Ansatzpunkte für eine flexiblere Fertigung in der Automobilindustrie
Von Dr.-Ing. Uwe Steinkötter, Partner, EFESO
In der weiterhin wettbewerbsintensiven Automobilindustrie versprechen modular gestaltete Produktionslinien mehr Flexibilität – sei es, um auf Marktveränderungen schneller reagieren zu können, Ressourcen effizienter zu nutzen oder um Kosten zu senken. Drei Stoßrichtungen sind für den erfolgreichen Aufbau einer modularen Fertigung entscheidend: Flexibilität durch Standardisierung zu erreichen, die Effizienz mit modularen, automatisierten Systemen zu steigern – und Standardisierung als strategisches Operations-Werkzeug über die Fertigung hinaus einzusetzen.
Erhöhung der Flexibilität durch Standardisierung
Hochverkettete Anlagen- und Maschinenparks sind häufig die erste Flexibilitätshürde, mit der Werke konfrontiert sind. Bei Automobilzulieferern sind solche Produktionslinien häufig auf die Anforderungen eines einzelnen Herstellers abgestimmt. Oder sie wurden speziell für diesen konzipiert und nach seinen Vorgaben im Laufe der Jahre modifiziert, was die Anpassungsfähigkeit zusätzlich einschränkt. Zeitgemäß sind jedoch modulare Fertigungsplattformen mit entkoppelbaren Stationen, um verschiedene Fahrzeugmodelle (beim OEM) oder verschiedene OEM-Komponenten (beim Zulieferer) auf derselben Linie produzieren zu können. Dies erfordert in beiden Fällen eine konsequente Standardisierung der Werkzeuge und Komponenten, um die Umstellung auf unterschiedliche Produkttypen bzw. -varianten zu erleichtern.
Zulieferer können zudem mit einer flexiblen Produktionslinie diverse OEMs bedienen, ohne hohe Anpassungskosten zu verursachen. Die bessere Reaktionsfähigkeit bei Veränderungen in der Nachfrage stellt ein weiteres Flexibilitätsziel für die gesamte Branche dar, welches u.a. mit einer Verkürzung der Rüstzeiten erreichbar ist. Die Herausforderungen der Vergangenheit – lange Umrüstzeiten und hohe Stillstandskosten – müssen daher durch strategische Planung und optimierte Prozesse überwunden werden.
Effizienzsteigerung durch modulare Systeme und Automatisierung
Die zweite, wesentliche Dimension des modularen Aufbaus ist die Umrüstung oder die Neuanschaffung von Maschinen und Anlagen. Hier sollten Unternehmen ihre Entscheidungen anhand von Effizienzkriterien treffen, um mit standardisierten und flexiblen Maschinen ihre Investitionskosten minimieren und gleichzeitig eine hohe Produktivität aufrechterhalten zu können. Zugleich sollten sie vorhandene, alte Maschinen in diese neuen Konzepte integrieren, um Re-Use-Potenziale zu realisieren. Bereits jahrelang genutzte Technologien müssen nicht zwangsläufig ineffektiv sein – die richtige Kombination aus alten und neuen Technologien kann die Gesamtanlage optimieren und die Komplexität der technologischen Infrastruktur reduzieren.
Selbstverständlich sind Effizienzsteigerungen eng mit Fortschritten in der Digitalisierung und Automatisierung eines Werkes verwoben. Mit IoT-fähigen Maschinen etwa erfassen und nutzen viele Unternehmen bereits Daten effizient, um ihre Produktionsprozesse zu verbessern. Automatisierung darf jedoch nicht auf Kosten der Flexibilität gehen – technische Lösungen müssen wandelbar bleiben, um Anpassungen schnell vornehmen zu können. Hier lohnt sich insgesamt eine erneute Auseinandersetzung mit den Prinzipien und Leitbildern des Toyota-Produktionssystems, welches auf hohe Eigenverantwortung und Flexibilität anstelle starrer Verkettungen setzt.
„Die richtige Kombination aus alten und neuen Technologien kann die Gesamtanlage optimieren und die Komplexität der technologischen Infrastruktur reduzieren.“
Standardisierung als strategisches Werkzeug
Gerade im Kontext von E-Mobilität und industrieller Nachhaltigkeit bietet die beschriebene Modularität die Chance, flexibel auf neue Anforderungen zu reagieren. Standardisierungen werden nicht nur in der Produktion, sondern auch bei der Entwicklung von Batterien und anderen neuen Technologien notwendig sein. Daher lohnt es sich, die Idee standardisierte Module zu verwenden, über die Fertigung hinaus zu erweitern, um die gesamte Wertschöpfungskette effizienter zu gestalten und zugleich Abhängigkeiten zu reduzieren.
Standardisierung sollte also – drittens – nicht als Einschränkung, sondern als strategisches Werkzeug verstanden werden. Die innerbetriebliche Diskussion darüber muss bei der Produktentwicklung beginnen. Unternehmen sollten prüfen, welche Komponenten tatsächlich benötigt werden und wie bestehende Designs vereinfacht werden können. Schließlich führt eine niedrigere Variantenvielfalt ebenfalls zu geringeren Kosten und einer effizienteren Produktion. Im Idealfall wird diese Betrachtung auf weitere Operations-Bereiche erweitert, etwa bei einer Standardisierung der Läger, der Technologie für Transport- und Ortungsysteme oder beim Muster- und Werkzeugbau.
