KURSZIEL: IDEALER ONE-PIECE-FLOW
Dank der Servolenkungen von Bosch HUAYU Steering Systems lassen sich PKW und LKW komfortabel durch den Verkehr bewegen. Das Hightech-Unternehmen ist in seinem Sektor Marktführer in China, in Wuhan fertigt es elektrische und hydraulische Servolenkungen sowie die Schlüsselkomponenten Schnecke und Ritzel mit einem Umlaufbestand von rund 70.000 Stück.
Vor fünf Jahren startete das Werk ein Projekt mit dem Ziel, die Komponentenfertigung zu optimieren und dem Leitbild des One-Piece-Flows möglichst nahe zu kommen. So sollten u.a. Durchlaufzeit und Flexibilität verbessert werden, zum Beispiel durch eine Automatisierung der manuellen Warenbewegungen zwischen Arbeitsplätzen oder durch die Digitalisierung der bisher papiergestützten Datenerfassung.
FITS: Hochflexible Planung mit begrenzten Ressourcen
Das Projektteam erzielte bereits Erfolge, als der Ausbruch der COVID-19 Pandemie in Wuhan zur Schließung des Großteils der ansässigen Unternehmen führte und der Betrieb der Fabrik mit einem Bruchteil der Belegschaft funktionieren musste. Da zu diesem Zeitpunkt bereits einige der angestrebten Technologien implementiert werden konnten, war es möglich die Produktion mit stark eingeschränkter Belegschaft aufrecht zu halten und Kundenaufträge weiterhin zu erfüllen.
Dies machte vor allem die Planungs- und Dispositionslösung FITS möglich. FITS steht für "Flexible Intelligent Transportation System" und wurde ursprünglich bei der Planung des Materialflusses der Schnecken und Ritzel konzipiert. Das System sollte die Zustandsrückmeldungen der einzelnen Anlagen in Echtzeit erfassen können und so eine präzise Produktionsplanung ermöglichen. Zudem wollte das Werk die Aufgaben der einzelnen Werkzeuge bzw. Ausrüstungen in der Fertigung flexibel an den Produktionsplan und den Zustand der Ausrüstung anpassen. Hierbei sollte auch ein dynamischer Wechsel der einzelnen Arbeitsplätze möglich gemacht werden. Die Zielvorgaben für das System lauteten somit:
- hochflexible Planung von Produktionsrouten mit begrenzten Ressourcen;
- genaue Abstimmung auf die dynamische Terminierung der einzelnen Werkzeuge / Ausrüstungsgegenstände;
- Automatisierung des Materialtransfers, Rückverfolgbarkeit einzelner Gestelle;
- Echtzeit-Rückmeldung von Materialinformationen und Echtzeit-Überwachung des Gerätestatus.
Aus der Umsetzung dieser Ziele entwickelte sich das FITS-Projekt: Durch den Einsatz eines zentralen Produktionsplanungssystems, das auf RFID- und MES-Komponenten von Fertigungssystemen basiert, gelang die Transformation des gesamten Produktionsprozesses von einer traditionellen, diskret geplanten Fertigung zu einer agilen On-Demand-Fertigung. Hierbei spielten fünf Industrie-4.0-Lösungen eine zentrale Rolle:
Kernalgorithmus und Advanced Planning and Scheduling System (APS)
Das zentrale Element des Projekts ist das "smart brain", also der Software-Algorithmus, welcher die Primärbedarfe analysiert und diese mit weiteren Informationen in ausführbare Sekundärbedarfe umwandelt. Er erfasst jedes Betriebsmittel, sodass eine Optimierung der Rüstreihenfolge im Materialfluss in kürzester Zeit erfolgen kann. In Kombination mit einem überlagerten APS-System für die Echtzeitplanung und -terminierung werden Lieferungen mit unerwarteten Produktionsschwankungen abgeglichen. Bei Abweichungen bzw. Ausnahmen wie Maschinenausfällen oder fehlendem Material initiiert das System eine automatische Umplanung: Der Produktionsplan wird automatisch aktualisiert und der Fertigungsleiter erhält eine Benachrichtigung zur Bestätigung.
Manufacturing Execution System (MES)
Zur Erfassung der im Produktionsprozess anfallenden Daten wurde ein von Bosch entwickeltes MES implementiert. Dies umfasst u.a. Funktionen wie Werkzeug-, Qualitäts-, Auftrags- und Energiemanagement, Lichtanlagensteuerung und Fertigungsdatenanalyse.
