PROGNOSESICHERHEIT MIT HUMAN AI
Wie Künstliche Intelligenz und Gamification eine globale, flexible Industrie-4.0-Supply-Chain stärken.
Es existieren nicht viele vergleichbare Industrieprodukte, deren kleinste Bestandteile in der Größenordnung von Nanometern gemessen werden. Auf einem Halbleiterbauelement wird zum Beispiel ein einzelner „Cube“, der für Ein- und Ausschaltungen sorgt, eine Million Mal platziert. Jeder Cube wird lithografisch aus Kupfer-, Aluminium- und Siliziumoxidschichten strukturiert und geätzt. Neben anderen Logikeinheiten entsteht so ein Mikrocontroller, der Steuerungsfunktionen in elektronischen Produkten übernimmt.
Bauteile, die sich ohne Weiteres hinter einem menschlichen Haar verstecken lassen, spielen in einer globalen Wertschöpfungskette somit in einer ganz eigenen Liga. Hinzu kommt, dass Halbleiterlösungen von Infineon inzwischen in vielen Produkten rund um die Welt essenziell sind, insbesondere in der Automobil- und Konsumgüterindustrie. Ein reaktionsstarkes Supply Chain Management ist notwendig, um die folgenden Herausforderungen zu meistern: Neben einem hohen Kapitalbedarf für Anlagen und Fabriken, einer intrinsisch langen Durchlaufzeit bei der Herstellung und einer hohen Bedarfsvolatilität ist auch die kurze Lebenszeit von Produkten mit Halbleitern zu nennen, denn der nächste Halbleiter ermöglicht bereits bessere Produkte. Unser weltweites Team von tausend Mitarbeitern mit einer smarten Industrie-4.0-Supply-Chain-Lösung, die kontinuierlich weiterentwickelt wird, beherrscht das.
Unser Supply Chain Business Ecosystem basiert auf einer physikalischen Make-Flexibilität und deren täglicher Optimierung in einem hochautomatisierten Planprozess. Um die Leistungsfähigkeit unserer Industrie-4.0-Supply-Chain-Lösung in diesen Bereichen weiter zu steigern, haben wir Digitalisierungsprojekte gestartet, die eine bessere Vorhersage und höhere Flexibilität garantieren.
Digitalisierung in zwei Stoßrichtungen
Die Projekte verfolgten zwei Digitalisierungsinitiativen: „Digitalization for Input“ konzentrierte sich auf bedarfsorientierte Aspekte. Neben der optimalen Nutzung verfügbarer Daten standen hier die Kompetenz der Mitarbeiter und das Change Management zur Umsetzung der Maßnahmen sowie ein Gamification-Ansatz zur Integration einer KI-gestützten Planung im Vordergrund.
Zugleich sollte „Digitalization for Execution“ die Infrastruktur für eine globale, flexible, virtuelle Fabrik schaffen, Automatisierung weiter im Unternehmen etablieren und die Reaktionsfähigkeit bei einer veränderten Auftragslage auf täglicher Basis im globalen Produktionsnetzwerk verbessern.
Mit dieser Vorgehensweise konnten wir unsere Supply Chain als Wettbewerbsvorteil weiter ausbauen und zugleich die Erfahrungswerte aus unseren Standorten bündeln, etwa zu Big-Data-Analysen in der Fertigung oder bei der Rückverfolgbarkeit von Fehlern im Qualitätsmanagement. Als besonders wichtig für den Erfolg unserer Industrie-4.0-Lösung erwiesen sich die folgenden Elemente:
COB (Customer Order Behavior)
Unser Projektteam visualisiert das Bestellverhalten von Kunden in Heatmaps auf wöchentlicher Basis über einen Zeitraum von 26 Wochen. Die zweidimensionale Darstellung erzeugt Bilder, anhand derer Experten den Kunden vordefinierte Kategorien (z.B. Über- oder Unterplanung) zuordnen können. Ist eine ausreichende Anzahl solcher Bilder zugeordnet (gelabelt), kann man diese Zuordnung einer Deep-Learning(DL)-Maschine übergeben. Dies ermöglicht eine zuverlässige und schnelle Analyse des Bestellverhaltens der Kunden, was wiederum ein besseres Verständnis des Kundenbedarfs erlaubt und Veränderungen beim Bestellverhalten erkennen lässt.
