Wirtschaftlich produzieren mit Losgrösse 1
ROI unterstützt HASCO bei Einführung neuer Fertigungskonzepte
Die HASCO Hasenclever GmbH + Co KG, einer der weltweit führenden Anbieter für Werkzeugnormalien, bewegt sich in einem anspruchsvollen, globalisierten Markt: Denn trotz hoher Standardisierung müssen kundenindividuelle Wünsche erfüllt werden können, was teilweise zur Losgröße von nur einem Stück führt – eine extreme Herausforderung an die Wirtschaftlichkeit der Produktion. Die eng getakteten Kundenprozesse erfordern darüber hinaus Lieferfristen innerhalb eines Tages. Gleichzeitig ist der Markt durch hohe Wettbewerbsintensität und das Auftauchen neuer Player gekennzeichnet – insbesondere werden Stahllieferanten zunehmend zu Wettbewerbern. Um vor diesem Hintergrund seine führende Marktposition in Europa zu verteidigen und die Wettbewerbsfähigkeit langfristig zu sichern, hat HASCO eine strategische Initiative ins Leben gerufen, deren wesentliches Element die nachhaltige Erhöhung der Flexibilität und Effizienz der Fertigungsprozesse ist.Das ambitionierte Projekt startete mit Unterstützung von ROI im Februar 2011 und wurde, nach einer dreimonatigen Optimierungsphase, Ende September abgeschlossen. „Das Vorhaben war im Hinblick auf seine strategische Relevanz, das Investitionsvolumen und die komplexe Zielstellung äußerst ambitioniert und erforderte eine intensive und umfassende Vorbereitung“, sagt Dipl. Ing. Dirk Schulte, Senior Vice President von HASCO, der für das Projekt verantwortlich zeichnete. „Mit dem Bau der neuen Fertigungsstätte sollten Herstellkosten, Lieferzeit und Durchlaufzeit signifikant reduziert werden – was uns eindrucksvoll gelungen ist.“
Komplexität im Griff – Effizientes Projektmanagement in drei Phasen
„Der Bau einer Fabrik ist kein Tagesgeschäft. Im Rahmen des Projekts musste eine enorme Vielfalt an Themen strukturiert und aufeinander abgestimmt abgearbeitet werden – die gesamten Supply-Chain- und Fertigungsprozesse wurden detailliert analysiert und neu geplant, um eine perfekte Basis für den Bau und die Inbetriebnahme der Fertigung zu gewährleisten“, berichtet Schulte, „die hohe Komplexität und der straffe Zeitplan erforderten deshalb eine perfekt funktionierende Projektorganisation und eine enge Zusammenarbeit aller Beteiligten“.
„Kundenindividuelle Wünsche führen zur Losgröße von einem Stück – eine extreme Herausforderung an die Wirtschaftlichkeit der Produktion.“
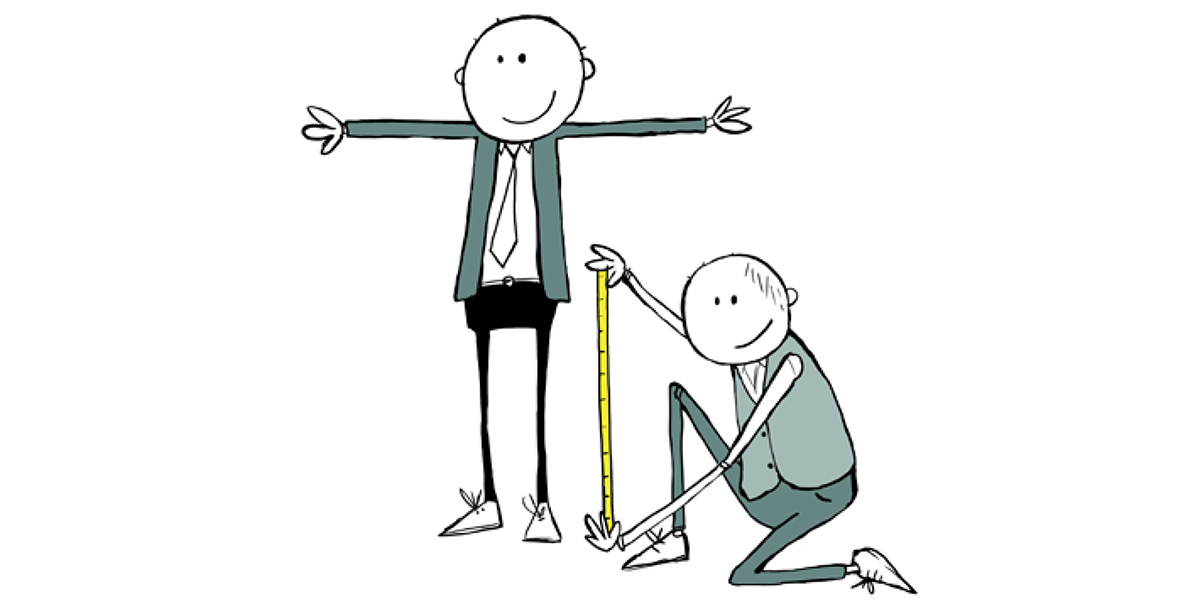
Ausgehend von einer Greenfield-Planung gliederte sich das auf 17 Monate ausgelegte Projekt in die Phasen Projektvorbereitung, Brownfield Planung und Umsetzung. In der Projektphase wurde das Bauvorhaben unter Beachtung bestehender Restriktionen evaluiert, Projektinhalte und Strukturen aufgebaut sowie die Ressourcenplanung definiert und damit die Grundlage für die Brownfield- Planung geschaffen. Dabei wurde die Möglichkeiten zur Nutzung des vorhandenen Grundstücks und der bestehenden Produktionsflächen untersucht und eine Grob-Dimensionierung der Produktion durchgeführt, wobei Planungsgrunddaten für Mengen, Typen und Varianten generiert wurden. Die Evaluierung von Greenfield-Ansätzen im Hinblick auf die veränderten Brownfield Vorgaben, insbesondere