TRANSPARENZ ALS BASIS OPERATIVER EXZELLENZ
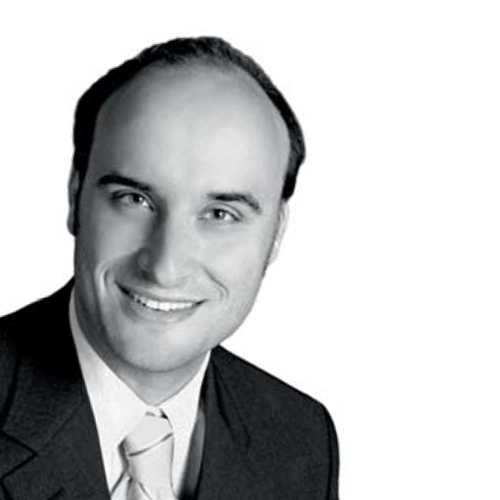
Einführung eines ganzheitlichen Produktionssystems bei der ThyssenKrupp AG
Mit dem Projekt ‚drive‘ verbessert ThyssenKrupp die operative Exzellenz und Leistung seines globalen Produktionsnetzwerkes. Gemeinsam mit der Unternehmensberatung ROI arbeitet der Weltkonzern an der Entwicklung und Einführung des ThyssenKrupp Produktionssystems. Das Ziel: mehr Arbeitssicherheit, Qualität und Produktivität entlang der gesamten Wertschöpfungskette im Produktionsprozess.
Dabei muss der Konzern in Punkto Komplexität einige Herausforderungen meistern: Allein im Geschäftsbereich ‚Components Technology‘ sind rund 29.000 Mitarbeiter an über 70 Standorten weltweit in der Produktion eingesetzt. Die ProduktpaIette ist vielseitig. Im Automobilsektor reicht sie von gebauten Nockenwellen und Zylinderkopfhaubenmodulen über Kurbelwellen, Lenkungs- und Dämpfersystemen bis hin zu Federn und Stabilisatoren sowie der Montage von Achsmodulen. Im Industriebereich liefert Components Technology Komponenten für Baumaschinen, Windkraftanlagen und zahlreiche Anwendungen des allgemeinen Maschinenbaus. Die insgesamt acht Business Units des Geschäftsbereiches halten mit ihren Produkten jeweils führende Marktpositionen. Diese gilt es kontinuierlich durch höchste Qualität und eine operationale Exzellenz in allen Wertschöpfungsprozessen zu sichern. Das umfangreiche Produktportfolio macht diese Aufgabe nicht leichter, denn es führt zu einer Vielzahl von Herstellungsverfahren. Zudem existierten aufgrund der historisch gewachsenen und durch Zukäufe erweiterten Unternehmensstruktur zum Teil unterschiedliche Produktionssysteme in den einzelnen Business Units.
„Das Produktionssystem ist unser Navigator für die Erreichung operativer Exzellenz in allen Bereichen unserer Organisation.“
Daher entwickelte der Geschäftsbereich im Projekt ‚drive‘ das ThyssenKrupp Produktionssystem (TKPS), das als Rückgrat des Unternehmens für die Operational Excellence und Performance dient. Bei der Entwicklung des Produktionssystems kam es besonders darauf an, die vielfältigen Randbedingungen der einzelnen Werke zu berücksichtigen. Dies wurde durch zwei iterativ kombinierte Ansätze – Top-Down und Bottom-Up – geschafft.
Effiziente Prozesse für mehr Nachhaltigkeit
Der strategische Rahmen des Projekts entstand aus dem ThyssenKrupp Mission Statement sowie den Leitbildern der einzelnen Business Units. Hieraus leitete das Projektteam nach dem Top- Down-Ansatz Ziele und operationalisierte Vorgaben für die Unternehmensbereiche ab. Abschließend wurden diesen Zielen Prinzipien und Methoden der schlanken Produktion zugeordnet.
