Industrie 4.0 im Hype-Zyklus
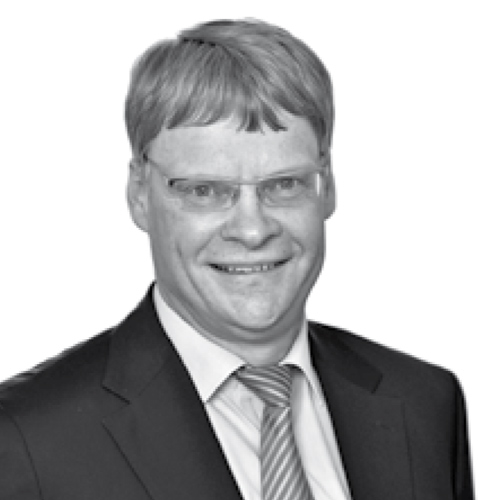
‚Industry 4.0 meets Lean‘ – unter diesem Motto hatten das F.A.Z.-Institut und die Maschinenfabrik Reinhausen GmbH am 25. Juni 2014 zu einer hochkarätig besetzten ‚Top Transfer Forum Veranstaltung‘ eingeladen. ROI hat den Kongress als Partner unterstützt. Prof. Dr. Werner Bick, Generalbevollmächtigter bei ROI und Professor an der Technischen Hochschule Regensburg sowie Dr. Johannes Pohl, Seniorberater bei ROI, haben im Rahmen der Veranstaltung einen Workshop geleitet, der sich den gemeinsamen Perspektiven des Industrie 4.0-Ansatzes und der Lean- Philosophie widmete.
DIALOG: Herr Professor bick, wie passen industrie 4.0 und lean zusammen? Wo liegen die Gemeinsamkeiten und unterschiede der beiden Ansätze?
WB: Gemeinsam ist den beiden Ansätzen, dass sie Auswege aus der rasanten Zunahme der Komplexität suchen, die wir in den letzten Jahren erleben. Komplexität heißt hier, dass wir mit zunehmend dynamischen und vernetzten Systemen konfrontiert sind – sowohl auf der Makroebene, also etwa durch die fortschreitende Integration der Volkswirtschaften und Produktionsnetzwerke, als auch auf der Ebene einzelner Fabriken. Komplexität ist enorm ressourcenintensiv. Sie beherrschen zu können, ist die Voraussetzung dafür, dass man als Unternehmen handlungs- und wettbewerbsfähig bleibt. Der zentrale Unterschied liegt in der Herangehensweise. Im Rahmen der Lean- Ansätze versuchen wir die Komplexität zu reduzieren – einfache Lösungen mit einfachen Mitteln zu erreichen. Wir zerlegen letztlich komplexe Systeme und Problemstellungen. Aber dieser Ansatz hat natürlich Grenzen – und genau hier greift der Industrie 4.0-Ansatz. Dabei geht es im Wesentlichen darum, die Komplexität aus Sicht des Anwenders zu vereinfachen, was durch eine zunehmend dezentrale Steuerung und den Einsatz von Assistenten erreicht wird. Ein Beispiel dafür sind Navigationssysteme, die für den Autofahrer die Reise selbst durch ganz Europa ziemlich einfach machen. Die enorme technologische Komplexität wird dabei an den Assistenten – in dem Fall das Navi – ‚delegiert‘, bleibt dem Gesamtsystem aber natürlich erhalten. Damit wird auch das Potenzial deutlich, das im Zusammenspiel der beiden Ansätze liegt, und deshalb werben wir dafür, diese Kombination durch Use Cases in die Praxis zu tragen.