DFC 4.0 (Demand Forecaster 4.0)
Eine Prognosegenauigkeit, die maschinell besser ist als die von Menschen, ist beim DFC 4.0 umgesetzt. Der DFC 4.0 nutzt dazu historische Zeitreihendaten und „Zukunftsdaten“ und arbeitet mit einem für die beste Prognosegenauigkeit auf das individuelle Produkt optimierten Mix aus statistischen und DL/KI-Tools.
HAI Game trainiert Interaktionen zwischen Mensch und Software
Um das Change Management bei der Einführung des DFC 4.0 zu unterstützen, setzen wir zwei Tools ein: in regelmäßigen sogenannten Espresso-Mails stellt ein Mitglied der Geschäftsleitung bestimmte Funktionen des DFC 4.0 und deren Vorteile vor und bietet den Mitarbeitern an, sich über Videos, Artikel etc. weiter zu diesem Thema zu informieren.
Zudem entwickelten wir mit HAI (Human & Artificial Intelligence) ein Game, um die Zusammenarbeit mit unseren „digitalen Kollegen“ spielerisch zu verbessern. Eine KI liefert zwar meist sehr schnell bessere Prognosen als Menschen, kann diese aber nicht erklären und liegt gelegentlich grob daneben, wenn Informationen fehlen. In einem halbstündigen Spiel in 20 Runden lernt man, der Maschine schnell – ohne einzugreifen – zu vertrauen, weil die KI einfach meist besser „forecasted“ als der Spieler, der auch die Zeitreihen sieht und selbst vorhersagen könnte. Aber warum sich die Mühe machen, wenn di KI besser ist? Dies gilt sowohl in dem Fall, wenn sie sich in ihrer „Komfortzone“ befindet, aber auch dann, wenn man als Mitarbeiter mehr Informationen hat und somit eine eigene Prognose abgeben kann. Ein Aha-Erlebnis kommt zum Schluss: Hier erfährt man, wie viele Einsparungen man für das Unternehmen hätte erzielen können, wenn man sich einerseits auf die Informationen der Künstlichen Intelligenz verlassen hätte, aber auch, wie wichtig es andererseits ist, in bestimmten Situationen die Berechnung selber (und dann exakt) zu übernehmen.
Globale Supply Chain als virtuelle Fabrik mit GPN (Global Production Network)
Die globale Supply-Chain-Planung erzeugt aus Zehntausenden Bedarfselementen und Tausenden globalen Bottlenecks einen täglichen ATP (Available-to-Promise). Sie berücksichtigt produktfein, was im Distributionszentrum verfügbar ist oder tagesfein dort ankommen wird. Dieser ATP wird dann wiederum täglich von rund einer Million Auftragselementen genutzt, um die Zusage vom Vortag entweder zu bestätigen oder zu verbessern. Verbessern bedeutet hier, näher als am Tag davor zum Kundenwunschtermin zuzusagen. Dieses seit Jahren bestehende „Best of Breed“-IT-Tool eines Supply-Chain-Planungs- und Execution-Systems wurde in unserem Digitalisierungsprojekt durch das GPN ergänzt. Das GPN ermöglicht eine ganzheitliche Sicht auf Produktion, Qualitätskontrolle und Materialzuweisung über die gesamte Lieferkette. Die Auslieferung bzw. Verwendung von fehlerhaften Losen kann nun z.B. innerhalb von Minuten global gestoppt werden.
Dass die Kombination dieser Technologien und Maßnahmen Früchte trägt, zeigt sich in allen genannten Bereichen: Die vollständige Rückverfolgbarkeit der Güter bzw. Produkte vom Frontend bis zum Backend im GPN reduziert auch Fehler durch manuelle Handhabung und erzielt signifikante Einsparungen. Außerdem verbessert die Supply-Chain-Planung mit dem GPN die physische Flexibilität und damit die Gesamtauslastung der Kapazitäten um mehrere Prozentpunkte.