„Mit diesem Vorgehen haben wir die Basis dafür geschaffen, das Produktionssystem von unten nach oben mit für den uns relevanten Inhalten weiter zu individualisieren. Das so angelegte Produktionssystem ist somit unser Navigator für die Erreichung operativer Exzellenz in allen Bereichen unserer Organisation“, sagt Dr.-Ing. Alexander Gulden, Head of BA CT Technology, Innovation & Sustain-ability und Leiter des Projektes bei der ThyssenKrupp AG. Hierzu entstand in enger Zusammenarbeit mit allen acht Business Units ein gemeinschaftliches Verständnis für ein innovatives und vor allem effektives Operational Excellence System. Ein Projektteam aus TK-Mitarbeitern und ROI Beratern sorgte für die konkrete Umsetzung dieses Anspruchs im Arbeitsalltag. Dazu leitete das Team 14 Prinzipien ab (vgl. Abbildung 1). Sie bilden die fundamentalen Kriterien des Produktionssystems.
„Neben etablierten Prinzipien wie ‚Just-In-Time‘ oder ‚Zero Defects‘ haben wir neue Prinzipien wie ‚Green Responsibility‘ oder ‚Supply Chain Integration‘ aufgenommen. Bei der ‚Supply Chain Integration‘ geht es uns vor allem darum, unsere Lieferanten noch aktiver in unsere Entwicklungs- und Produktionsprozesse einzubinden. Damit wollen wir die Durchlaufzeit unsere Produkte weiter senken, um noch flexibler produzieren zu können“, sagt Gulden.
Die 14 Prinzipien wurden anschließend inhaltlich weiter detailliert und mit konkreten Zielzuständen versehen, wie beispielsweise der Integration einer Null-Fehler- Kultur. Sie geben die zukünftige operative Richtung des Unternehmens vor. Die Einbindung der Business Units in diesen Prozess ermöglichte nicht nur die Nutzung der bereichsspezifischen Erfahrungen und den systematischen Know-how-Transfer über die einzelnen Bereiche hinweg. Sie erhöhte auch die schnelle Akzeptanz des neuen Systems bei allen Beteiligten. Auf diese Weise ist ein vollständiges und ThyssenKrupp-spezifisches Produktionssystem entstanden.
Strukturierte Einführung von Best Practices
Zur kontinuierlichen Verbesserung der einzelnen Werke und zum strukturierten Austausch von Know-how und Best Practice wurde der sogenannte OPX Maturity Scan entwickelt. Dieses Werkzeug zur Bestimmung und Bewertung des Reifegrads des Produktionssystems basiert auf den Prinzipien des Produktionssystems. Anhand eines entsprechenden KPI-Systems lassen sich die Verbesserungen quantitativ messen und ermöglichen eine transparente Darstellung der „Operational Performance“.
Die Prinzipien stellen die Kategorien der Bewertung und die insgesamt 41 Unterpunkte mit ihren Zielzuständen die Bewertungsobergrenze (Level 5) dar. Die Zielzustände wurden auf die verschiedenen Ausprägungsstufen (Level 0 – 4) heruntergebrochen. So wurde eine homogene Einordnung der Performance erreicht. Außerdem lässt sich damit das Verbesserungspotenzial des bewerteten Werkes zum nächst höheren Level direkt ablesen. Zudem kann man daraus konkrete Maßnahmen ableiten. Bei jeder Level 5-Bewertung eines Werks werden die vorhandenen Best Practice Lösungen dokumentiert und dienen den anderen Werken als Vorlage für die Umsetzung.
Produktivitätssteigerungen dank jährlicher Bewertung Die Bewertung der einzelnen Werke wird im Rahmen der Operational Excellence Initiative zukünftig jährlich durchgeführt. Sie schafft eine unternehmensweite Transparenz der Leistungsfähigkeit nach einheitlichen Standards. Dies ermöglicht eine konsistente operative und strategische Zielplanung auf Werks- sowie Unternehmensebene. Zudem wird der werksübergreifende Austausch von Know-how und Ressourcen stark vereinfacht. Das Zusammenspiel des Produktionssystems und des Werkzeugs zur Reifegradbewertung erlaubt eine effiziente und kontinuierliche Produktivitätssteigerung der gesamten Produktionslandschaft der Business Area Components Technology.