Automatic Guided Vehicles (AGVs)
Der FITS-Algorithmus erzeugt Transportaufträge auf Basis des Echtzeit-Produktionsstatus und der Materialverfügbarkeiten, die von den MES-Daten zurückgemeldet werden, und sendet sie an ein AGV-Dispatching-System. Das System führt die Transportaufträge aus und befördert so eigenständig Materialien, Komponenten und Werkzeuge zwischen den einzelnen Stationen und Arbeitsplätzen. Die einzelnen AGVs verfügen dabei über die Funktionalität, ihre Tragflächen in der Höhe zu verstellen. So werden An- und Abtransporte zwischen Fertigungszellen mit unterschiedlicher Höhe gewährleistet. Für das AGV müssen keine Bodenführungsschienen oder Magnetstreifen verlegt werden, auch das Anbringen eines QR-Codes ist nicht erforderlich, so dass minimale Bodenveränderungen überwunden werden können.
Radio-frequency Identification (RFID)
Jedes Transportgestell (welches je 48 gleiche Teile fasst) wurde mit RFID-Tags ausgestattet, jede Produktionslinie mit entsprechenden RFID-Lesegeräten. Alle Prozess- und Maschinendaten werden auf Teileebene über das MES gespeichert und mit den RFID-Daten synchronisiert. Natürlich musste auch das (automatisierte) Rüsten von Anlagen mit der Produktionsprogrammplanung synchronisiert werden.
Human Machine Interaction (HMI)
In Punkto Mensch-Maschine-Interaktion kommen im Werk Tools zum Einsatz, die wesentliche Informationen der intelligenten Fertigung visualisieren. Dies nutzt FITS zur Systemdiagnose und -überwachung. Derzeit wird im Rahmen des Projektes ein Handheld-Terminal ausgewählt, das elektronische Etiketten scannen kann. So sollen Informationen über verdachtserregende Materialien ausgelesen und die Isolierung, der Ausschuss oder die Rückgabe abwickelt werden. Mobile Tablets kommen als papierlose Devices für Vor-Ort-Inspektionen und Gerätekonfigurationen zum Einsatz. Sie sind mit dem drahtlosen Netzwerk verbunden, um den Produktionsstatus und die Qualität der Teile abzurufen und zu überwachen.
Wie nutzt man Industrie-4.0-Technologien, um die Fertigung effizienter zu machen – ohne neue Komplexität zu schaffen? Jun Bao, Werksleiter in Wuhan bei Bosch HUAYU Steering Systems, teilt Erfahrungswerte.
DIALOG: Herr Bao, welche Smart-Factory-Vision verfolgen Sie mit FITS?
JB: Das Projekt startete mit mehreren Zielen: Erstens, die unterschiedliche Anzahl und Verfügbarkeiten der Maschinen passend zu den unterschiedlichen Arbeitsprozessen zu planen. Für einen kontinuierlichen Materialfluss müssen mehrere Vorbedingungen erfüllt sein: etwa, den aktuellen Status jeder Maschine zu kennen, die Art des Bauteils, das sie produziert, und den Fertigungsfortschritt. Kurz gesagt, wir wollten quasi ein IoT für die Maschine und die dazugehörige Ausrüstung entwickeln.
Zweitens mussten wir einen Standard festlegen, da wir im Idealfall den One-Piece-Flow (Einstückfluss-Montagelinie) erreichen wollen. Wir definierten dazu zunächst ein Standardlos, das aus 48 Teilen besteht und von jeder Maschine verarbeitet werden kann. Bei jedem Los wissen wir in Echtzeit, wo es sich befindet, was der Produktionsstatus ist und wie viele der einzelnen Teile bereits bearbeitet wurden.
Drittens mussten wir uns überlegen, an welchen Stellen im Prozess eine Implementierung der angestrebten Lösungen sinnvoll und profitabel sein würde. Beim One-Piece-Flow gibt es keine zusätzlichen, nicht-wertschöpfenden Operationen, wie das Bewegen von Komponenten. Was voraussetzt, dass sich diese Komponenten von selbst oder automatisch bewegen. Also mussten wir einen Weg finden, um ein einzelnes Los von einer Station oder von einer Maschine zu einer anderen zu transportieren.
DIALOG: Aber der Zustand jeder Maschine kann sich ja ständig verändern. Wie haben Sie diese Komplexität in den Griff bekommen?
JB: Mit dem „smarten“ Kernstück unserer Lösung, einem Software-Algorithmus zur Datenanalyse, welcher den Status der Komponenten und den Status der Maschinen kennt. Und der außerdem jedem AGV und jeder Maschine aktiv Anweisungen geben kann, was jetzt oder als nächstes zu tun ist. Unser FITS-Algorithmus kann aber noch mehr: Er empfängt das Feedback der Maschinen und reagiert darauf. Falls etwa plötzlich eine Maschine ausfällt, informiert uns FITS direkt und macht Vorschläge, wie wir reagieren können, z.B. indem wir in einem bestimmten Zeitrahmen auf andere Maschinen umschalten.
DIALOG: Was hat Ihr Projekt neben diesem Technologieeinsatz erfolgreich gemacht?
