Break down the Walls!
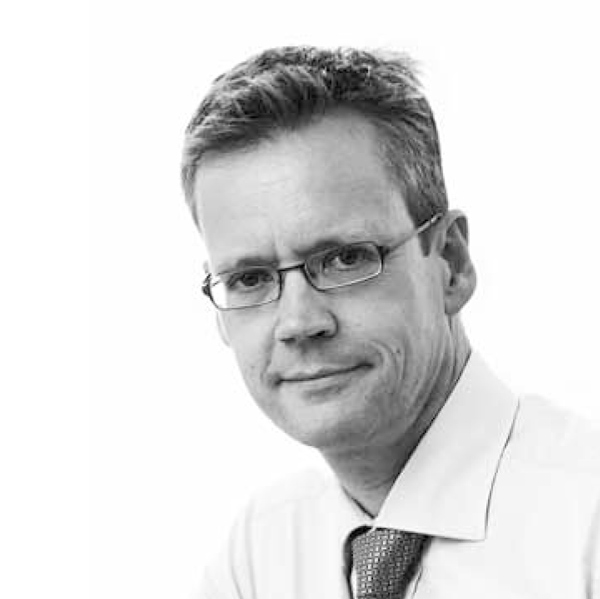
Wie Entwicklung und Produktion zueinander finden
„Soziale Systeme bestehen nicht aus Menschen, auch nicht aus Handlungen, sondern aus Kommunikation“, stellte Niklas Luhmann vor rund dreißig Jahren fest – und trieb damit Generationen von Studenten an den Rand eines Nervenzusammenbruchs. Was vielleicht daran lag, dass in den Hörsälen das falsche Publikum saß. Denn ich würde wetten, dass viele Praktiker aus den Entwicklungs- und Produktionsabteilungen ihn auf Anhieb verstanden hätten. Für Luhmann zeichnet ein soziales System sich dadurch aus, dass es die Welt selektiv, auf seine ganz spezifische Weise, wahrnimmt und sich durch die entsprechende Wahl der Kommunikation von seiner Umwelt abschließt – und zwar luftdicht. Das Zusammenwirken verschiedener Unternehmensfunktionen ist mehr als oft lebendig gewordene Theorie: Man plant, budgetiert, entwickelt und produziert nach bestem Gewissen aneinander vorbei. Man redet auch schon mal über gemeinsame Themen – und meint in den seltensten Fällen exakt das Gleiche. Der Erfolg bereichsübergreifender Projekte wird damit prinzipiell zu einem recht unwahrscheinlichen Ereignis – was gerade im Hinblick auf Entwicklung und Produktion besonders kritisch ist. Denn ein Produktentstehungsprozess besteht typischerweise aus fünf Phasen, in denen F&E und Produktion intensiv zusammenarbeiten müssen – von der Spezifikation über die Produktentwicklung und Musterfertigung bis hin zur Serienreife und dem Produktionsstart. Mir sind nur sehr wenige Unternehmen bekannt, die diesen zentralen Wertschöpfungsprozess dem Zufall oder der Intuition der Beteiligten überlassen. Deshalb existieren umfassende und detailliert ausgearbeitete Beschreibungen von Produktentstehungsprozessen, Verfahrensanweisungen und Vorgaben – die in aller Regel von den Mitarbeitern auch eingehalten werden. Am Ende der Entwicklungsphase steht ein Ergebnis, das mehr oder weniger mühelos die Gateways passiert und im Hinblick auf Zeit-, Kosten-, und Qualitätsvorgaben im grünen Bereich ist.
