DIGITAL STEEL
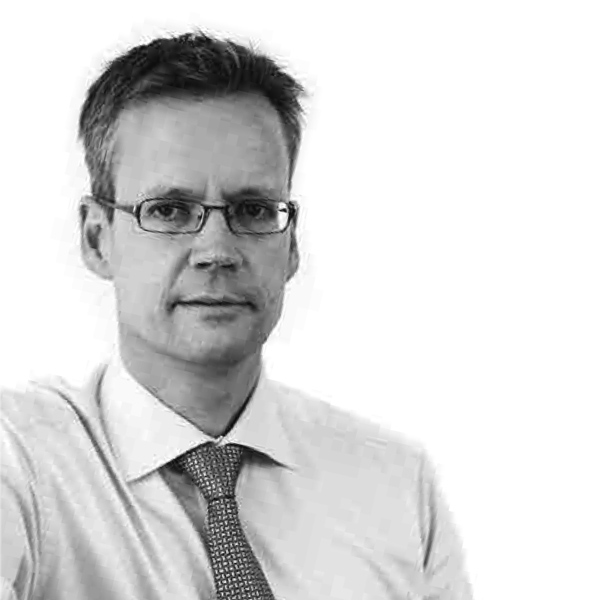
Was IT und Produktion gemeinsam bewegen können
Lassen Sie uns einen kleinen Test machen. Was ist der gemeinsame Nenner der meisten technologischen und organisatorischen Entwicklungen der letzten Jahre? Ich plädiere für Konvergenz. Das lateinische ‚Convergere‘, sich hin- oder zueinander neigen, ist das, was wir in vielen Bereichen beobachten können und das, was für uns Chance und Problem zugleich ist. Eine Chance ist es, weil aus der Kombination bekannter Elemente Neues entsteht: neue Produkte, neue Lösungen, neue Geschäftsmodelle. Ein Problem ist es, weil die Komplexität, die durch Integration bislang weitgehend unabhängiger Elemente entsteht, enorm ist: auf strategischer, technologischer, prozessualer und letztlich auch auf kultureller Ebene. Besonders gravierend ist diese Entwicklung bei der Verschmelzung digitaler und analoger Elemente, bei der Verbindung von Einsern und Nullen mit Stahl. Der bereits heute absehbare breitflächige Einsatz von Cyber-Physical Systems (CPS) in Entwicklung, Industrialisierung und Produktion hat das Potenzial, die Spielregeln in einer Vielzahl von Branchen zu ändern. Als eine Art ‚geistiger Nachfolger‘ des Internets und vor allem des Computer Integrated Manufacturing (CIM) eröffnen CPS eine neue Integrationsebene, indem sie analoge Strukturen mit Intelligenz und Kommunikationsfähigkeit ausstatten und heterogene Produktions- und Logistikumgebungen zu dezentralen Netzwerken verknüpfen.
„Wie beim Internet werden wir in den kommenden Jahren viele Flops und wenige Erfolgsmodelle erleben. Diese werden jedoch die Spielregeln in der Industrie grundlegend verändern.“
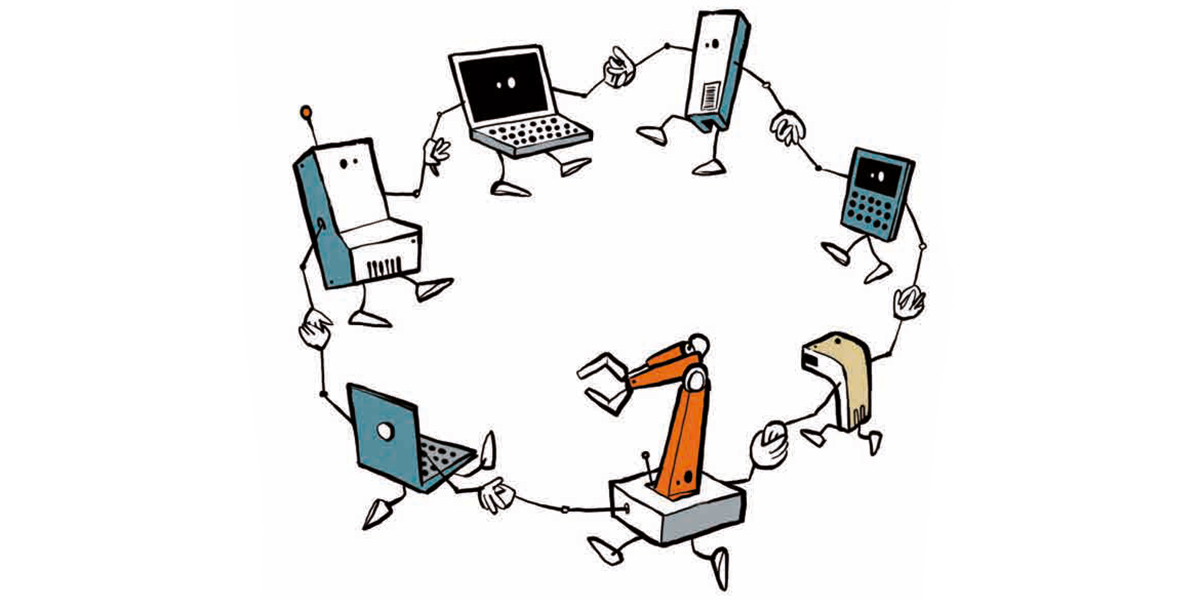
Das Netzwerkparadigma
Damit entsteht ein Prozess zur Abwicklung des Gesamtauftrags der im Gegensatz zu CIM nicht auf eine zentralistische Steuerung über Fertigungsleitstände setzt, sondern verteilt und vernetzt ist. Er ermöglicht eine Selbststeuerung der Objekte im Netzwerk und damit nicht nur eine Integration, sondern auch eine Verteilung der Steuerungsaufgaben und Informationen. Es entsteht ein Netzwerk, das im Vergleich zu traditionellen Ablaufund Aufbauorganisationsmodellen ein schnelleres und flexibleres Reagieren auf sich wandelnde Kundenerwartungen, steigenden Individualisierungsbedarf und Marktschwankungen ermöglicht. Die Rolle der IT ist dabei zentral – denn ohne sie ist das Internet der Dinge nicht möglich. Die heute zur Verfügung stehenden Technologien können die Beschränkungen überwinden, denen die CIM-Lösungen der achtziger und neunziger Jahre unterlagen und die letztlich ihren breitflächigen Einsatz verhindert haben. Doch auch hier gilt: Ähnlich wie bei internetbasierten Geschäftsmodellen muss bewiesen werden, dass eine faszinierende Basistechnologie auch in der Lage ist, konkrete Bedarfe zu befriedigen und neue Prozesslandschaften zu ermöglichen, die sich für Unternehmen – und Kunden – tatsächlich auszahlen. Und ähnlich wie beim Internet werden wir in den kommenden Jahren viele Flops und wenige Erfolgsmodelle erleben. Diese werden jedoch transformativen Charakter haben, sie werden die Spielregeln in der produzierenden Industrie grundlegend verändern.
