf.
Darüber hinaus bietet der „Digital Process Twin“ von EFESO völlig neue Möglichkeiten im Wertstrommanagement, etwa in der Bewertung, Steuerung und Qualifizierung von Lieferanten. Denn durch den Einsatz des virtuellen Prozessmodells lassen sich die tatsächlichen Strukturen und Prozesse in Wertschöpfungsnetzen sehr viel präziser und tiefgreifender analysieren als mit den heute üblichen Checklisten und Lean-Manuals. Damit erhielt das Unternehmen einerseits ein sehr gutes Werkzeug zur Qualifizierung seiner Lieferanten. Andererseits kann es neue Partner wesentlich schneller und einfacher integrieren, was Abhängigkeiten reduziert und den Aufbau neuer lokaler Produktionsstätten erleichtert. Damit werden virtuelle Prozesszwillinge auch zu einem eminent strategischen Faktor beim Aufbau eines smarten Supply Chain Managements.