„Im Rahmen der Lean-Ansätze versuchen wir die Komplexität zu reduzieren – einfache Lösungen mit einfachen Mitteln zu erreichen.“
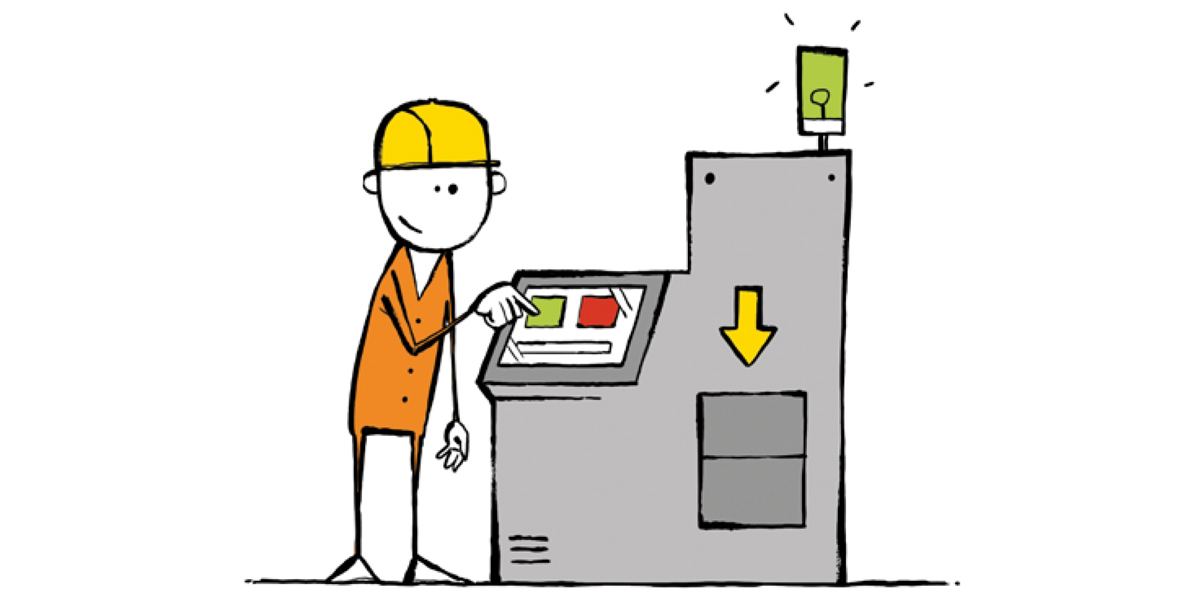
„Bei Industrie 4.0 geht es im Wesentlichen darum, die Komplexität aus Sicht des Anwenders zu vereinfachen, was durch eine zunehmend dezentrale Steuerung und den Einsatz von Assistenten erreicht wird.“
DIALOG: Das Navigationssystem ist ein gutes stichwort, denn es generiert unmengen von Daten. Welche rolle spielt big Data im kontext von industrie 4.0?
WB: Eine ganz wesentliche! Die Vernetzungsund Kommunikationsfähigkeit von Maschinen, Produktionslinien, Güterwagons oder Containern ist ja ein absolut zentrales Element einer Industrie 4.0-Architektur. Die dadurch entstehenden Daten eröffnen drei grundsätzliche Möglichkeiten.
Zum einen lassen sich Prozess und Betriebsdaten mit einem sehr hohen Genauigkeitsgrad analysieren, wodurch wertvolle Erkenntnisse für die Optimierung gewonnen werden können, etwa über die Auslastung einzelner Maschinen, Leerlaufzeiten, Umweltdaten wie Temperatur und vieles mehr. Auf dieser Basis können dann zum Beispiel wieder die Lean-Methoden greifen, oder gegebenenfalls auch Anpassungen im Maschinenpark vorgenommen werden. Zum anderen können natürlich die Wartungsprozesse deutlich optimiert werden, was zu signifikanten Einsparungen und längerer Lebensdauer des Maschinenparks führt. Die Wartungsarbeiten werden günstiger und einfacher, weil perspektivisch ein Großteil auch über Fernzugriff erfolgen kann.
Und schließlich entstehen dadurch in Summe die Chancen, völlig neue Geschäftsmodelle zu entwickeln. So werden die Maschinenbauer in Zukunft ein großes Serviceportfolio aufbauen, denn aus den Daten ihrer weltweit aufgestellten Maschinen werden sie Benchmarks und Best Practices bis hin zu Cluster- und Signifikanzanalysen ableiten und so ihre Kunden dabei unterstützen können, die Produktionsprozesse laufend zu optimieren. Das alles ist bereits heute weit weniger Zukunftsmusik, als es scheint – es gibt bereits Hersteller, Pioniere, die dieses Feld aktiv und auch erfolgreich austesten. Angemerkt sei noch, dass auch die Chancen, die diese Szenarien der deutschen Industrie im globalen Wettbewerb bieten, enorm sind.
DIALOG: Angesichts dieser Perspektiven stellt sich die Frage, warum die umsetzung nicht schon weiter ist. Was sind die größten stolpersteine?
WB: Von Stolpersteinen würde ich nicht sprechen. Jede neue Technologie – nehmen Sie das Gartner-Modell als Beispiel – muss erst Anlauf nehmen, die ersten enttäuschten Erwartungen verkraften, Standards ausbilden. In dieser Phase des ‚Hype-Zyklus‘ sind wir gerade.
Noch fehlt die breite Basis, aber es spricht vieles dafür, dass die Entwicklung sich in den kommenden zwei bis drei Jahren stark beschleunigt. Umso wichtiger ist es für Unternehmen, sich bereits heute mit dem Thema auseinanderzusetzen, sich zu fragen, wie hoch der eigene ‚Industrie 4.0-Reifegrad‘ ist, welche technologischen, aber auch organisatorischen und personellen Fragen noch beantwortet werden müssen.
„Unternehmen sollten sich fragen, wie hoch der eigene ‚Industrie 4.0-Reifegrad‘ ist und welche technologischen, aber auch organisatorischen und personellen Fragen noch beantwortet werden müssen.“