THEMEN & NEWS
Beiträge und Interviews zu aktuellen Fach-, Technologie- und Branchenherausforderungen, Informationen zu unseren Beratungsangeboten, Seminaren und Events sowie Unternehmensthemen:
Hier erfahren Sie, was EFESO bewegt.
Das menschenleere Lager
Von Dr. Wolfgang Keplinger, ROI Management Consulting AG
Lager und Distributionszentren der Zukunft sind leistungsfähiger, schneller, zuverlässiger, smarter – und vor allem: menschenleer. Denn Roboter sind mittlerweile so günstig und energieeffizient, dass sie den Menschen dort fast vollständig verdrängt haben. Mehr noch: Sie verändern die Art und Weise, wie dort gearbeitet wird. Nicht mehr die Anzahl an Arbeitsschritten ist ausschlaggebend für die Effizienz eines Prozesses, sondern die Betriebskosten des einzelnen Roboters. Die schier unbegrenzte Verfügbarkeit von robotergestützter Arbeit wird somit zum Hebel für riesige Effizienzgewinne und verändert das Aussehen der Lager für immer:
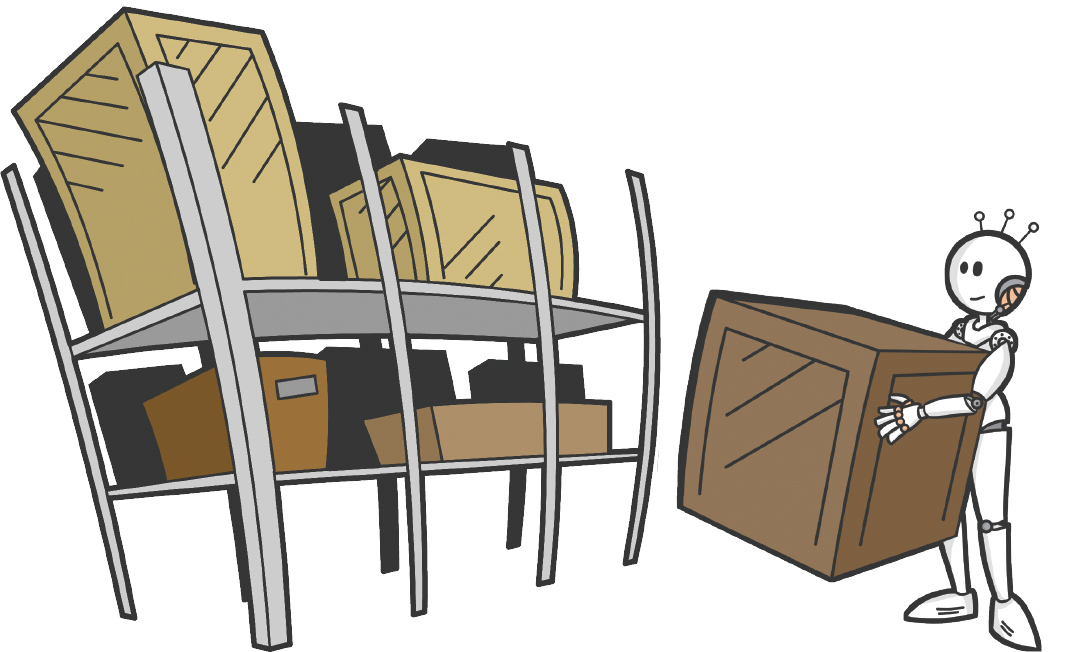
Dynamische Lokalisierung
Das Warehouse 4.0 wird dynamisch, d.h. in Echtzeit wissen, wo sich welche Materialen/Artikel gerade befinden – ob gerade im Zulauf oder schon auf dem Weg zum Kunden. Der Einsatz von RFID und von Beacons erlaubt dann den Einsatz von Smart Boxes, Smart Bins und Smart Racks, mit denen sich jedes Material jederzeit lokalisieren lässt. Werden die Produkte selber immer smarter, benötigen wir nicht einmal mehr die Unterstützung durch die „Logistik-RFIDs“, denn die Lesegeräte im Lager kommunizieren dann direkt mit den smarten Produkten. Durch die Weiterentwicklung der bekannten Lokalisierungstechnologien (wie z. B. DGPS oder UWB) werden zukünftig Methoden wie Geofencing auch innerhalb des Lagers angewendet werden.
