THEMEN & NEWS
Beiträge und Interviews zu aktuellen Fach-, Technologie- und Branchenherausforderungen, Informationen zu unseren Beratungsangeboten, Seminaren und Events sowie Unternehmensthemen:
Hier erfahren Sie, was ROI-EFESO bewegt.
Best Practices
Für hochspezialisierte Unternehmen aus dem Maschinen- und Anlagenbau führt der Einstieg in das digitale Produkt- und Servicegeschäft meist nicht direkt über radikale Geschäftsmodellinnovationen oder offene gemeinsame Plattformen, sondern über Produktnahe Services und ergänzende digitale Lösungen. Sie erweitern die Kernfunktionen der Maschine um digitale Zusatzleistungen und ermöglichen dadurch radikale Effizienzsprünge. Das Spektrum reicht von Hardware-unterstützten Lösungen bis hin zu rein Software-basierten Diensten. Dabei zeichnen sich Digitale Hard-, Software- und Servicelösungen meist durch eine gemeinsame „Anatomie“ aus. Sie ...
... erweitern die Funktionen physischer Produkte unter Ausnutzung undefinierter digitaler Technologieimpulse, wie etwa Deep Learning, Cognitive Systems oder innovativer Mikrosystemtechnik;
... basieren auf der Bereitstellung, Analyse und Interpretation von Betriebs-, Zustands- und Umgebungsdaten der Maschine in Echtzeit;
... unterstützen durch beschreibende, prognostizierende oder vorschlagende Analysen auf Maschinen- oder Prozess-Ebene eine intelligente Entscheidungsfindung oder sind direkt eingebettet in autonome, selbstentscheidende Systeme;
... tragen durch einen höheren Automatisierungsgrad, Qualitätsverbesserungen und eine Verkürzung der Stillstandszeiten zur Hypereffizienz von modernen Anlagen- und Maschinenparks bei.
Digital Operator Support
Best Practice: Robert Bosch GmbH
Der digitale Operator Support zur Unterstützung von Anlagenführern vernetzt die Daten der eingesetzten Maschinen mit den Wissensdatenbanken und dem Fernwartungsdienst des Herstellers. Auf diese Weise werden eintretende Störfälle umgehend klassifiziert und über eine App Lösungsanleitungen vorgeschlagen, die der Bediener der Anlage selbstständig oder bei komplizierteren Fällen zusammen mit dem Kundendienst via Fernwartung umsetzen kann. Dadurch können Stillstandszeiten und Wartungskosten reduziert und die Gesamtanlageneffektivität (OEE) erhöht werden.
Digital Assistant System
Best Practices: Airbus, Robert Bosch GmbH, Amazon
Digitale Assistenzsysteme ermöglichen ungelernten Arbeitskräften die Ausführung komplexer manueller Prozessschritte in rascher Abfolge sowie eine lückenlose Dokumentation ausgeführter Tätigkeiten in Echtzeit. Sie bilden damit die Vorstufe zur Automatisierung und werden dort eingesetzt, wo heute noch keine taktilen, sensitiven oder kognitiven Robotikfähigkeiten vorhanden sind. Dadurch können Personal und Qualitätskosten gesenkt sowie die Arbeitstaktung erhöht werden.