„Simultaneous Engineering ist eine Art Generalschlüssel zu den vielen geschlossenen Systemen im Produktentstehungsprozess.“
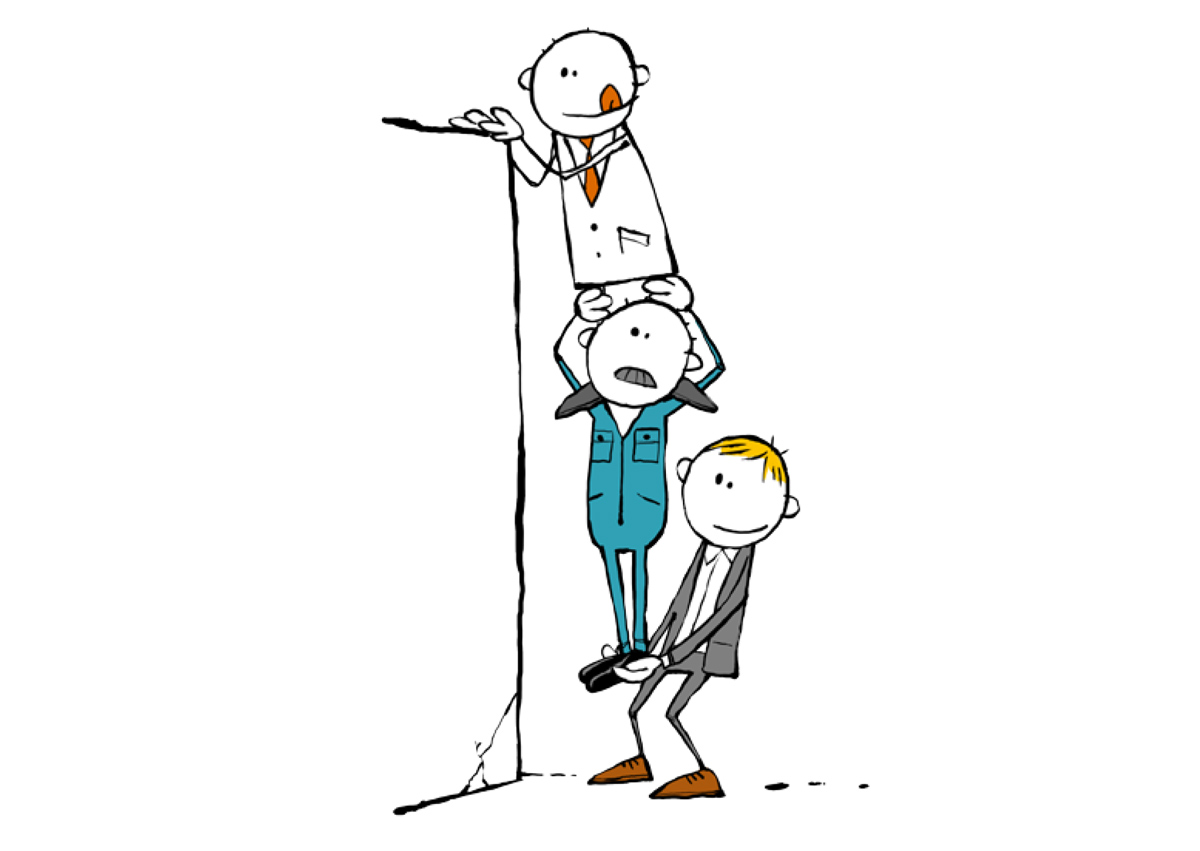
Das Problem ist nur: Es ist nicht das Endprodukt. Denn sobald dieses allen Qualitätskriterien genügende Werk den Reinraum der Entwicklungsabteilung in Richtung Industrial Engineering und Produktion verlässt, kommt Sand ins Getriebe. Zum Beispiel, wenn die Kollegen schlicht keinen Ansatz finden, um ein dem fein säuberlich konstruierten Teil angemessenes Herstellungsverfahren zu entwickeln und es in eine wirtschaftliche Serienproduktion zu überführen. Etwa weil ein Kunststoff sich nicht so verarbeiten lässt, wie die Entwicklungsabteilung es vorgesehen hat. Letztere konstruiert das entsprechende Teil dann neu – was für eine Reihe weiterer Teile Implikationen hat – mit katastrophalen Folgen sowohl für die Zeit- und Kosteneffizienz eines Projekts als auch für die Kundenzufriedenheit und das Nervenkostüm der Beteiligten.
Der Ausweg aus dieser Falle heißt Simultaneous Engineering (SE), eine Art Generalschlüssel zu den vielen geschlossenen Systemen im Produktentstehungsprozess (PEP).SE nimmt es mit der Logik der Prozessphasen nicht so genau, sondern setzt im Gegenteil darauf, die Beteiligten gerade an den Schnittstellen der einzelnen Prozessphasen gemeinsam agieren zu lassen. Diese Strategie schlägt sich in der frühzeitigen Einbindung aller Bereiche nieder, die für technisch kritische, oder im Hinblick auf ihren Herstellkostenanteil überproportional bedeutsame Komponenten verantwortlich sind.
