THEMEN & NEWS
Beiträge und Interviews zu aktuellen Fach-, Technologie- und Branchenherausforderungen, Informationen zu unseren Beratungsangeboten, Seminaren und Events sowie Unternehmensthemen:
Hier erfahren Sie, was ROI-EFESO bewegt.
The Management Philosophy Affects Lean Principles In China
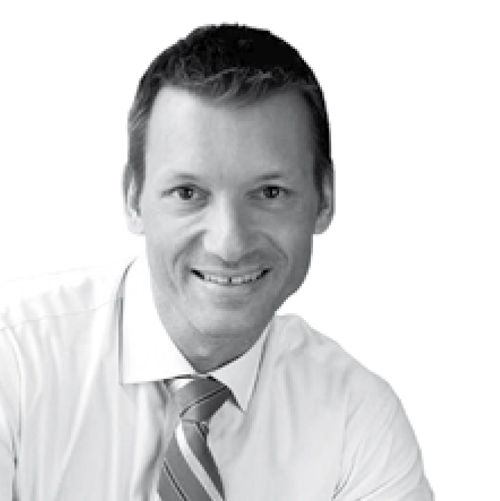
ROI has been executing projects in China for several years and has finally opened its own China office in Beijing in 2012. The office is led by Stefan Weiler who has lived in Asia for eleven years. ROI’s team there is made up of currently 12 consultants, mainly Chinese, coming from renowned international companies like Toyota, ABB, etc. The consulting services focus mainly on quality management, lean manufacturing and supplier development. The broad project experiences allows to share insights on cultural differences and diverse management approaches between European and Chinese companies.
General challenges on the Chinese market accelerate a growing need to implement the Toyota principle
The Chinese economy has shown clear signs of slowing down in the past years. For quite some time many companies haven chosen China because of its low level of wages. However, this advantage seems to be disappearing as wages in China have risen in recent years. From 2000 to 2013, Chinese average real wages grew at an average annual rate of 11.4%. Cost competitiveness is starting to become a real issue for most of the industries in China as the markets will be more competitive and the pressure on cost reduction is growing fast. Some industries, like textile and toys, are already moving out of China to countries like Vietnam or Myanmar.
Additionally, it has been getting more difficult to do business in China. Legislation, obtaining business licenses and residence permits, etc. can be difficult compared to some emerging countries that want to attract new business and are more ‘accommodating’ in this respect. As the market growth is slowing down and companies will have more pressure on reducing costs, manufacturing companies, like automotive OEMs, need to implement more lean concepts across their entire value chain. Companies may also have need to implement lean principles for internal processes, for example reducing purchasingand customer service lead time. The cost of quality has a big impact too. Once many companies thought they could simply move production or source from China, now they realize that they need to have someone constantly monitoring production, which is an add-on-cost. And when quality problems occur, the cost of air freight, etc. to Europe or North America quickly negate the cost advantages.
“The Chinese market is becoming more competitive and the pressure on cost reduction is growing fast.”
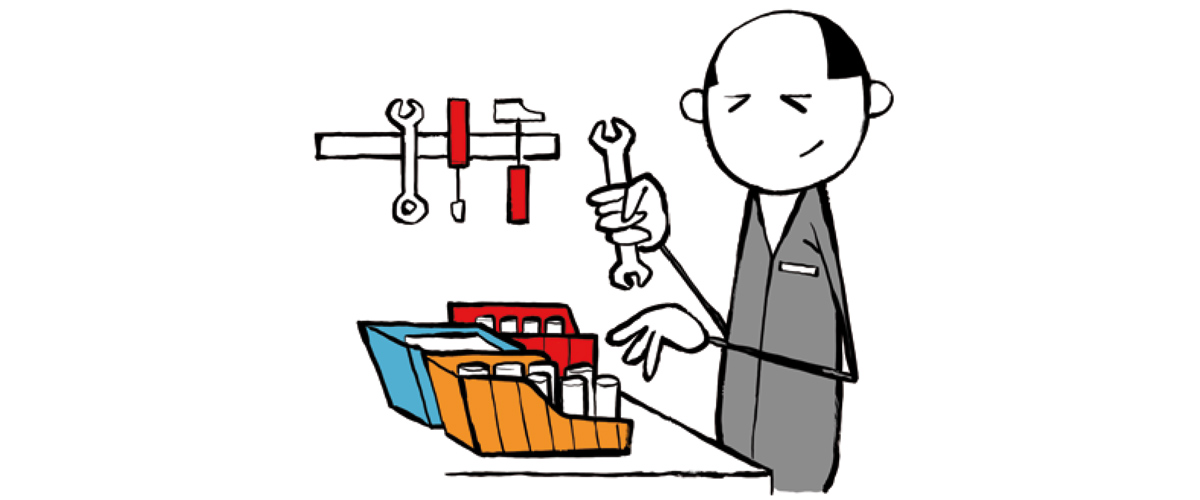
Therefore: only if a Chinese company can demonstrate a robust management system and quality based customer focus while having competitive prices can they compete effectively with other potential suppliers. This is what the implementation of lean concepts in China aims to achieve.