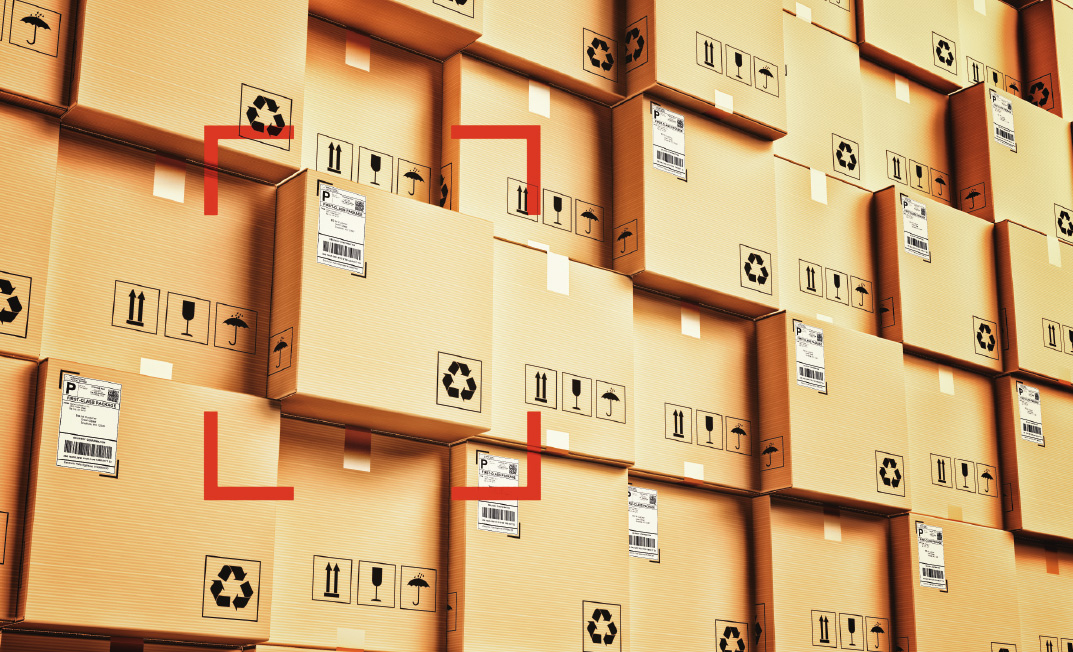
Automatisierung durch Cobots und Picking Robots
Die Lager-Automatisierung in Richtung effizienter Ware-zum-Mann-Systeme ist in den letzten Jahren durch die Entwicklung der Shuttles deutlich vorangeschritten. Ihr Vorteil: Sie sind skalierbar, sie erlauben im Vollausbau mit einem Shuttle pro Ebene und Gang höhere Ein-/Auslagerleistungen als ein Regalbediengerät (RBG) und sie sind relativ unempfindlich, wenn einmal ein Shuttle ausfällt. Da die bewegten Massen deutlich unter denen von RBG liegen, ist die Energiebilanz eines Shuttle-Systems besser als diejenige eines RBG, ein wichtiges Argument in Richtung einer grünen Logistik.
Die schier unbegrenzte Verfügbarkeit von robotergestützter Arbeit wird somit zum Hebel für riesige Effizienzgewinne und verändert das Aussehen der Lager für immer.
Automatically Moved Racks
Eine effiziente Nest-Kommissionierung schafft Amazon mit den vollautomatischen Robotern, die ein ganzes Fachbodenregal selbstgesteuert zum Kommissionierplatz bringen, indem sie unter das Regal fahren und es anheben. Die Vorteile für Amazon: Entfall der Wegezeit – damit erreicht das Unternehmen eine Effizienzsteigerung von 50 bis 70 %. Weitere Vorteile sind die Erhöhung der Lagerdichte (pro Flächeneinheit gelagerte Artikel), die Skalierbarkeit des Systems, die Unempfindlichkeit bei Ausfällen eines Roboters und der niedrige Energieverbrauch. Neben dem von Amazon erworbenen Roboterhersteller Kiva bietet auch Swisslog mit seinem Carry Picker dieses hocheffiziente System für E-Commerce-Anbieter oder Versandhändler an.
Kurze Marktzyklen und volatile Bedarfe zwingen Konzerne und Logistikdienstleister, ihre Lager-Hardware in Zukunft standardisiert, skalierbarer und flexibel zu gestalten.
Zellulare/schwarmbasierte Shuttles
Die Transporte innerhalb des Lagers, vom Lager zum Versandbereich oder vom Lager in die Produktion bzw. wieder retour übernehmen immer mehr AGV/FTS (Automated Guided Vehicles/Fahrerlose Transportsysteme). Die Fahrzeuge wurden in den letzten Jahren kleiner, zuverlässiger und selbstständiger in ihrer Steuerung, zudem kostengünstiger und sicherer – und vor allem unabhängig von fest verlegten Routenführungsmitteln wie Kabeln, Leitungen oder Markierungen. Die Fahrzeuge steuern sich selbst immer zuverlässiger mittels Laser-Scannung und Ausrichtung an fest installierten Orientierungsmarken oder mittels kamerabasierter Umgebungs-/Konturerkennung.
Während heute noch Handlings- oder Übergabeprozesse zwischen den Lager-Shuttles und den AGV zum Weitertransport notwendig sind, könnten die Shuttles zukünftig auch in den Regal-Vorbereich fahren und das gewünschte Material direkt an den Kommissionierplatz oder in die Produktion bringen. Damit entfällt wieder ein „Touch“ mehr aus der Intralogistikkette und wir kommen einem „No-/Few-Touch“-Lager wieder einen Schritt näher. Erste Versuche für ein schwarmbasiertes Shuttle-System, das aus dem Regal heraus direkt an Kommissionierplätze oder in die Produktion fährt, gab es bereits vor einigen Jahren vom Fraunhofer-Institut für Materialfluss und Logistik und der Firma Dematic, die technologischen Unterschiede zwischen dem Regalbetrieb und dem selbstfahrenden Bodenbetrieb machten aber diese Lösung noch nicht wirtschaftlich.
