SIND VARIANTENFERTIGER DIE PIONIERE?
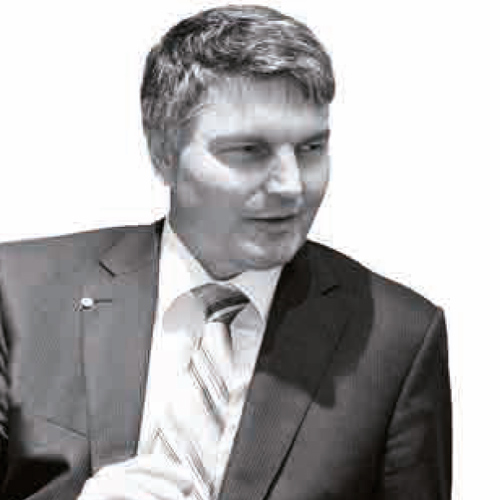
CAM, Maschinenfabrik Reinhausen www.johannhofmann.info
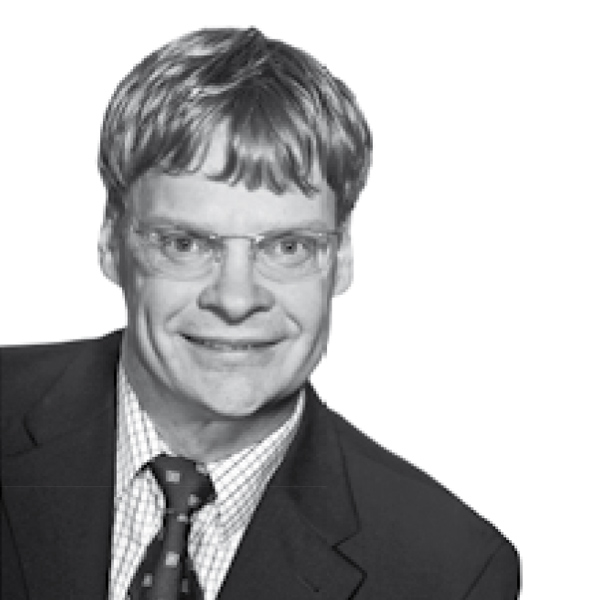
Generalbevollmächtigter, ROI
Management Consulting AG
Gespräch zwischen Johann Hofmann und Prof. Dr. Werner Bick über die Potenziale von Industrie 4.0-Lösungen in der Praxis
Im Jahr 2013 wurde von der Fachzeitschrift Produktion und der ROI Management Consulting AG zum ersten Mal ein Wettbewerb ausgeschrieben, der Industrie 4.0- Lösungen in der Praxis bewertet und prämiert. Der ROI DIALOG sprach mit dem Sieger des Industrie 4.0-Award, Johann Hofmann, Leiter des Geschäftsbereichs CAM, der Maschinenfabrik Reinhausen und dem Generalbevollmächtigten von ROI, Prof. Dr. Werner Bick, über die betriebliche Realität, IT-Strategien in der Produktion und die Weiterentwicklung von Industrie 4.0.
DIALOG: Herr Hofmann, herzlichen Glückwunsch, Sie sind der Gewinner des Industrie 4.0 Awards 2013. Was sind die Wurzeln dieses Erfolgs? Hatten Sie eine strategische Vision und eine Roadmap zur Entwicklung Ihrer Industrie 4.0 Lösung? Wenn ja, wie genau sah diese aus?
JH: Entstanden ist die Vision bereits 1989 während der ‚CIM-Euphorie‘ und war die ersten 17 Jahre nur für die Fertigung der Maschinenfabrik Reinhausen im Einsatz. Ab dem Jahr 2000 war es dann erstmalig möglich, NC-Maschinen via Netzwerktechnologie und Browsertechnik anzubinden. Das gab den Ausschlag, die mittlerweile industrieerprobten Prozesse auf WEB-Technologie umzustellen und vollständig skalierbar als Produkt MR-CM® anderen Firmen anzubieten. Interessanterweise finden sich nun viele Merkmale unserer Lösung in der Definition von Industrie 4.0. Besonderheiten der heute bei uns aktiven intelligenten Fertigung sind unter anderem die eigenentwickelte Datendrehscheibe, die vollständige vertikale und horizontale Integration, die komplette Digitalisierung der Anlagen und Werkzeuge sowie die Bereitstellung aller benötigten Daten direkt am Arbeitsplatz: wie zum Beispiel Aufspannskizzen, Rüstanweisungen oder ähnliches.
DIALOG: Sind ‚Smart Factory‘ und vernetzte Produktion für alle Branchen gleichermaßen ein Thema, oder gibt es hier Ausnahmen? Wie sind hier Ihre Erfahrungen, Herr Prof. Dr. Bick?
WB: Besonders hohen Nutzen stiftet digitale Vernetzung, wenn es sich um eine diskrete Produktion von stark individualisierten, tendenziell hochwertigen Produkten handelt. Typischerweise also in Serienproduktionen mit starken Schwankungen im Volumen und Fertigungsmix, bei denen auch Lieferanten und Kunden datentechnisch in die Wertschöpfungskette eingebunden werden müssen. Daraus kann man als Hauptanwendungsbranchen die Automobil- und Automobilzulieferindustrie sowie variantenreiche Fertiger des Maschinenbaus und der Elektroindustrie ableiten. Prozessorientierte Unternehmen mit geringen Freiheitsgraden in der Wertschöpfungskette profitieren im ersten Schritt weniger stark von Industrie 4.0-Lösungen. Diese Einschätzung deckt sich auch mit der Branchenverteilung der hoch innovativen Unternehmen, die am Industrie 4.0-Award teilgenommen haben. 40 Prozent der Firmen kamen aus dem Maschinenbau, 30 Prozent aus dem Automotive- Bereich und 20 Prozent aus der Elektrotechnik.