In Summe verdeutlichen die genannten Punkte, dass der modulare Aufbau von Produktionslinien mehr als nur eine Reaktion auf aktuelle Herausforderungen darstellt; er kann als strategische Notwendigkeit für die Zukunft der Industrie bewertet werden. Unternehmen, die bereits einen modularen Ansatz verwirklicht haben, profitieren deutlich von den genannten Vorteilen. Somit ist das Thema von essenzieller Bedeutung, um die Herausforderungen der kommenden Jahre zu meistern und im Wettbewerb bestehen zu können.
Autor
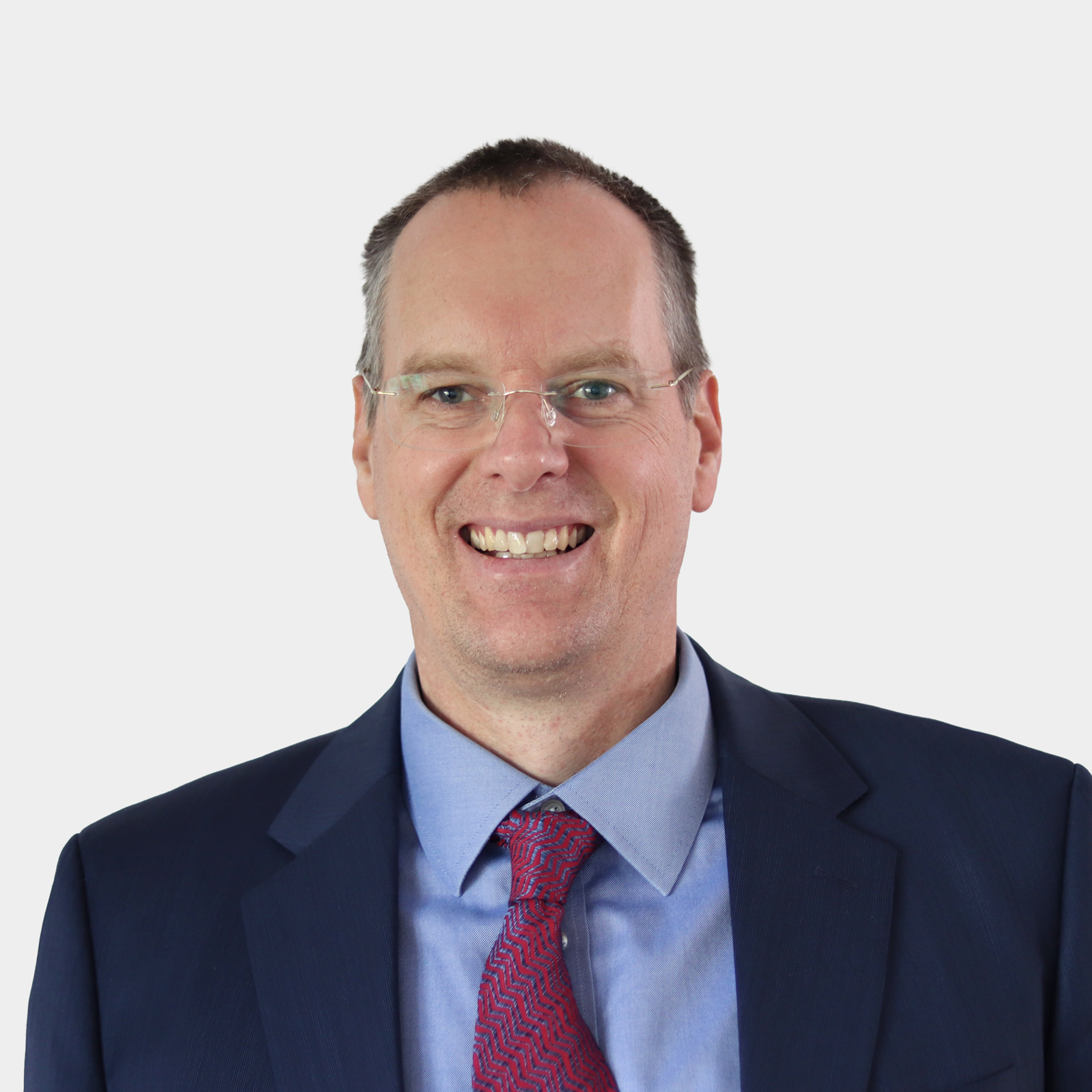
Dr.-Ing. Uwe Steinkötter, Partner, EFESO
Dr.-Ing. Uwe Steinkötter verfügt über umfassende Kenntnisse in der Lean-Implementierung sowie in der Umsetzung von Transformationsstrategien in der Fertigungsindustrie. Vor seiner Tätigkeit als Partner bei EFESO arbeitete er u.a. für die Bosch-Gruppe. Dort hatte er mehrere Führungspositionen zu Operational Excellence, Lean Management, Digitalisierung und Transformation in den Bereichen Mobilität, Konsumgüter und Industrietechnik von Bosch inne.