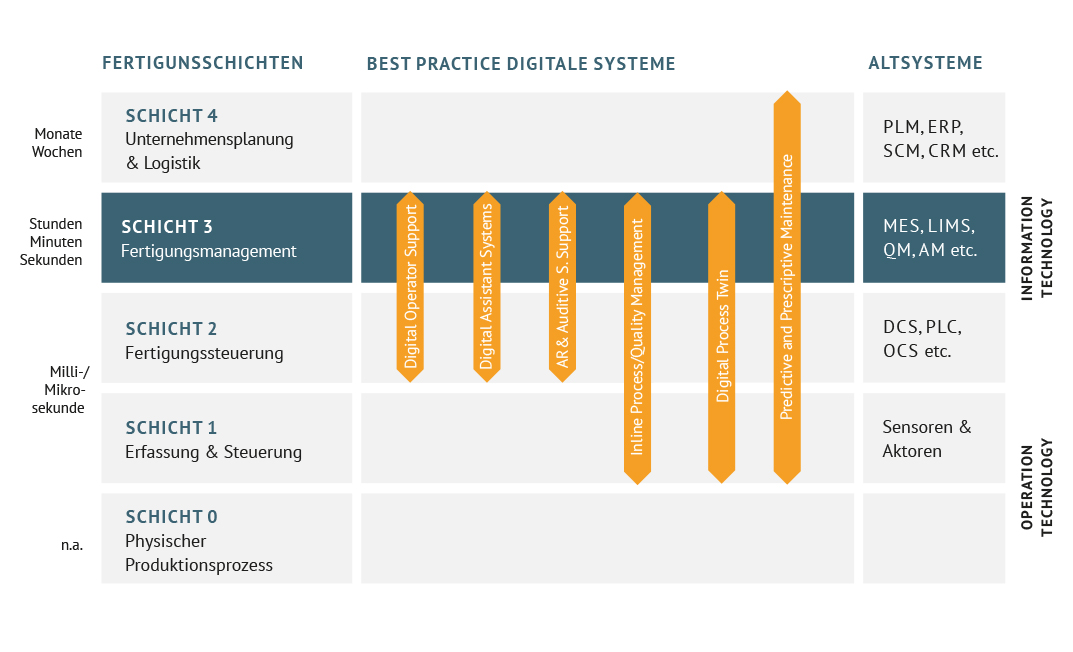
Augmented Reality Service Support
Best Practices: Palfinger AG, ABB, Körber AG
AR-Anwendungen und auditive Wearables unterstützen die selbstständige Ausführung von Anlagenwartungen und -reparaturen durch den Betreiber. Im Rahmen des Augmented Reality Service Support werden einzelne Maschinen und mögliche Störfälle selbstständig erkannt, visuelle und auditive Arbeitsanweisungen gegeben, Wartungs- und Reparaturvorgänge automatisch dokumentiert und Remote Support/Mentoring angeboten. Dadurch können Wartungs-, Reparatur- und Stillstandzeiten reduziert, Personalkosten gesenkt und eine höhere Mitarbeitersicherheit gewährleistet werden. AR wird zudem bei der Simulation der Anlage oder Maschine sowie bei der Schulung des Bedienpersonals eingesetzt.
Predictive & Prescriptive Maintenance
Best Practices: Thyssenkrupp Aufzüge, GEA, Kapco Global, Aerospace Distribution
Predictive Analytics beschreibt die vorausschauende Erkennung und Vorhersage potenzieller Störfälle auf Basis von Zustands- und Umgebungsdaten. Dabei kommen Machine-Learning-Algorithmen zum Einsatz, die auf Basis bereits erkannter Probleme kritische Datenmuster automatisch identifizieren. Im Rahmen von Prescriptive Maintenance liefert die Maschine eigenständig Handlungsempfehlungen und Vorschläge, wie ein vorhergesagtes Ereignis verhindert werden kann. Ausfall-, Wartungs- und Ersatzteilkosten können dadurch reduziert, Verfügbarkeit und Umsatz erhöht werden.
Inline Process/Quality Management
Best Practice: Rhenus Lubs
Beim Inline Process bzw. Quality Management werden Prozessparameter unter Berücksichtigung vorherrschender Einflussfaktoren im laufenden Prozess so optimiert, dass ein genau festgelegtes Produkt erzeugt wird. Dadurch können Fertigungsprozesse detailgenau reproduziert, Durchlaufzeiten reduziert und Qualitätskosten minimiert werden.
Digital Process Twin
Best Practices: Klingelnberg GmbH, Bilsing Automation GmbH, Biohort GmbH
Das digitale Abbild eines realen physikalischen Fertigungsprozesses beschreibt Merkmale und Eigenschaften eines Bauteils entlang der gesamten Prozesskette. Somit können für jeden Prozessschritt Merkmale und Eigenschaften definiert und bei Abweichung korrigierend eingegriffen werden – Gleiches gilt für das Einrichten von Werkzeugen. Qualitätskosten und Durchlaufzeiten können dadurch reduziert und Fertigungsinvestitionen besser validiert werden.