DIALOG: Kann man folglich sagen, dass gerade der Maschinenbau mit seinem Variantenreichtum zu den Pionieren und Wegbereitern von Industrie 4.0 gehören wird oder sogar gehören muss?
JH: Ja, denn gerade der Variantenreichtum führt zu häufigen und kostenintensiven Umrüstvorgängen. Kostendruck, zunehmende Konkurrenz aus Niedriglohnländern, sich verkürzende Produktlebenszyklen sowie steigende Qualitätsforderungen seitens der Kunden und die zunehmende Variantenvielfalt bei den Endprodukten machen für produzierende Unternehmen die Beherrschung und ständige Verbesserung ihrer Fertigungsprozesse zu einem zentralen Wettbewerbsfaktor. Der Visionen von Industrie 4.0 kommt dabei besondere Bedeutung zu. Die Produktion der Maschinenfabrik Reinhausen für das Kerngeschäft ‚Stufenschalter zur Regelung von Transformatoren‘ umfasst eine Hochleistungsfertigung und eine Montage. Kennzeichen der Fertigung sind eine hohe Streubreite der Kundenanforderungen und geringe Stückzahlen. Wesentliche Triebfeder für die Entwicklung der preisgekrönten Lösung waren Ineffizienzen beim Rüstprozess der NC-Maschinen. Hierbei tritt insbesondere – nicht nur bei der Maschinenfabrik Reinhausen – das allgemein in der Fertigung mit NC-Maschinen vorzufindende Problem zutage, dass die unterschiedlichen, an einem Fertigungsprozess beteiligten Aggregate, also beispielsweise NC-Maschinen, Voreinstellgeräte und Lagersysteme, proprietäre Datenformate verwenden und eine aggregatsübergreifende Bereitstellung der Prozessdaten regelmäßig nicht möglich war.
DIALOG: Wie ‚schlank‘ oder ‚lean‘ sind denn erfolgreiche Industrie 4.0 Lösungen, oder gibt es hier tatsächlich einen Widerspruch?
WB: Es gibt hier keinen Widerspruch, ‚Lean‘ ist die Basis effizienter Wertschöpfungsketten von Unternehmen. Man kann zwar auch schlecht aufeinander abgestimmte Prozesse automatisieren, allerdings bleiben diese dann dauerhaft schlecht, vorhandene Einspar- und Produktivitätssteigerungspotenziale werden nicht realisiert und die Kosten der Automatisierungslösung steigen zudem. Sehr gut lässt sich das auch am Beispiel der Maschinenfabrik Reinhausen zeigen. Hier findet sich ein sehr guter Umsetzungsgrad der Lean-Prinzipien: von konsequenter Durchlaufzeitverkürzung über Fehlerfreiheit (Poka Yoke) bis hin zu robusten Prozessen.
DIALOG: Eines der Bewertungskriterien beim Industrie 4.0-Award war auch der Nutzen aus Sicht von Kunden, Mitarbeitern und Gesellschaft, etwa durch eine effizientere Ressourcennutzung und verbesserte Arbeitsprozesse. Welche Erfahrungen haben Sie im Hinblick auf diese Themen gesammelt?
JH: Unsere preisgekrönte Lösung ist ein System aus der Praxis für die Praxis. Das heißt, es wurde gemeinsam mit den Maschinenbedienern entwickelt. Es befreit den Werker von fehleranfälligen und nicht wertschöpfenden Arbeiten und verbessert somit seinen Arbeitsalltag. Unsere Lösung erzeugt glücklichere und zufriedenere Mitarbeiter.
DIALOG: Lassen Sie uns einen Blick in die Zukunft werfen – was werden die nächsten Evolutionsstufen bei Industrie 4.0 sein? Und wann werden wir von Industrie 5.0 sprechen?
JH: Industrie 4.0 ist so umfassend angelegt, dass vieles davon funktionieren wird, vieles davon nicht und einiges wird ganz anders gemacht werden als es heute vorhergesagt wird. Beispielsweise die Vision ‚Cyber-Physical System‘ erfordert erst mal ‚Cyber-Physical Logistics‘. Bevor das einzelne Werkstück selbststeuernd durch die Fertigungshallen navigiert, gilt es zu klären, wer das Werkstück bewegt. Auf jeden Fall wird Industrie 4.0 – genauso wie CIM – vieles bewegen und verändern. CIM gilt zwar allgemein als gescheitert, ich bin jedoch davon überzeugt, dass CIM viel bewegt hat. Wir als Maschinenfabrik Reinhausen wären ohne die ‚CIM-Welle‘ nicht da, wo wir heute sind. Franz Kafka sagte schon: „Wege entstehen dadurch, dass man sie geht.“ Das gilt auch für Industrie 4.0. WB: Da bin ich völlig bei Ihnen, Herr Hofmann. Denn solange Industrie 4.0 in vielen Bereichen und Industrien noch Vision ist, müssen wir über ‚5.0‘ nicht spekulieren.
„Unsere Lösung erzeugt glücklichere und zufriedenere Mitarbeiter.“