ALLES IM TAKT
UMSTELLUNG VON DER STANDPLATZAUF DIE TAKTMONTAGE BEI DER MAPLAN GMBH
Nach wie vor gilt die Werkstättenfertigung als Mittel der Wahl bei der Produktion von komplexen Produkten mit einer hohen Variantenvielfalt, wie etwa im Sondermaschinenbau. Der Fall der MAPLAN GmbH zeigt jedoch, wie auch in extrem komplexen Produktionsumgebungen die Einführung des Takt-Prinzips möglich wird und dadurch die Durchlaufzeiten radikal reduziert werden können.
Als die MAPLAN GmbH 2016 ihren Produktionsstandort in Kottingbrunn eröffnete, wagte sie sich gleich in zweifacher Hinsicht auf unbekanntes Terrain. Zum einen weil der Hersteller von Elastomer-Spritzgießmaschinen sein bisheriges Stammwerk in Ternitz durch eine komplett neue Fabrik ersetzte. Zum anderen weil MAPLAN dort als erster Hersteller im Elastomer-Bereich überhaupt eine getaktete Fließmontage realisierte. Bislang wurden die Spritzgießmaschinen und -pressen dort ausschließlich in der Standplatz-Montage gefertigt, wobei ein Großteil der Komponenten gleichzeitig an die Maschine gebracht wurde. Die Umstellung auf eine Taktmontage stellte insbesondere im Hinblick auf die hohe Variantenvielfalt eine enorme Herausforderung dar. Denn nahezu alle am Standort gefertigten Anlagen sind Einzelstücke, mit kundenindividuellen Besonderheiten.
ABTAKTUNG MITHILFE VON „ROM“
Aufgrund dieser hohen Variantenvielfalt variieren auch die Arbeitsinhalte innerhalb der Linie sehr stark. Um trotz dieser Schwankungen eine getaktete Montage sicherzustellen, entwickelte und bewertete ROI mithilfe der ROI-Tools ROM® zunächst den optimalen Montageprozess. ROM® – die ROI-Operationsfolge-Methode – ist ein System vorbestimmter Zeiten, mit dem auf Basis der Stückliste eine sehr schnelle und fundierte Bestimmung von Best-Practice-Zeiten, die ein optimiertes und verschwendungsfreies Montage- und Materialbereitstellsystem simulieren, möglich ist. Die so gewonnenen Informationen bildeten zum einen die Grundlage für die Abtaktung und ein flexibles Personal-Einsatzkonzept, bei dem die Mitarbeiter nicht mehr ausschließlich an einem festen Arbeitsplatz eingesetzt werden, sondern teilweise mit der Maschine mitwandern. Zum anderen wurden durch die intensive Auseinandersetzung mit jedem einzelnen Bauteil auch Optimierungspotenziale sichtbar, die gemeinsam mit den Konstrukteuren umgesetzt wurden.
SELBSTSTEUERNDER MATERIALFLUSS DANK INTELLIGENTEM LOGISTIKKONZEPT
Darüber hinaus lieferte ROI ein auf die neue Montageform angepasstes Logistikkonzept, mit dem ein optimaler Materialfluss vom Wareneingang bis zum Versand sichergestellt werden kann. Dies umfasste unter anderem die direkte Anbindung vorgelagerter Vormontageprozesse sowie die Definition von Kanban-Nachschub-Prozessen. Dabei werden die wichtigsten Lieferungen vom System automatisch nach oben gereiht und i.d.R. stunden- bzw. tagesgenau bereitgestellt. Dadurch konnten die Stehzeiten auf ein Minimum gesenkt werden.