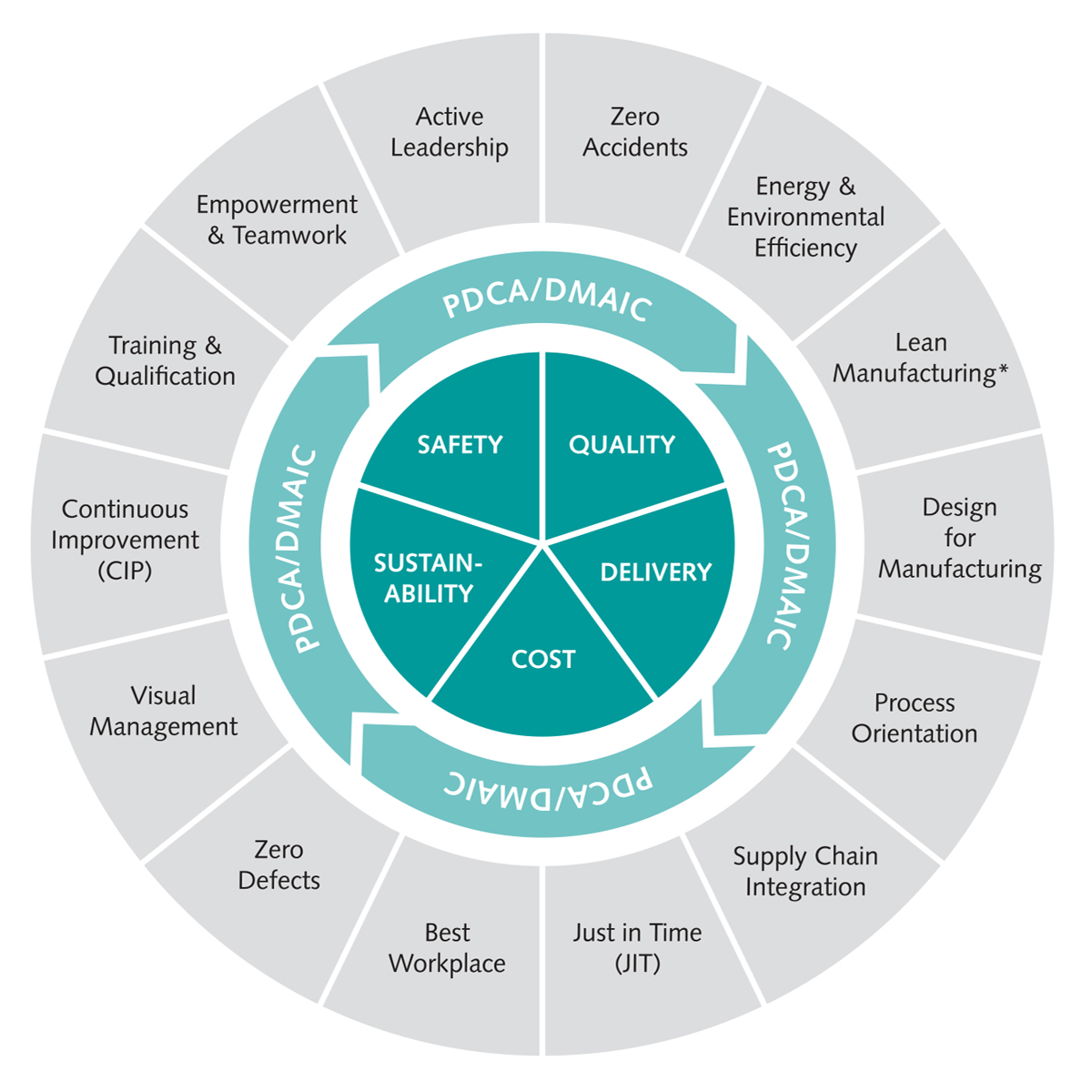
*Gestaltung von Anlagen- und Maschinenkonzepten unter Lean-Gesichtspunkten
ThyssenKrupp AG
Die ThyssenKrupp AG ist Deutschlands größtes Stahl- und Technologieunternehmen. Der Konzern erwirtschaftete mit rund 160.000 Mitarbeitern in knapp 80 Ländern im Geschäftsjahr 2013/2014 einen Umsatz von rund 41 Mrd. €. Weltweit besitzt ThyssenKrupp direkt oder indirekt mehr als 850 Tochterunternehmen und Beteiligungen. Insgesamt bestehen international 2.500 Produktionsstätten, Büros und Servicestützpunkte, zwei Drittel außerhalb Deutschlands.
www.thyssenkrupp.com