The Chinese perspective on company culture is different
You can find several differences referring to company culture between Chinese and Western European cultures. In Chinese companies there seems to be less focus on goals and objectives in line with the company strategy, and considerably more focus on worrying about keeping the managers happy. Statements about quality or efficiency often just become wall-paper that the employees walk past every day.
Chinese people are used to following their leaders, so management in different levels should provide complete, real and visible support for lean production concepts. Primarily, top management commitment is necessary for sustaining the program.
As the implementation of the Toyota Production System (TPS) is rather based on decentralized and autonomous decision making with a focus on achieving highest quality Standards, it needs a lot of time and convincing efforts to make it work in Chinese companies. In Joint Ventures between Chinese and Western / Japanese companies the implementation of lean Standards is easier to achieve, as you find a different mindset there more often.
Many enterprises which started to deploy lean at the ‘tool level’ with no relation to business strategy failed. And, even worse, some employees including some leaders don’t know their business strategy at all, which prevents them from combining lean production thinking with the daily work.
Success factors for lean principles in China
To successfully implement TPS, an official team must be set-up and the team leader must be supported by senior management as the managerial aspect of lean is just as important as or even more important than the production tools or methodologies in China.
There has to be 100% conviction and belief from the managers, the clear idea of ‘walking the walk’ and leading by example are paramount. Only if the employees at any level can clearly see and understand what is important to their managers, it will become important to them. In China you cannot have a ‘do as I say – not as I do attitude’ and expect people to take you or your demands seriously. A successful implementation of any lean tool is closely related to the management philosophy. Nobody can succeed by imitating and copying practices of others indiscriminately, they must be combined with the local culture.
Many Chinese enterprises hope to achieve quick results and act rashly, which only allows them to stay on the surface. They won’t succeed at all, e.g. if a quality problems occurs, because often there is not enough time spent on a proper root cause analysis. People jump directly to any solution which promises to solve the problem quickly, but there is no sense in trying to find a sustainable solution.
In contrast, the success of TPS in Japan is closely related to the long term employment system. The situation in China is on the contrary where the fluctuation of people is very high.
Central role of Toyota principles in global production networks
Clearly centrally defined and described methodologies, Standards and definitions of KPIs have to be in place to align the whole global production network according to the same guidelines and principles.
A lean system makes it clearly easier to manage production expansion with higher flexibility over the short and medium term and to be able to respond to market shifts and the rise of complexity.
Nevertheless, the real implementation of lean concepts has to be done country specific. Wherever you are, in China, India or Europe you have general lean production concepts – but how to apply them to the current situation will be different.
The strength of TPS is, that it focuses on ‘inputs’. Everything entering the production network must occur in the right quality and quantity. This makes the overall system quite easy to manage, if every contributor knows about quality and quantity requirements and has actions in place to support that. As a result the whole system is easier to manage and achieving the right outputs is easier as well. And this counts worldwide.
“Chinese people are used to following their leaders, so management in different levels should provide complete support for lean production concepts.”