Internet der Dinge
Ein wunderbares Beispiel dafür bietet die Maschinenfabrik Reinhausen (MR), Gewinner des aktuellen Industrie 4.0-Awards der Fachzeitschrift ‚Produktion‘: MR ist es tatsächlich gelungen, aus der Integration ehemals getrennter Einheiten nachhaltige Wettbewerbsvorteile zu generieren. MR hat, wie Johann Hofmann, Bereichsleiter CAM des Unternehmens, in dieser Ausgabe des DIALOG erzählt, ein intelligentes System entwickelt, das die unterschiedlichen Anlagen komplett miteinander vernetzt und Kommunikation und Informationsaustausch ermöglicht. Dieses einzigartige Netzwerk ist nicht zentralistisch organisiert, sondern erlaubt eine lokale Datenspeicherung. Und da, wo die Daten liegen, werden sie von den anderen Elementen des Netzwerks auch abgeholt – ein CPS und ein Internet der Dinge in Reinkultur. Änderungen und Anpassungen, die an einer Stelle initiiert werden, sind im gesamten Netzwerk in Twitter-Geschwindigkeit wirksam. Die Zeit- und Kosteneinsparungen sowie die Erhöhung der Prozesstransparenz sind enorm. Die Zukunftsrelevanz dieser Entwicklung liegt – gerade in einem Hochlohnland wie Deutschland – auf der Hand. Richtig eingesetzt, ermöglichen cyberphysikalische Systeme einen Produktivitätsschub, insbesondere im Hinblick auf Kleinserien und die Individualisierung von Produkten.
Das CPS in der Maschinenfabrik Reinhausen wirft auch ein Licht auf die grundsätzliche Struktur von Industrie 4.0. Dazu zählen einerseits die Manufacturing Execution Systeme (MES), die den operativen Auftragsdurchlauf und damit auch den Informationsaustausch zwischen den Elementen des Produktionsnetzwerks steuern. Dies ist ein Bereich, der heute bei der praktischen Auseinandersetzung mit Industrie 4.0 häufig im Fokus steht. Die zweite wesentliche Ebene sind Produktionsplanungs- und Steuerungssysteme (PP / PPS), die nicht nur eine technologische, sondern vor allem auch eine prozessuale Herausforderung darstellen. Um keine IT-Monstren aufzubauen, gilt es, die Grundsätze der Lean-Logik anzuwenden: Möglichst viele Bereiche der Produktion sollen anhand von Rahmendaten selbststeuernd funktionieren und eine Selbstoptimierung der Fabrik ermöglichen. So wichtig diese Planungsebene ist, findet Industrie 4.0 vor allem im Feld statt. Sie bedarf einer schlanken und flexiblen Steuerungslogik, muss aber ansonsten auf die Intelligenz des Netzwerks setzen.