MEHR PLATZ UND KÜRZERE DURCHLAUFZEITEN
Mithilfe des neuen Logistikkonzepts konnte der Lagerplatz um etwa die Hälfte reduziert werden, bei gleichzeitiger Verdoppelung des Lagerumschlags. Auch in der Montage zeigten die Maßnahmen Wirkung. Durch die Umstellung auf eine Taktfertigung konnte die Durchlaufzeit vom Montagebeginn bis zur Auslieferung beim Kunden von knapp einem Monat auf zwölf Tage mehr als halbiert werden. Geplant war ursprünglich, den im Takt gefertigten Anteil der Maschinen von zunächst 30 Prozent innerhalb von drei Jahren auf 70 Prozent zu steigern. „Nach nur neun Monaten liegen wir bereits bei einem Anteil von 60 Prozent“, so Wolfgang Meyer, Geschäftsführer von MAPLAN. Mit seinem innovativen Montage- und Logistikkonzept belegte das MAPLAN-Werk Kottingbrunn im Gesamtranking der „Fabrik 2018“ den zweiten Platz und holte den Sieg in der Kategorie „Green Factory 2018“. Die Veranstaltung gilt als renommiertester Produktionswettbewerb Österreichs und wird gemeinsam von Fraunhofer Austria und WEKA Industrie Medien durchgeführt.
Mehr unter: https://fabrikkonferenz.at
MODUL 4: ROLL-OUT, ABSICHERUNG UND NACHHALTIGKEIT
DER LANGE WEG ZUM DAUERLÄUFER
Konsequent umgesetzt, ist Lean Manufacturing nicht nur ein Werkzeug zur Prozessoptimierung, sondern vielmehr ein Zustand der kontinuierlichen Verbesserung. Am Ende steht die Vision eines Systems, das hohe Prozessstabilität mit stetiger Experimentierfreude verbindet und dadurch für eine kontinuierliche Optimierung des Produktionssystems sorgt. Es geht somit nicht nur darum, Prozesse schlank zu gestalten, sondern sie „auf Spannung“ zu halten.
Diesen Zustand zu erreichen – und vor allem ihn langfristig abzusichern – ist eine Aufgabe, die weit über die einzelnen Bereiche hinausreicht. In der Praxis jedoch wird die Verantwortung für die kontinuierliche Weiterentwicklung der Prozesse oft an die einzelnen Mitarbeiter im Shopfloor oder in den produktionsnahen Bereichen ausgelagert. Sie allein können das aber unmöglich leisten. Stattdessen sind die Unternehmen selbst gefordert, die strukturellen Voraussetzungen für einen kontinuierlichen Verbesserungsprozess zu schaffen. Dies umfasst verschiedene Aspekte:
Qualifizierung & Know-how-Aufbau
Zentrale Voraussetzung für die nachhaltige Verankerung des Lean-Gedankens in der Organisation ist der Aufbau von eigenen Know-how-Ressourcen im Unternehmen. Dies erfolgt zum einen durch die gezielte Entwicklung von Nachwuchsführungskräften, die als Treiber des Themas im Unternehmen auftreten und den Lean-Gedanken auf Managementebene verankern, zum anderen durch den Aufbau interner Qualifizierungsinfrastrukturen, etwa mithilfe von Train-the-Trainer Programmen.
Internalisierung & Anreizsysteme
Um die Verankerung der Verbesserungskonzepte in den Fachbereichen und im Tagesgeschäft zu fördern, sollten neben regelmäßigen Weiterbildungsprogrammen zusätzliche Anreizsysteme geschaffen werden, um die Mitarbeiter auf allen Ebenen zu motivieren, sich aktiv in den Transformationsprozess einzubringen. Dies reicht von individuellen Zielvereinbarungen bis hin zu Gamification-Ansätzen oder Award-Konzepten.
Skalierung & globaler Roll-out
Das Ausrollen von Lean- bzw. OPEX-Programmen im globalen Werksverbund erfordert ein zentral gesteuertes, koordiniertes Vorgehen. Ausgehend von einer standardisierten Analyse und einem internen Benchmark aller Werke, wird dabei ein Framework aufgesetzt, das die verschiedenen Werke parallel abarbeiten können. Die Nutzung von internen Best Practices bzw. ein Leitwerk-Ansatz stellen dabei ein agiles und flexibles Vorgehen sicher und ermöglichen eine schnelle Optimierung der Produktionssysteme in der Fläche. Gleichzeitig gilt es, die neuen Zielsysteme mit den Operations-Verantwortlichen vor Ort in den lokalen Organisationen bekannt zu machen.