Mengengerüst, Fertigungskonzept, Lagerstufen, Logistikkonzept sowie eine detaillierte Kapazitäts- und Wirtschaftlichkeitsberechnung spielten im Projektablauf eine zentrale Rolle. Im nächsten Schritt wurde die Werks- und Infrastruktur festgelegt, sowie die Detailplanung der Fertigungs- und Supportprozesse vorgenommen. Auf dieser Basis konnte die Detailplanung Brownfield durchgeführt werden, wobei nach einer umfassenden Investitionsplanung und Baudimensionierung die Themen Technologie, Logistik, Infrastruktur, Organisation und IT im Fokus standen. Darüber hinaus wurden Konzepte für die Beschaffungsvorbereitung, Kostenplanung und Controlling erarbeitet. Dabei erwies sich der Einsatz der von ROI entwickelten Methoden ROM® und Logistik ROM® als ein wesentlicher Erfolgsfaktor: Er erlaubte sowohl die Ermittlung von Best Practice Montagezeiten schon in der frühen Projektphase als auch eine präzise Potenzial- und Prozesskostenermittlung bei Logistikprozessen. Mit dem Tool ‚Plant Simulation‘ wurde eine dynamische Ablaufsimulation von Fertigungskonzeptvarianten und interaktive 2Dund 3D-Visualisierungen durchgeführt. „Die Simulationsergebnisse erzwangen eine Anpassung des Fertigungskonzeptes, was durch unsere gute Zeitplanung beherrschbar war – ein früher Einsatz der Plant Simulation bei einem so komplexen Produktionsvorgang ist deshalb unabdingbar“, so Schulte. Schließlich wurde in der Umsetzungsphase ein Realisierungsplan erstellt, die Beschaffung initiiert und Qualifizierungsmaßnahmen durchgeführt. Darauf aufbauend wurden die Baumaßnahmen sowie der Aufbau der Infrastruktur und Organisation begonnen. Das komplexe Gesamtprojekt wurde in Arbeitspakete mit eindeutiger Zuordnung der Verantwortung für Inhalte, Dauer, Ressourcenbedarf, Ergebnisse strukturiert und durch ein effizientes Projektcontrolling flankiert.
Basis für nachhaltige Wettbewerbsfähigkeit
Mit der Inbetriebnahme der neuen Produktionsstätte in Lüdenscheid hat HASCO die Voraussetzungen für eine langfristig starke Position geschaffen und neue Standards für den Werkzeug- und Formenbau gesetzt – auch im Hinblick auf die ökologische Nachhaltigkeit: Bei Planung und Bau wurden alle aktuellen Umweltanforderungen und Energierichtlinien berücksichtigt und ein umfassendes Konzept zur Energieerzeugung und -rückgewinnung realisiert. „Mit dem erfolgreichen Abschluss dieses Projekts haben wir nicht nur die Weichen für ein profitables Wachstum in einem sehr anspruchsvollen Marktumfeld gestellt sondern auch gezeigt, dass eine wettbewerbsfähige Produktion in Westeuropa auch langfristig möglich ist“, resümiert Schulte.
„Der erfolgreiche Projektabschluss zeigt, dass eine wettbewerbsfähige Produktion in Westeuropa auch langfristig möglich ist.“
Die HASCO Hasenclever GmbH + Co KG gehört weltweit zu den wichtigsten Komplettanbietern rund um die Herstellung von Normalien sowie standardisierten Elementen für den Formen- und Werkzeugbau. Schon 1930 beschäftigte man sich im HASCO-Stammhaus in Lüdenscheid mit der Herstellung von Formen für die Metall- und Kunststoffverarbeitung. Heute umfasst die Produktpalette von HASCO neben Platten, Auswerfern und Führungselementen moderne Qualitätsstähle, Entformungs- und Temperierelemente sowie innovative Heißkanaltechnik und Sonderbearbeitungen.