Was konkret bedeutet, dass beispielsweise eine Zeichnung erst dann freigegeben werden kann, wenn ein Fertigungsexperte sie gegengezeichnet hat, der wiederum das Feedback weiterer beteiligter Bereiche und Zulieferer eingeholt hat. Wenn Industrial Engineering, Einkauf und Entwicklung sich auf diese Weise gegenseitig über die Schulter schauen, sinkt die Wahrscheinlichkeit von Fehlkonstruktionen oder eines Rohstoffengpasses immens – und damit auch die Kosten und Zeitverluste, die dadurch entstehen, dass Fehler erst in einer späteren Prozessphase entdeckt werden. Die Annahme liegt deshalb nahe, dass SE heute zum Standard in der produzierenden Industrie gehört, zumal sich industrielle Strukturen tiefgreifend verändern. Neben der zunehmenden Variantenvielfalt und Produktkomplexität ist es die dramatische Verkürzung der Lebenszyklen, die etablierte, sequenziell ausgelegte Prozessmodelle an ihre Grenzen bringt. So beträgt die Kernentwicklungszeit eines PKWs heute häufig nur noch zwei Jahre. Eine sukzessive Abarbeitung notwendiger Prozessschritte ist hier schlicht unmöglich.
„Die Einführung von SE scheitert häufig daran, dass Industrial Engineering und Einkauf mit Feuerwehreinsätzen ausgelastet sind.“
Obwohl das simultane Vorgehen in vielen PEP-Dokumentationen verbindlich beschrieben ist, sieht die Realität oft anders aus. Und dafür gibt es gewichtige Gründe. Denn SE erfordert gerade in den frühen Phasen eines Produktentstehungsprozesses eine intensive interdisziplinäre Zusammenarbeit und zunächst höheren Ressourcenaufwand, da parallel startende Prozesse auf deutlich weniger Vorgaben basieren, als bei einem sequenziellen Ablauf. Doch Ressourcen und Zeit sind Mangelware in Unternehmen. Heute prägen immer noch die im Feuerwehr-Modus arbeitenden Industrial Engineers oder Einkäufer, die einen signifikanten Teil ihrer Zeit dafür aufwenden müssen, Brände in laufenden Projekten zu löschen, das Bild der industriellen Fertigung.
Auflösen lässt sich dieses Dilemma nur, wenn ein Prozess- und Schnittstellenmanagement etabliert wird, das dem Druck gewachsen ist, und das durch eine nachhaltige Entlastung der wichtigsten Akteure die Voraussetzungen für ein schlagkräftiges SE schafft. Der wichtigste Schritt ist dabei die Diagnose. Denn bereits das Erkennen der dringendsten Probleme und die Identifikation der kritischsten Fehlerherde stellt viele Unternehmen vor enorme Herausforderungen. Es ist sowohl eine Menge an Wissen und Erfahrung als auch kommunikatives und politisches Geschick notwendig, um die Systeme Entwicklung und Produktion sowohl füreinander als auch für eine gemeinsame Situationsanalyse zu öffnen.
Ein mit dieser Aufgabe betrauter Experte muss einerseits in der Lage sein, die für das SE notwendigen Prozesse zu verstehen und das entsprechende methodische Know-how anzuwenden. Vor allem muss er aber über tiefe Branchen- und Fachkenntnisse verfügen, um im Dialog mit den Beteiligten sprachfähig und glaubwürdig zu sein. Dieses Verständnis innerer Zusammenhänge ist in Entwicklung und Produktion von besonderer Brisanz. Die Industriesoziologen Michel Crozier und Erhard Friedberg sprechen in diesem Kontext von einem sogenannten Marginal- Sécant – einem Akteur der ‚mehreren in Beziehung zueinander stehenden Handlungssystemen angehört und daher die unerlässliche Rolle eines Vermittlers und Übersetzers zwischen verschiedenen, oft sogar widersprüchlichen Handlungslogiken spielen kann‘.
Gerade vor dem Hintergrund dieser anspruchsvollen Aufgabe ist es in einem SE-Projekt wichtig, die Hauptstellhebel schnell zu erkennen, unmittelbar wirksame, pragmatische Lösungen zu finden und zum nachhaltigen Standard für alle künftigen Projekte zu machen. Das sichert nicht nur die Projektinvestitionen, sondern schafft auch Vertrauen und Commitment bei den Beteiligten. Dazu gehört beispielsweise die schnelle Entlastung der kritischen Mitarbeiter, damit sie die Möglichkeit erhalten, Produktentstehungsprozesse von Anfang an zu begleiten. Front Loading statt Fire Fighting: Der anfangs höhere materielle und kommunikative Aufwand führt erfahrungsgemäß dazu, dass über den gesamten PEP hinweg bis zu einem Drittel der Ressourcen eingespart werden können – bei kürzeren Laufzeiten, besserer Qualität und höherer Marge. Wenn es da nicht lohnt, die Abteilungsmauern einzureißen …!
„SE-Projekte sparen bis zu einem Drittel der Ressourcen – und das bei kürzeren Laufzeiten, besserer Qualität und höheren Margen.“