Für die Lösung der globalen Chip-Knappheit reicht es aber nicht, dass nur die Halbleiter-Supply-Chain funktioniert, auch die Lieferkette mit Halbleitern muss nahtlos ineinandergreifen. Just-in-Time-Methoden, die mit minimalen Lagerbeständen operieren und die Wiederbeschaffung nach Reichweite steuern, funktionieren in pandemischen Situationen nicht, wenn es Partner wie die Halbleiterindustrie gibt, die ihre intrinsisch lange Durchlaufzeit von bis zu sechs Monaten für ein Bauteil trotz 365/24 nicht weiter reduzieren kann. Bei einer Reichweitensteuerung wird eine Wiederbeschaffung erst initiiert, wenn eine bestimmte Reichweite unterschritten ist. Beispiel: Bei einem Bestand von 1.000 und einem Bedarf von 500, beträgt die Reichweite 1.000/500 = 2 (z.B. zwei Wochen). Sinkt der Bedarf dann auf 250, ist die Reichweite vier Wochen und zwei Wochen wird nichts bestellt – und schon ist der Bullwhip-Effekt (Peitscheneffekt, also die Verstärkung von Schwankungen entlang der Lieferkette) erzeugt. Im Arbeitskreis SCM des ZVEI, der von Infineon geleitet wird, gibt es bereits gute Ansätze, wie man auch dieses Problem und den Bullwhip-Effekt nachhaltig in den Griff bekommt.
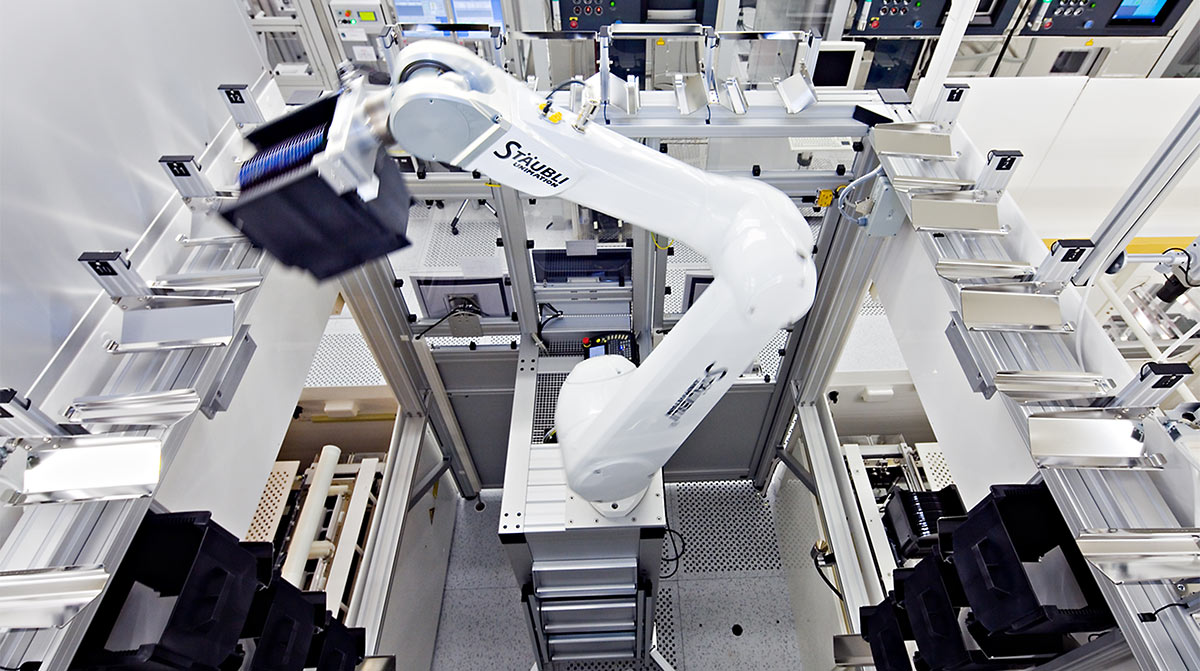
Einsatzfeld: Hightech-/Elektronikindustrie
Herausforderung
Weiterentwicklung einer Industrie-4.0-Supply-Chain-Lösung über Digitalisierungsinitiativen, um die Resilienz des Unternehmens gegenüber Volatilität und Auftragsschwankungen zu stärken
Lösung
Kombination von smarten Technologien, die Verbesserungen in mehreren Handlungsfeldern in der globalen Supply Chain adressieren, insbesondere in der kundenorientierten Bedarfsplanung und durch physikalische Flexibilität, die täglich durch Planungstools optimal genutzt wird; Verbesserung der Zusagen bei Kundenaufträgen