Standardisierung & globales Wissensmanagement
Um über die Roll-out-Phase hinaus einen effektiven Austausch zwischen den verschiedenen Standorten sicherzustellen, benötigt man globale Standards, die eine Vergleichbarkeit von Prozessen und Problemlösungsansätzen durch konsolidierte Kennzahlensysteme gewährleisten. Im zweiten Schritt gilt es, das gesammelte Prozesswissen über entsprechende Schnittstellen global bereitzustellen. Auch hier kann das globale Wissensmanagement durch Best-Practice-Sharing-Plattformen und Vernetzungsevents unterstützt werden.
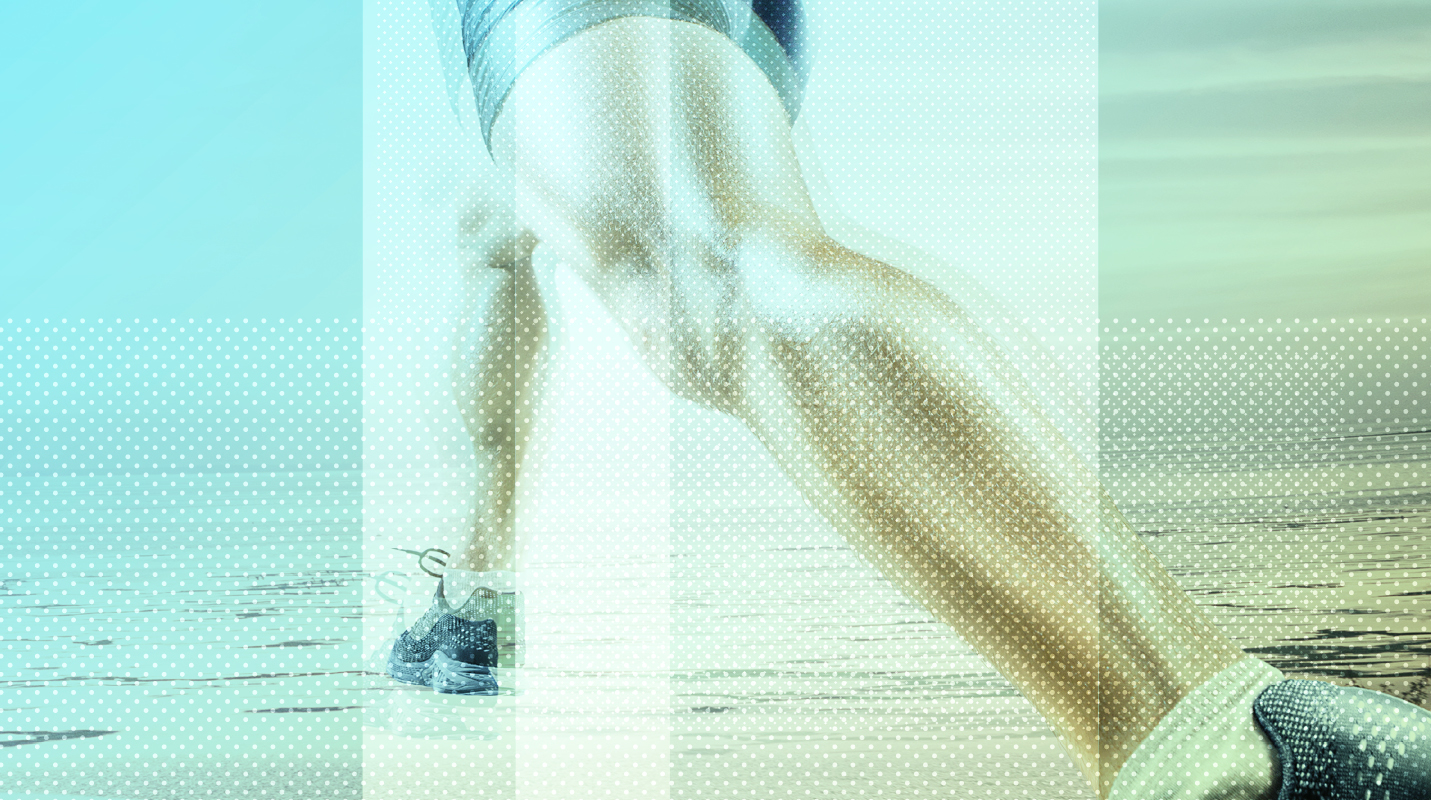