JB: Die Teamarbeit und die Entwicklung der Kompetenzen. In der Vergangenheit hatten die Teammitglieder meist unterschiedliche Rollen und fachliche Expertisen, nicht nur bei uns, sondern natürlich in der Fertigungsindustrie ganz allgemein. Diese Rollen entwickeln sich weiter, da ein multidisziplinärer Kompetenzaufbau immer wichtiger wird.
Und dazu muss man den Blick über die Grenzen der eigenen Disziplin hinaus wagen, so entstehen spannende neue Ideen und Lösungen. Im FITS-Projekt haben wir zum Beispiel erkannt, wie wichtig es ist, dass ein Verfahrensingenieur auch über IT-Kenntnisse verfügt. Ein Wartungsingenieur sollte nicht nur wissen, wie ein AGV funktioniert und wie man es wartet – sondern auch, wie man ein neues AGV vermarktet. Wenn man so viele nützliche IoT-Lösungen wie möglich implementieren will, muss man darauf achten, wer sich im Team welches Wissen bzw. welche Kompetenzen aneignet. Es ist wichtig, dass Teams auf diese Weise ‚wachsen‘ können. Wer das unterstützt, profitiert von motivierten Teams, die Industrie-4.0-Lösungen planen, umsetzen und weiterentwickeln können
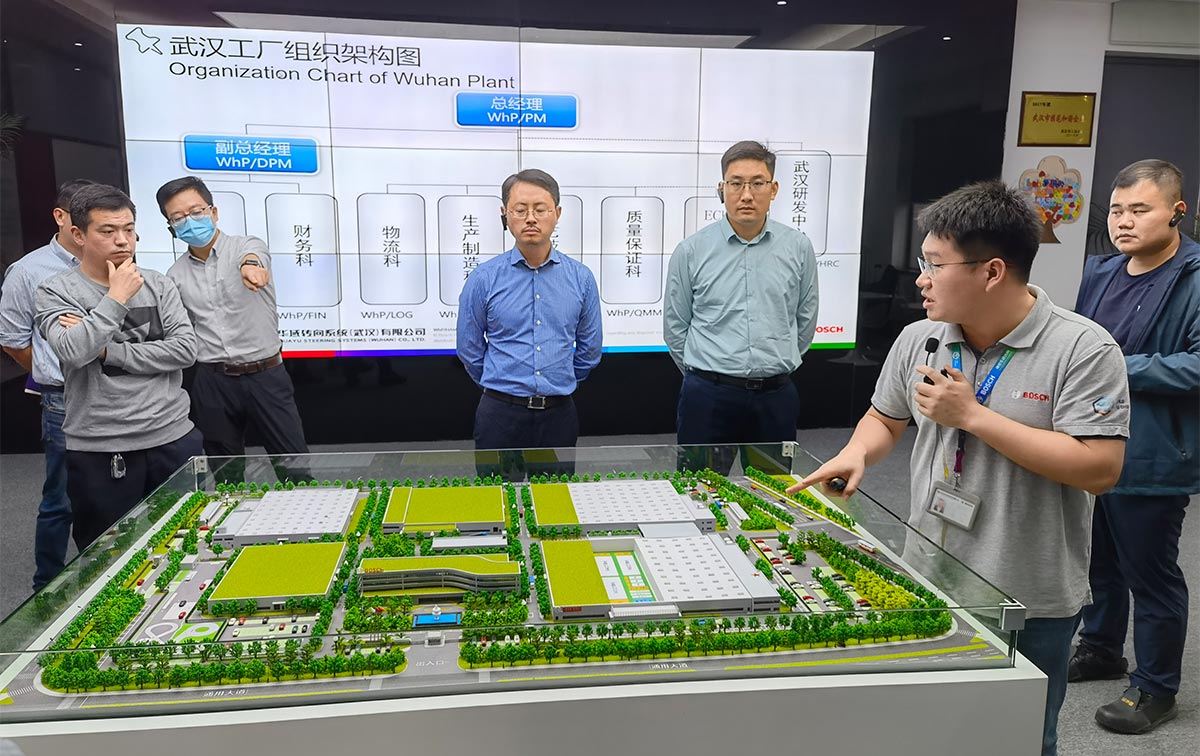
Anwendungsbereich: Automobilindustrie
Herausforderung
Umstellung des Produktionsprozesses von Autokomponenten von der traditionellen diskreten Planfertigung auf eine agile Fertigung auf Abruf; Bewältigung der Personalreduzierung im Werk von 16 auf 2 Mitarbeiter aufgrund der durch Covid-19 bedingten Schließung
Lösung
Konzeption und Implementierung von FITS, einem Transportsystem zur Optimierung des Materialflusses der Schlüsselkomponenten; Kombination von fünf Kernmodulen (MES, APS, FTS, RFID und HMI) verwandelte den Produktionsfluss von dedizierten Fertigungslinien in ein modulares Produktionssystem; Anpassungen während des Lockdowns führten zu flexibleren und hochautomatisierten Prozessen