Drohnen im Lager
Drohnen, die im Lager die Inventur durchführen, überraschen heute niemanden mehr. Doch wo heute Drohnen das Lager abfliegen und mit einem RFID-Lesegerät die RFID-Transponder der gelagerten Produkte aktivieren, werden künftig keine brummenden Propeller zu hören sein. Die dynamische Lokalisierung wird diese Einsätze überflüssig machen. Als Transportmittel haben Drohnen jedoch eine große Zukunft: Im Warehouse 4.0 werden sie innerhalb eines Gebäudes oder auch auf offenen Kurzstrecken für einen schnellen und direkten Ausnahme-Express-Transport sorgen. Da könnte eine Drohne dann das dringend benötigte letzte Glied einer Logistikkette liefern, um etwa eine umfangreiche Kundenlieferung zu vervollständigen oder eine Produktion starten zu können. Vorstellbar ist auch der Einsatz von Drohnen in einem räumlich klar beschränkten und umrissenen Lagerbereich, um z.B. Sortieraufgaben (von einem Band in KLTs oder auf Paletten) durchzuführen.
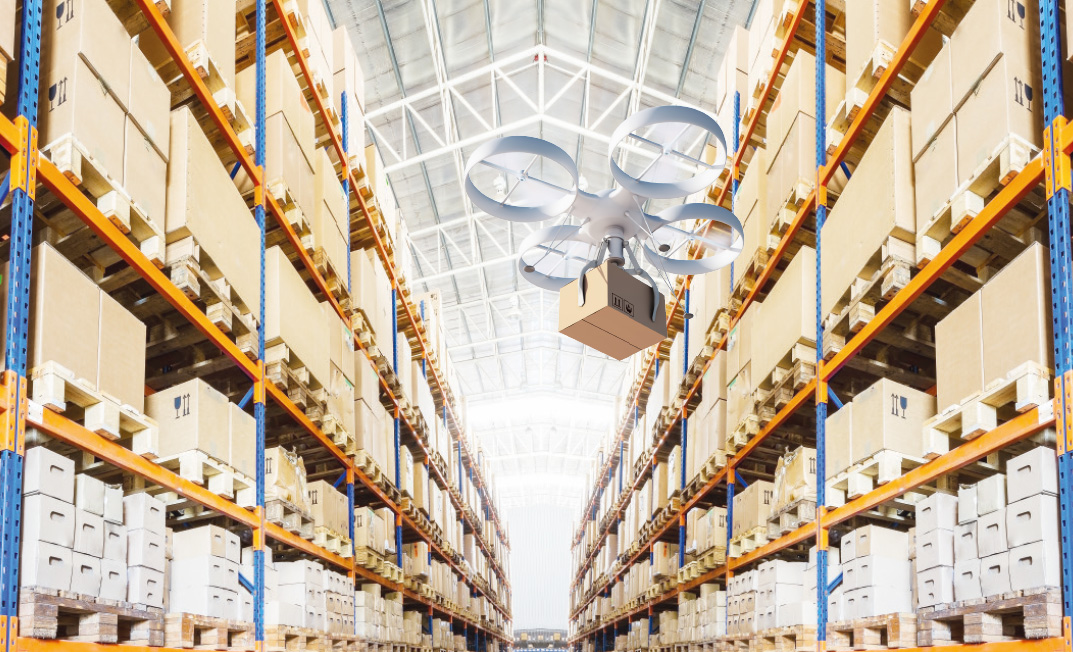
Hubs2Move & Virtualisierung der Lager
Kurze Marktzyklen und volatile Bedarfe zwingen Konzerne und Logistikdienstleister, ihre Lager-Hardware in Zukunft standardisiert, skalierbarer und flexibel zu gestalten. Nur so lassen sich die Lager agil dem sich verändernden Kundenbedarf anpassen. Die weiteren Schritte in dieser Richtung werden dann sein, dass die Lager portabler (Transfer von Standort A nach Standort B) und virtueller werden. In diesem Fall könnte der physische Transport von Produkten zu wesentlichen Teilen durch einen „Transport von Information“ über das Internet ersetzt werden. Die finalen Produkte erstellt der Kunde dann selber mittels Additive Manufacturing/3D-Druck am Ort des Bedarfs.
Das beste Lager ist kein Lager. Die „advanced technologies“ arbeiten daran, die letzten Bastionen des Stapelns und Schichtens zu schleifen. Durch einen Mix aus Lean-Methoden, Digitalisierung, Automatisierung, Mobilisierung und Flexibilisierung verliert das klassische Warehouse nicht nur an Bedeutung, sondern immer mehr auch an physischer Substanz. Der berüchtigte Letzte, der das Licht ausmacht, wird dabei mit hoher Sicherheit kein Mensch sein. Und deshalb wohl erst gar kein Licht gebraucht haben.