„Es empfiehlt sich ein Ansatz, der von einer pragmatischen Vision geleitet wird.“
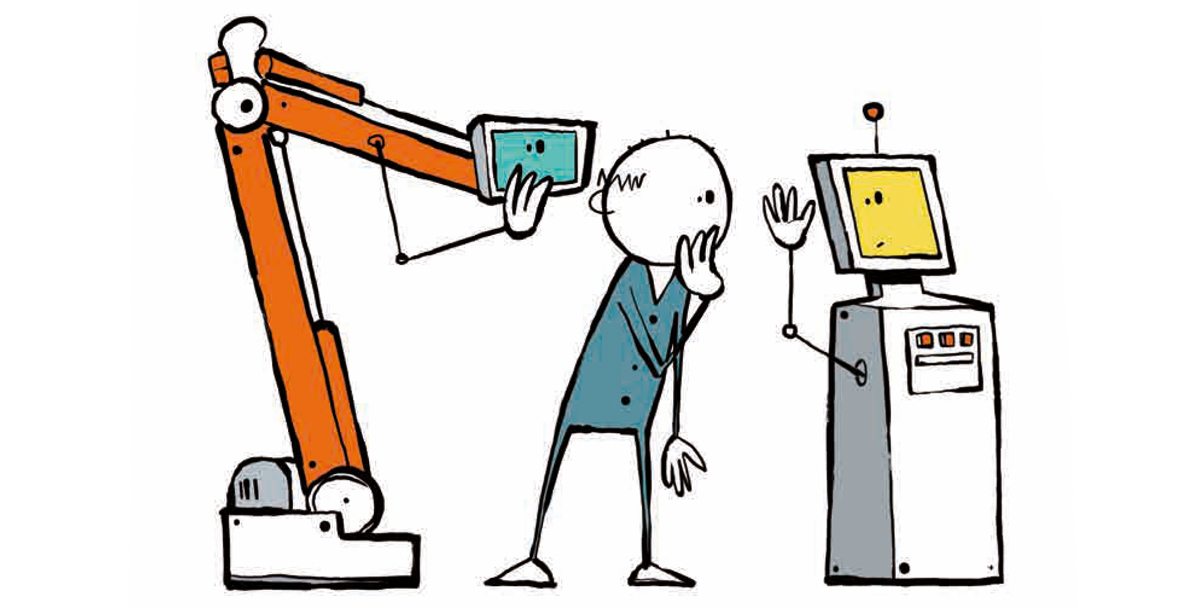
„Industrie 4.0 bleibt auch in den nächsten Jahren vor allem ein Experimentierfeld an der Schnittstelle zwischen Technologien,Prozessen, betriebswirtschaftlichen Notwendigkeiten und Inspiration.“
Grau ist alle Theorie
Aber, wie so häufig ist das leichter gesagt als getan. Denn die organisatorischen und auch kulturellen Auswirkungen einer umfassenden Industrie 4.0-Implementierung sind enorm. So wird ein Gutteil tradierter Geschäftsprozesse gründlich auf den Kopf gestellt, insbesondere weil die Abteilungs- und selbst Unternehmensgrenzen nicht mehr als Kommunikationsgrenzen fungieren dürfen. Sowohl vertikale als auch horizontale Integration sind Voraussetzung für eine Organisation, die dezentral strukturiert ist und die Intelligenz im Netzwerk verteilt. Es gibt wohl keinen Entscheidungsträger, der das nicht unterschreiben würde. Aber wohl auch kaum ein Unternehmen, das diese Art der Zusammenarbeit und Kompetenzverteilung reibungslos umgesetzt hat. Denn Netzwerkorganisationen sind unabdingbar, um die steigende Komplexität und insbesondere auch Volatilität zu beherrschen. Sie widersprechen jedoch fast unserer gesamten beruflichen Sozialisierung, unseren gelernten Interaktionsmustern und den daraus abgeleiteten Arbeits- und Organisationsformen – vorausgesetzt, die Mitarbeiter sind im Durchschnitt älter als 20. Ein weiterer schwerwiegender Faktor sind die desintegrierten und heterogenen IT-Landschaften, mit denen die meisten Unternehmen nach wie vor zu kämpfen haben. Und nicht nur die Unternehmen. Ein Blick auf den Markt der IT-Dienstleister zeigt vor allem ein Bild, das von Insellösungen und ‚Best of Breed‘ Ansätzen geprägt ist. Keiner ist derzeit geeignet, als umfassende Lösung alle technologischen Anforderungen an unternehmensspezifische Cyber-Physical Systems zu erfüllen. Vor diesem Hintergrund empfiehlt sich ein Ansatz, der von einer pragmatischen Vision geleitet wird. Das bedeutet vor allem, das Pferd nicht von hinten aufzuzäumen. Die entscheidende Frage ist, welche technologische Architektur im Hinblick auf konkrete Markt- und Kundenanforderungen entwickelt werden soll und wie umfassend diese sein muss – und nicht, wie verfügbare Technologien nutzbar gemacht werden können. Die Umsetzung wird dabei, wie in der Maschinenfabrik Reinhausen, häufig von Eigenentwicklungen und kreativen Lösungen getragen werden müssen. Industrie 4.0 bleibt deshalb auch in den nächsten Jahren vor allem ein Experimentierfeld an der Schnittstelle zwischen Technologien, Prozessen, betriebswirtschaftlichen Notwendigkeiten und Inspiration.